In this interview, AZoCleantech talks to Kelly McPartland about using optically enhanced Fourier Transform Infrared Spectroscopy (OE-FTIR) to monitor Ethylene Oxide levels and emissions.
Please could you introduce yourself and your role at Thermo Fisher Scientific?
My name is Kelly McPartland, and I serve as the Senior Applications Manager for Gas Analysis Solutions at Thermo Fisher Scientific. Since 2015, I have been extensively involved in FTIR gas analysis. Over the past three years, I have focused on monitoring ethylene oxide (EtO) source emissions.
What is FTIR, and why is it important in gas analysis?
FTIR, short for Fourier transform infrared, represents one of the most common forms of infrared spectroscopy. Initially developed for commercial use in the 1960s, FTIR spectrometers were primarily utilized in advanced research applications due to high instrument costs and the need for large computers to operate them.
Over time, the FTIR technology has evolved, reducing costs and improving overall FTIR capabilities. Consequently, FTIR spectroscopy has become the standard method for identifying organic compounds in academic, analytical, QC/QA, and forensics laboratories.
FTIR technology has proven effective in various applications, such as in-line processes, batch sampling, gas purity/certification, emissions testing, and ambient air monitoring. Optically enhanced FTIR (OE-FTIR) has expanded its usage in gas analysis, particularly in scenarios requiring very low detection limits.
What advantages does the introduction of FTIR-based continuous emissions monitoring (CEM) give you?
FTIR-based continuous emissions monitoring (CEM) systems have several advantages over other techniques, particularly gas chromatography (GC). One notable benefit is the speed.
Unlike GC-based methods that involve batch sampling, FTIR-based CEM utilizes a continuous flow through the gas cell, enabling constant sample probing with the infrared (IR) beam. This results in a faster response time and more data points.
The Thermo Scientific™ EMS-10™ represents a four-channel CEM system that can measure a single sample channel in approximately 30 seconds. The typical data collection rate is once a minute when monitoring a single stack on one channel.
This system's sensitivity is a significant advantage as it incorporates the Thermo Scientific™ MAX-IR™ FTIR Gas Analyzer with the advanced Thermo Scientific™ StarBoost™ Optical Enhancement Technology (OE-FTIR).
The StarBoost technology greatly enhances the sensitivity of the FTIR analyzer, allowing real-time detection limits comparable to GC mass spectrometry (GC-MS) techniques.
Selectivity is another critical advantage. GC-based methods may face misidentification issues due to coeluting peaks, but FTIR-based CEM overcomes this challenge. For example, detecting ethylene oxide (EtO) can be difficult as its molecular weight is the same as propane, acetaldehyde, and CO2, leading to coelution and misidentification.
Another significant benefit is stability. Utilizing a unique zeroing technique within the Thermo Scientific™ MAX-OXT thermal oxidizer module, we effectively eliminate biases caused by interferences. Our specialized data acquisition method, Auto Reference, also efficiently eliminates baseline drift.
FTIR analyzer boasts minimal calibration drift and comes factory calibrated. It comes equipped with a comprehensive quantitative library, including a resident EtO calibration, ensuring no recalibration is necessary in the field. This singular calibration remains effective throughout the instrument's entire lifetime.
The technique's robustness sets it apart as a superior choice. With minimal maintenance requirements, the system offers an extended operational lifespan. The MAX-iR FTIR gas analyzer's spectrometer has a remarkable mean lifetime of 10 years before experiencing failure.
The analyzer provides exceptional value with its remarkably low cost of ownership. Running continuously for extended periods, it proves highly cost-efficient. However, we recommend a yearly preventative maintenance visit to clean the gas cell, check the signal and other diagnostics, and change the diaphragm on the pump.
Why is monitoring ethylene oxide (EtO) an excellent example of the MAX-iR analyzer’s capabilities?
Video Credit: Thermo Fisher Scientific – Environmental and Process Monitoring Instruments
Ethylene oxide (EtO) possesses both carcinogenic and mutagenic properties. The chemical industry commonly employs it to sterilize medical instruments and as a reaction intermediate for ethylene glycol production. Industries in North America, as well as in countries like Japan and Germany, frequently utilize EtO.
Its extreme reactivity makes it one of the most challenging gases to analyze. Consequently, transporting EtO samples from the stack to the analyzer poses difficulties.
To overcome these challenges, the MAX-iR FTIR Gas Analyzer, combined with StarBoost optical technology, allows users to achieve exceptional detection limits ranging from single-digit parts per billion (ppb) to tens of parts per trillion (ppt). This innovative breakthrough preserves all the benefits of real-time FTIR analysis.
The MAX-iR analyzer eliminates the need for costly methods, such as MS, GC, or cavity ringdown spectroscopy (CRDS), across various applications. Notably, the MAX-iR analyzer can analyze EtO for trace analysis and hundreds of other gases, making it an ideal and versatile tool.
Why is it important to measure ethylene oxide in the environment?
