In this interview, AZoCleantech talks to Olivia Madamba about Ethylene Oxide (EtO) opportunities and the new regulations proposed by the EPA.
What impact do you think the newly proposed EPA regulations will have on ethylene oxide emissions monitoring for businesses?
The newly proposed regulations will impact all stakeholders – including chemical manufacturers, commercial/medical sterilizers, and continuous emissions monitoring system (CEMS) suppliers – in various ways and will require them to adapt their business and operations goals as the rulings take effect over the next few years.
For EtO manufacturers, sterilizers, and other sources under the scope of the new regulations, the primary consequence of the final rulings will be the need to devote more capital to compliance. Businesses will need to invest in new CEMS technologies to meet the complex monitoring and reporting requirements. These same businesses may also need to invest in updating or optimizing their current equipment and control processes to reduce EtO emissions, which in turn could increase the day-to-day operational costs.
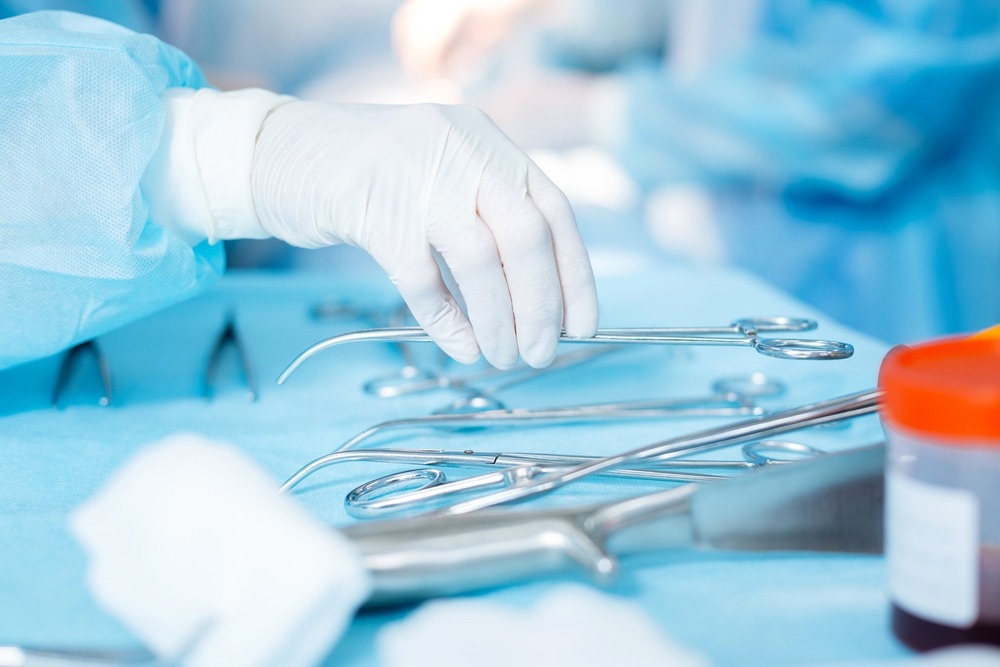
Image credit: Dmytro Zinkevych/Shutterstock.com
Industries that produce EtO emissions may be faced with more administrative burdens related to documentation and reporting. They should also anticipate potential legal fees or penalties associated with non-compliance.
The newly proposed regulations will spur the need for more competitive CEMS technologies. The increased market demand may drive CEMS suppliers to spend more time and money on technological innovation and R&D for more sensitive and robust monitoring equipment and software.
CEMS suppliers and environmental consulting agencies should expect to see an increase in business as the ruling and compliance deadlines approach. Some early adopters of the rulings may want to get ahead of the game and purchase new CEMS sooner rather than later. This allows CEMS suppliers to start building strong relationships in their target markets and learn more about the specific needs of their customers so that they can provide the best experience possible.
Could you explain the main requirements outlined in the performance specification for continuous EtO monitoring? How will this help ensure workplace safety and environmental compliance?
The requirements in the performance specification (PS-19) are used to evaluate if a CEMS is acceptable for monitoring EtO emissions. A company that is able to demonstrate that its CEMS meets these requirements may use it to continuously monitor gaseous EtO under any regulation or permit that requires compliance with PS-19.
