The utilization of hydrogen as the primary energy carrier in the 21st century is rapidly gaining momentum. Numerous countries are earnestly trying to establish a new, eco-friendly hydrogen economy and implementing national decarbonization strategies and sector coupling.
The expansion and integration of chemical, petrochemical, and steel industries and fuel production are expected to trigger a massive development of production and transportation capacities throughout the 2020s.
Plans are underway to introduce significant new storage capacity and import structures for liquid and gaseous hydrogen. Existing distribution networks and pipelines are expanding to encompass cross-border and cross-industry cooperation projects.
Modern electrolyzers for hydrogen production are scaling up from the one-digit to the two- and three-digit megawatt range, further driving the growth of the hydrogen industry. The number of power-to-gas projects in Germany continues to grow steadily.
Approximately three-quarters of all matter consists of hydrogen atoms, the smallest and lightest molecule with a substantial volume and extreme volatility.
Despite its flammability and little explosiveness, the gaseous H2 can discharge significant energy without producing greenhouse gases, making it a precious substitute for fossil fuels.
Compared to one kilogram of petrol, one kilogram of H2 contains 2.8 times more energy. The efficient and safe compression of hydrogen is made possible through various types of compressors, which can provide the necessary volumes and pressures for industrial applications cost-effectively.
In addition to the conventional reciprocating and diaphragm compressors used for pressures in the three-digit bar range, screw compressors are particularly useful and economically advantageous for low-pressure applications, especially with fluctuating operating conditions and increasing volume flows.
Wet Hydrogen Gas from Water Electrolysis
Natural gas and coal are the primary sources of hydrogen, but water use as a hydrogen carrier is expected to increase significantly in the future.
Several natural sources are available for the large-scale production of hydrogen. Electrolyzers are used to split water with electricity and generate around 200 Nm³/h H2 (equivalent to approximately 18 kg/h) and 100 Nm³/h O2 per megawatt of input power.
