Monitoring total organic carbon (TOC) is an excellent way to make sure that industrial processes are all under control and that equipment is protected. However, this may not be helpful if the TOC instrument is not dependable or if the TOC results cannot be trusted.
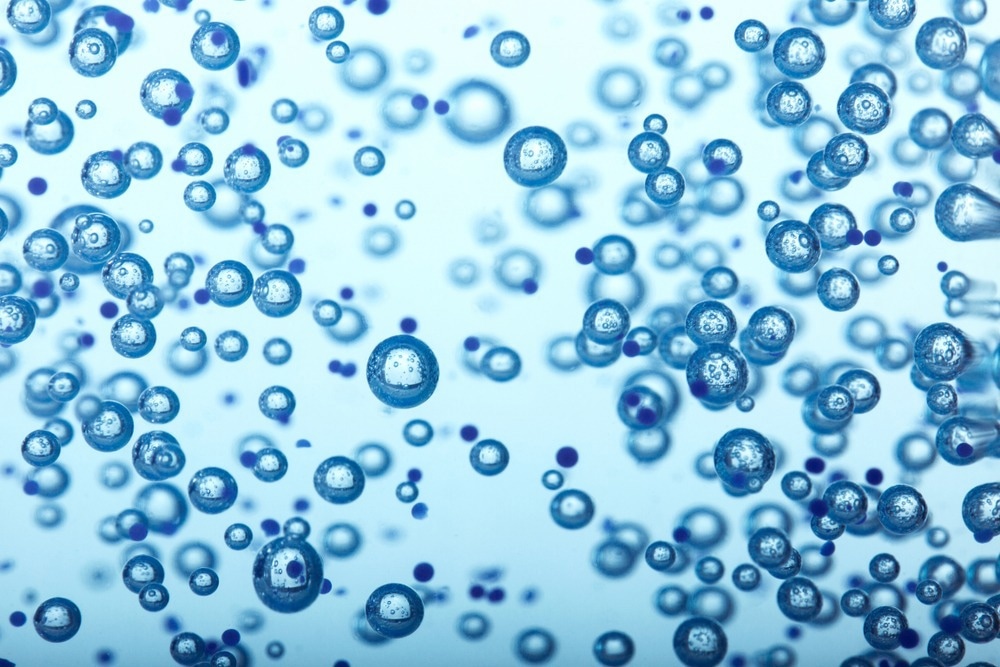
Image Credit: NiNell
The primary purpose of organics monitoring tools is to identify any issues early and alert users when something goes wrong with a process or water quality. Therefore, the tools used should be reliable and provide information quickly when attention is required.
Online instrumentation for TOC analysis is valuable for detecting process upsets or leaks. Nevertheless, it can become a burden if it is not responsive, reliable, and robust.
The seamless operation of a TOC instrument is essential for monitoring industrial processes, including easy maintenance and troubleshooting, to avoid downtime or product loss, ensuring optimal production while complying with regulations.
It is crucial to keep the process in control while preparing for possible process upsets. Thus, promptly detecting these sorts of events will facilitate corrections before they develop into more significant problems.
TOC monitoring is a powerful tool for preventing product loss, avoiding regulatory fines, and detecting leaks when the appropriate technology and support are available for the application at hand.
For over 30 years, the Sievers team has assisted thousands of customers worldwide with their TOC monitoring requirements, enhancing their operations and instilling confidence in their organics monitoring program.
It is imperative to avoid using a process monitoring tool that does not meet your needs. Outlined below are five issues to avoid when performing TOC analysis for industrial processes:
- Not having the right tool for the application at hand. The quality of samples and the TOC technologies used for analysis vary significantly. Hence, it is crucial to select the appropriate tool for your application and ensure that the technology used is suitable for its intended purpose.
For instance, incomplete oxidation or the inability to handle complex-to-oxidize compounds can result in incorrect outcomes, instrument clogging, or increased maintenance in many industrial TOC monitoring applications. It can be challenging to determine if complete TOC recovery is achieved or if an excursion, leak, or change in process is being detected.
Choosing TOC technology that can effectively handle challenging process streams will ensure that any process deviations are promptly identified, offering peace of mind.
- Unreliable measurement results. The reliability of TOC data is of utmost importance. Users should not have to concern themselves with the functionality of their instrument, the effectiveness of their consumables and reagents, or the accuracy of their maintenance practices.
A reliable analyzer should deliver not only precise measurements and straightforward maintenance procedures but also offer self-diagnostic capabilities, intelligent sensors, and automated functions like rinsing and verification.
Customizable features and add-ons tailored to specific applications can enhance response times, accuracy, sample handling, and overall performance, providing users with a comprehensive understanding of their system.
By maximizing uptime, eliminating concerns over consumables, and simplifying analyzer use and maintenance, users can be confident in their data and be prepared to take decisive action.
- Worrying about calibration frequency and corresponding downtime. Calibration is a crucial aspect of owning instrumentation, as it is necessary to validate monitoring systems and verify their performance. Nonetheless, frequent calibration requirements can result in analyzer downtime, leading to a loss of critical data.
A robust design can mitigate this issue by decreasing the calibration frequency, which in turn reduces the costs and resources associated with maintenance and enhances uptime.
The use of automated calibration and check standards enables users to ensure optimal performance and maximize uptime without any uncertainty or concern regarding the status of their instrument.
- Maintenance can be challenging and time-consuming. Performing routine maintenance should not be a complicated task that requires extensive training. Instruments that are designed in a simple and modular way, and are easy to navigate, can make it easier for users to carry out preventative maintenance and avoid situations where repairs are needed.
- Dissatisfaction with the level of TOC expertise and support from manufacturers. It is crucial to feel confident and have a clear understanding of the process, from technology selection to implementation and routine usage, when selecting the best TOC analyzer for a given application.
Acquiring TOC expertise enables users to determine configuration requirements and customize a solution that satisfies their monitoring needs. Additionally, having access to ongoing support from the TOC manufacturer can help address minor issues before they escalate.
Collaborating with TOC experts for commissioning, method development, preventative maintenance, and on-site repairs can ensure that the monitoring program is established for success.
If an issue arises during a process, having a dependable monitoring tool is essential. Without an appropriate tool for the application, there is a risk of missing vital data or mistrusting the received alerts.
This can result in various issues, such as product loss, quality concerns, equipment failure, downtime, regulatory fines, and more, which could be prevented or minimized. An effective method to detect process upsets in different applications is TOC monitoring. Thus, users can have peace of mind that they will be alerted whenever there is an issue.
With the right organics monitoring tool for your application, you can trust that your TOC instrument will function efficiently, and you can focus on other priorities. You can be confident that your TOC instrument is responsive and reliable and that you will receive the required information on time.
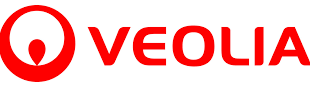
This information has been sourced, reviewed and adapted from materials provided by Veolia Water Technologies & Solutions.
For more information on this source, please visit Veolia Water Technologies & Solutions.