Six tests are used to demonstrate CEMS performance: Interference, Level of Detection, Response Time, Measurement Error, Calibration Drift, and Relative Accuracy. These tests should be performed at the time of installation or soon after. The goals of each test are listed below:
Source: Thermo Fisher Scientific – Environmental and Process Monitoring Instruments
Section in PS-19 |
Test |
Answers the Question |
11.1 |
Interference |
How do other gases in the atmosphere or the emissions sample affect the EtO measurement? |
11.2 |
Level of Detection (LOD) |
What is the lowest concentration that the CEMS can detect? |
11.3 |
Response Time |
How long does the CEMS take, under normal operating conditions, to detect a change in the EtO concentration? |
11.4 |
Measurement Error |
How accurate is the EtO measurement at different concentration levels? |
11.5 |
Calibration Drift |
Does the CEMS measurement response drift over time? If yes, by how much does it drift? |
11.6 |
Relative Accuracy |
How does the CEMS measurements compare to US EPA Method 320, when conducted by a certified source testing firm? |
The main goal of PS-19 is to promote safety for those who could be exposed to ethylene oxide emissions. These tests ensure that a CEMS can accurately and consistently measure low levels of EtO to keep communities downwind from sources safe.
How often will operators be required to conduct performance evaluations for their EtO CEMS, and what criteria must they meet during the initial acceptance testing?
Testing is required at the time of installation (or soon after) and whenever specified in the regulations. Under section 114 of the Clean Air Act, the Administrator may require performance evaluations at times other than the initial validation.
The main criteria of the PS-19 tests are described in the graphic below:
Source: Thermo Fisher Scientific – Environmental and Process Monitoring Instruments

What is the validity period of the performance specification test results, and in what cases would the system require retesting?
The performance specification test results are intended to be valid for the system's lifetime. Retesting may be required if major changes are made to its configuration.
Could you provide examples of configuration changes that would require reevaluation according to the performance specification?
Some examples of configuration changes include:
- Major changes to dilution ratio (for dilution-based systems)
- Changes to sample conditioning and transport, if used, such as filtering device design or materials
- Changes to probe design or configuration
- Changes to materials of construction
- Changes to the quantification algorithm provided by the CEMS Manufacturer
Changes consistent with instrument manufacturer upgrades that fall under the manufacturer’s certification do not require additional field verification.
What is the relative accuracy (RA) in EtO monitoring, and how is it established against a reference method (RM)?
Relative Accuracy (RA) is a term commonly used in the context of environmental monitoring, including monitoring of ethylene oxide (EtO) emissions. RA refers to the comparison between the measurements obtained from a method being evaluated (the candidate method) and those obtained from a reference method (RM).
The purpose of this comparison is to assess how closely the candidate method's measurements align with the measurements obtained from the reference method. The relative accuracy indicates how well the candidate method's measurements agree with the reference method's measurements. If the candidate method's measurements are within an acceptable range of the reference method's measurements, it would be considered to have demonstrated relative accuracy.
For the purposes of PS-19, the reference method may be Method 18, Method 320, Method 310, or another alternative approved as an RM by the Administrator. It may differ on a case-by-case basis.
How does the performance specification differ from ongoing CEMS performance evaluations?
PS-19 is not intended to assess the performance of a CEMS over time. The requirements in Procedure 7 to Appendix F of this part are designed to provide a way to assess CEMS and CEMS components (if applicable) performance over an extended period. The source owner or operator is responsible for calibrating, maintaining, and operating the CEMS properly.
Procedure 7 consists of two distinct and equally important functions:
- Assess the quality of the CEMS data by estimating accuracy
- Control and improve the quality of the CEMS data by implementing QC policies and corrective actions
These two functions form an iterative control loop. When the assessment function indicates that the data quality is inadequate, the control effort must be increased until the data quality is acceptable.
What role does the continuous emissions monitoring system (CEMS) play in monitoring gaseous EtO concentrations?
The CEMS is absolutely critical for monitoring EtO emissions from sources. It is the only component that informs the emissions producer, the governing agency, and the public exactly how much EtO is being emitted into the atmosphere and into the air they are exposed to daily. Without the CEMS, there is no way for a source to know if they are in compliance with the EPA regulations, whose primary intention is reducing public exposure.