Depending on the type of electrolyte used or whether a solid or liquid electrolyte is utilized, between 0.01 and 0.5 vol.% of the respective other molecule remains, along with a temperature-dependent water loading of up to 60% in the saturated H2 or O2 mass flow.
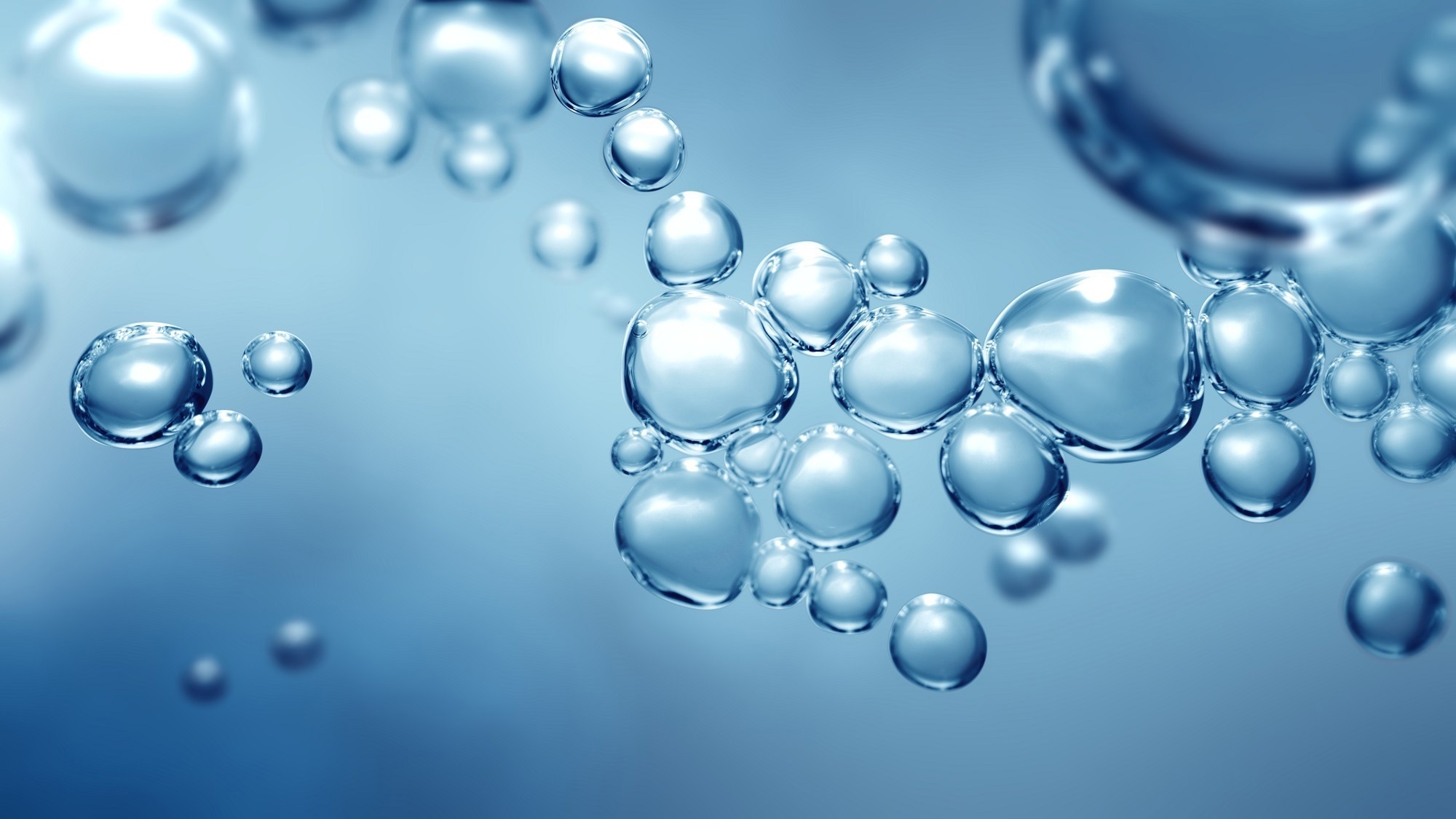
Image Credit: Aerzener Maschinenfabrik GmbH
Compressor manufacturers must consider the water content present in the hydrogen gas, which can be compressed or separated significantly by pre-drying methods, such as refrigeration drying. The hydrogen gas purity required varies depending on the end consumer's application.
For applications with the highest purity requirements, such as fuel cells requiring a purity level of 5.0, de-oxo dryers minimize the gas's oxygen and moisture content. These de-oxo systems can be correspondingly small and cost-effective after pre-compression.
In contrast, for other hydrogen-consuming processes, such as iron ore reduction, the production of basic chemicals, or feeding into natural gas networks, the tolerances and limit values for foreign components in the H2 gas can be significantly higher. This simplifies the overall process in terms of process technology and reduces costs.
It is advisable to have a technology-open, application-oriented process design from an economic and operational perspective. This will ensure that the needs of the participants are adequately addressed, and supply can be effectively complemented.
Screw Technology: Versatile and Reliable
Rotating positive displacement compressors, such as screw compressors, have been reliable and flexible in demanding gas applications since the latter half of the 20th century.
Their design features enable internal compression without free mass forces and make them insensitive to fluctuations in operating conditions, leading to low-pulsation compression behavior. As a result, screws require low maintenance intensity and have comparatively low operating costs for both full and partial load operation.
Screw compressors consist of a primary rotor and a second rotor that continuously rotates and moves gas portions from the suction side to the discharge side, where they are discharged against a smaller outlet geometry.
The main rotor is typically responsible for driving the compressor, while the secondary rotor forms the compression chamber and provides sealing. These compressors can be categorized into oil-free and oil-flooded types and used in single or multi-stage concepts for hydrogen applications.