The presence of ethylene oxide has been detected at low levels in the air in numerous areas of the United States, with some areas located near industrial plants and others not. People working in or living near industrial facilities that release EtO are likely to face higher exposure levels to the gas.
EtO has been classified as a known human carcinogen by the US Environmental Protection Agency (EPA). Prolonged occupational exposure and inhalation of EtO have been determined to induce a carcinogenic response.
Recent studies suggest that its toxicity could be even greater than previously believed, emphasizing the importance of real-time detection of EtO at the lowest possible levels.
How are ethylene oxide source emissions typically measured?
Because of its toxicity, there exists significant interest in monitoring Ethylene Oxide (EtO) at exceptionally low levels in and around the previously mentioned industrial facilities in the United States.
The interest in EtO emissions monitoring escalated following the publication of the National Air Toxics Assessment (NATA) conducted in 2014 by the EPA, which was released in 2018. Since then, the US EPA has been working on proposing new emission standards for EtO.
In the past, ethylene oxide source measurements were conducted annually in the US, following the EPA Method 18. This process involved gathering a sample in the field and then sending it to a laboratory for analysis, making it an offline technique.
This method is less than ideal as it often results in long waiting times for results. By utilizing FTIR for this measurement, real-time results become readily accessible.
What are the challenges you need to address when monitoring ethylene oxide at ultra-low levels using FTIR?
One of the primary challenges in transporting this gas at parts-per-billion (ppb) levels is its high reactivity. Therefore, instrument sensitivity plays a crucial role in accurate monitoring at ppb levels.
Like any optical technique, including FTIR, managing interferences is vital. Potential atmospheric interferences, such as high moisture and CO2 must be accounted for, ensuring that the ethylene oxide measurement remains unbiased by these interfering gases.
To meet compliance requirements, it is essential to develop and adhere to robust QA/QC measures when considering all these factors.
Ease of use is another critical aspect of emissions monitoring, particularly when dealing with EtO. For a continuous 24/7 online analyzer, full automation is necessary, allowing seamless integration with the factory's data collection system.
When selecting materials for the sample and calibration lines, careful consideration is crucial. The use of a PTFE line, heat-traced to maintain the gas at the same sample temperature as the stack, has proven successful for the sample line.
You have mentioned sample transport as a challenge. How do you assess and track this?
To assess sample transport, a dynamic spike recovery test is conducted. This involves diluting an EtO calibration standard in stack emissions at a 10:1 ratio, challenging the entire sampling train. It is essential to use EtO directly rather than as a surrogate for this test.
The desired quality metric for this test is an EtO recovery within 70-130% of the expected result, which is often surpassed.
During the spike test, the response time is evaluated to ensure efficient turnover of the gas cell and to obtain results promptly. Typically, the gas is equilibrated after turning the gas cell over five times due to gas mixing, and the response time is measured twice for both rise and fall times.
What is the main value for a customer considering the MAX-OXT Thermal Oxidizer Module?
The MAX-OXT module is highly beneficial in achieving excellent spectral subtraction, providing validation for results, and enhancing the data quality during collection. While it does not directly increase the sensitivity of the FTIR analyzer, it significantly strengthens the analysis, making it more robust and reliable for trace applications.
Our demonstrations have showcased the robustness of trace measurements with the MAX-OXT module, particularly through long-term drift assessments.
Two drift assessments are conducted upon initial installation of the analyzer: a zero drift assessment and a calibration drift assessment. The zero drift assessment involves using zero gas once a day at the same time for seven days.
All the essential data is collected using the EMS-10 system, an automated, four-channel CEM system. This system is optimally configured for detecting EtO at extremely low levels.
About Kelly McPartland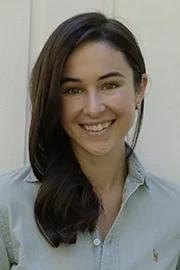
Kelly McPartland serves as the Applications Manager at Thermo Fisher Scientific, Gas Analysis Solutions. A graduate of Boston University, Kelly has expertise in FTIR gas analysis, method development, and data validation. As a senior-level technical liaison for gas analysis customers, she designs and manages data acquisition gas analysis software, ensuring top-notch results and user-friendliness. Kelly also collaborates closely with state and federal regulatory agencies for the development of Quality Assurance Plans and test methods for new technologies.
Her in-depth knowledge of FTIR gas analysis, spanning hardware systems to method development and data validation, originates from her valuable work with customers and regulatory agencies.
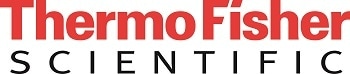
This information has been sourced, reviewed and adapted from materials provided by Thermo Fisher Scientific – Process Analytical Systems for Environmental Monitoring.
For more information on this source, please visit Thermo Fisher Scientific – Process Analytical Systems for Environmental Monitoring.
Disclaimer: The views expressed here are those of the interviewee and do not necessarily represent the views of AZoM.com Limited (T/A) AZoNetwork, the owner and operator of this website. This disclaimer forms part of the Terms and Conditions of use of this website.