What role do the Thermo Scientific™ systems play in confirming the effectiveness of pollution controls to comply with the proposed regulations?
The Thermo Scientific MAX-iAQ™ Ambient Air Monitoring system and EMS-10™ CEMS system, offered by Thermo Fisher Scientific™, provide powerful tools that sources can harness to confirm the effectiveness of their pollution controls.
Our multi-channel systems can be used for comparing the inlet/outlet concentrations of abatement processes to determine how efficiently the EtO is being scrubbed from emissions and identify where process improvements can be made. These systems include many factory integration capabilities for process monitoring, control, and data publishing.
Thermo Scientific FTIR-based analyzers work exceedingly well at monitoring a dynamic gas matrix; the robust sampling equipment and powerful analysis technology can make accurate measurements in varying levels of moisture and other gases present in the emissions. The systems can perform both high- and low-level measurements within the same analysis program, meaning that %-levels and ppb-levels of EtO can be consecutively measured.
Can you share how the MAX-iAQ and EMS-10 systems address the challenges of detecting low-level ethylene oxide emissions in real time?
Thermo Scientific’s air monitoring systems are equipped with optically enhanced FTIR (OE-FTIR) technology. OE-FTIR utilizes a highly sensitive detector with specialized optics and analysis algorithms to achieve detection limits down to the single-digit ppb range for demanding applications such as ethylene oxide monitoring.
Paired with our spectral interference reduction technology, the MAX-iAQ and EMS-10 instruments provide not only accurate and unbiased results but also timely results. Time is money, so real-time results are essential for sources to respond to changes in emission levels as soon as possible.
Besides compliance with EPA standards, what additional advantages do MAX-iAQ and EMS-10 systems offer in maintaining indoor air quality and protecting workers' health?
The EMS-10 and MAX-iAQ instruments are both fully automated emissions monitoring systems. They include all of the components required for measuring EtO, including pumps, gas diluters, and sample conditioners.
The goal of these systems is to make the jobs of operators easier and alleviate the burden of monitoring emissions 24/7/365. Both systems do not require calibration; the calibrations are performed at the CEMS supplier and are valid for the system's lifetime. All ongoing quality checks can be programmed into the system’s normal routine for a hands-free experience.
The MAX-iAQ and EMS-10 both have flexible alarm capabilities, and the sampling methods can be customized to fit the needs of the end-user. The built-in reporting engine adds another layer of ongoing support and minimizes the need for multiple avenues of data publishing.
Can you share your insights on how the use of MAX-iAQ and EMS-10 systems may shape the future of industries involved in medical equipment sterilization and chemical manufacturing?
Thermo Fisher hopes to instill confidence in those impacted by the new regulations as they have the ability to meet all of the requirements. We are here to provide the best support we can to these customers, helping them with their monitoring needs.
As the MAX-iAQ and EMS-10 solutions solve many of the complex challenges associated with low-level EtO monitoring, they may cause experts and end-users in these industries to have higher expectations of the capabilities of their CEMS instrumentation.
About Olivia Madamba
Olivia Madamba is an Applications Engineer with Thermo Fisher Scientific, Environmental and Process Monitoring. She has a BS in Chemical Engineering from Worcester Polytechnic Institute, with a concentration in Environmental Engineering. Olivia is an expert in OE-FTIR gas analysis solutions and specializes in both continuous emissions monitoring and ambient air quality monitoring applications.
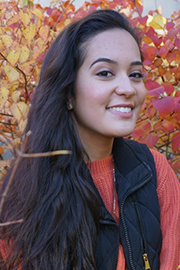
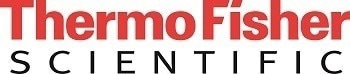
This information has been sourced, reviewed and adapted from materials provided by Thermo Fisher Scientific – Environmental and Process Monitoring Instruments.
For more information on this source, please visit Thermo Fisher Scientific – Environmental and Process Monitoring Instruments.
Disclaimer: The views expressed here are those of the interviewee and do not necessarily represent the views of AZoM.com Limited (T/A) AZoNetwork, the owner and operator of this website. This disclaimer forms part of the Terms and Conditions of use of this website.