Due to their design and differences in circumferential speed of the rotors, differential pressure, and delivery volumes, they have different working ranges. The following figures illustrate the main differences and show the work areas in relation to each other:
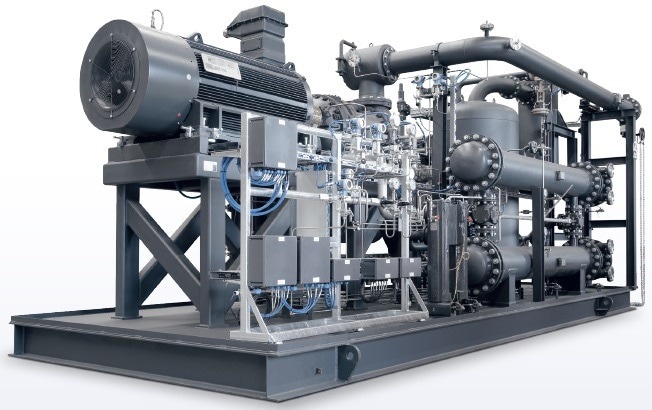
Image Credit: Aerzener Maschinenfabrik GmbH
Oil Flooded:
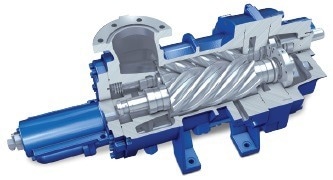
Image Credit: Aerzener Maschinenfabrik GmbH
- The whole interior is submerged in oil, resulting in a compact design with shorter bearing lengths
- The primary rotor is driven and rolls directly onto the revolving secondary rotor (oil lubrication film must not tear)
- The most intense differential pressures and bearing loads
- Reduced circumferential velocity and volume
- Wet gas must be compressed above the dew point to avoid water condensation into the oil
- Pre-drying makes sense in terms of operating costs and oil service life
- A variant with an oil-lubricated control cylinder is available (volume flow regulation at constant speed and pressure; functions as an internal bypass and may also be used as a start-up unloader).
Oil-Free (water-injected):
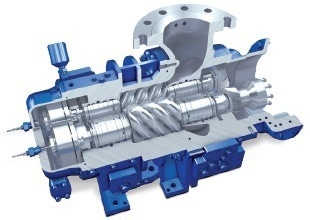
Image Credit: Aerzener Maschinenfabrik GmbH
- 100% oil-free conveying chamber; water injection for cooling and gap sealing
- Driven main rotor without contact with the secondary rotor; synchronization through gear pair
- Higher circumferential speed and volumes
- Oil chambers are divided by separating seals, resulting in longer bearing distances
- Reduced bearing loads and differential pressures
- No need to compress wet gas over the dew point
- Pre-drying, dew points are irrelevant
Oil-Free (dry):
- 100% oil-free conveying chamber, although barrier medium permeates the conveying chamber
- The main rotor is driven without contact with the secondary rotor; synchronization through the gear pair
- Differential pressures are constrained by the maximum temperature development or the discharge temperature (no internal cooling medium)
- Conveying chamber gas or liquid-locked seals (own medium as sealing gas also possible)
- Maximum circumferential velocity and volume
- It is not necessary to compress wet gas above the dew point
In all types of screw compressors, it is possible to control the volume flow by adjusting the speed using a frequency inverter. The choice of bearing is critical and determines the minimum speed (journal bearing) or the balancing forces (roller bearing) first.
Under constant torque, load changes of about 1 Hz/s are standard across the entire control range. Efficiency and delivery rates increase with reduced internal gaps between the rotors, housing, and bearings (including gaps between rotors and control slides in the case of oil-flooded machines with control slides) and better sealing.
Gap losses are higher with increased differential pressure and lower gas density, so injecting a fluid, such as oil or water, cools and seals the gaps.
The injection medium reduces the temperature difference, shifting from isentropic compression to isothermal compression and a corresponding state change in the PV diagram. These technical labor savings result in lower specific energy requirements and increased efficiency.
Wet oxygen generated during water electrolysis must also be utilized, and AERZEN booster blowers suit this purpose.
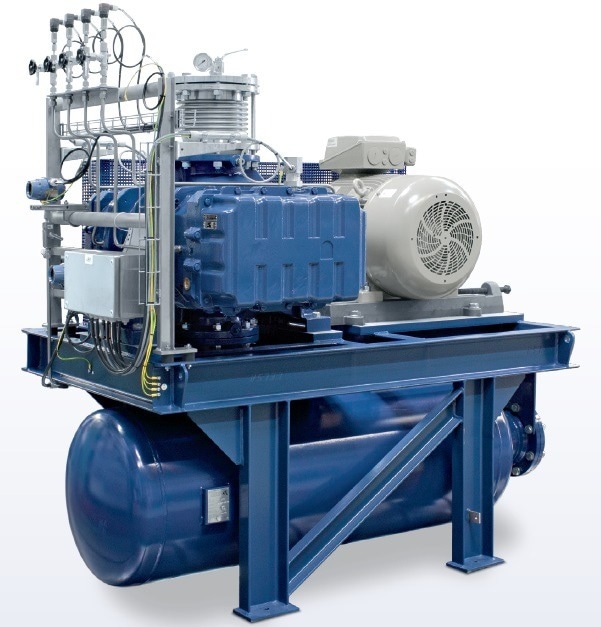
Image Credit: Aerzener Maschinenfabrik GmbH
Technology Selection Based on Application
Process and product requirements vary widely by application and end user in terms of the required purity and reliability, the mode of operation and cost sensitivity.
The residual contents of water, oxygen, and oil aerosols are critical limit values that may have a significant impact on the acquisition and operating costs, sometimes requiring the use of oil-free compressors or additional fine separators for oil-flooded machines.
Compared to other compression technologies, screw compressors can handle high-volume flows with relatively small footprints and lower investment costs. Moreover, the use of compactly designed screw packages further increases this advantage by minimizing additional groundwork and building costs.
Screw compressors offer the best techno-economic solution in the low-pressure range.
Solutions Made by Aerzen
AERZEN has been providing a wide range of process gases with both oil-flooded and oil-free compressor series for several decades. The company's consulting services are characterized by multiple perspectives and benefit from field and service experience with both technologies.
AERZEN has cooperated with reciprocating or diaphragm compressor manufacturers to optimize overall compressor concepts in the interest of the customer. In addition to screw compressors, AERZEN offers Roots-type process gas blowers in various pressure ranges.
These can transport wet oxygen from water electrolysis to industrial customers, such as wastewater treatment plants, cement works, or glass producers, promoting sector coupling.
All machine types are integrated into fully functional assembly concepts and consistently aligned with the operator's requirement profile. AERZEN offers both standardized and highly customized individual solutions to meet customers' specific needs.
For more information, customers can refer to AERZEN's current brochures or customer presentations. Reference lists and technical documents of typical solution concepts can be obtained by sending a request (RFQ) to [email protected].
AERZEN: Compression is the Key to Success
AERZEN, founded as Aerzener Maschinenfabrik, was established in 1864. A significant milestone was achieved in 1868 when the first positive displacement blower in Europe was built.
AERZEN introduced the first turbo blowers in 1911, screw compressors in 1943, and rotary lobe compressor package in 2010, which was a world-first innovation.
These pioneering inventions have continued to propel the advancement of compressor technology, and today AERZEN stands among the leading manufacturers of positive displacement blowers, rotary lobe compressors, screw compressors, and turbo blowers globally.
AERZEN's products are highly acclaimed and enjoy a dominant market share in several fields of application. With more than 2,500 proficient employees working diligently across 50 subsidiaries worldwide, AERZEN is committed to shaping the future of compressor technology.
The company's triumph is rooted in the technical proficiency of its skilled professionals, global network of experts, and valuable customer feedback. AERZEN is renowned for delivering unrivaled reliability, value, and efficiency in its products and services.
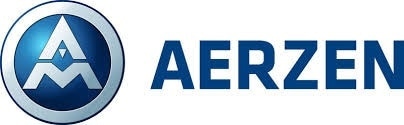
This information has been sourced, reviewed and adapted from materials provided by Aerzener Maschinenfabrik GmbH.
For more information on this source, please visit Aerzener Maschinenfabrik GmbH.