Ethylene Oxide (EtO, EO), a sterilant gas and central ingredient in chemical feedstock, is facing a significant regulatory oversight revision to make sure industrial facilities reduce fugitive emissions and limit worker exposure.
Abatement technologies are key to making sure the effort is successful when it comes to achieving regulatory destruction efficiency requirements and producing the monitoring technologies that can demonstrate this at the stack.
This article outlines a series of tests run by Picarro Inc., a leading manufacturer of continuous emissions monitoring systems (CEMS) and provider of complete monitoring services.
The system employed for the purpose of this study was powered by Cavity Ring-Down Spectroscopy (CRDS) on a LESNI EO Catalytic Abatement Plant, which is largely considered to be the chief abatement solution for EtO.
Testing took place at a medical device manufacturing and sterilizing facility in the United States during the active sterilization process. EtO concentrations were quantified in real-time upstream of the Catalytic Oxidizer (CatOx) and downstream at the stack to assess the CatOx’s destruction efficiency.
Picarro’s CRDS monitoring systems demonstrated the capacity to measure single- and double-digit ppb values of EtO at the stack and triple-digit ppm on the inlet, with exceptional repeatability, which quickly provided sensitive data to demonstrate the remarkable destruction efficiency of the LESNI CatOx.
Concentrations at the stack remained under 100 ppb across an hourly-averaged basis, with a 24-hour average of just 12 ppb at the LESNI Ethylene Oxide Catalytic Abatement Plant (EO CAP).
It is clear that this facility has an outstanding average destruction efficiency of 99.991%,1 far greater than the 99.94% other large facilities must comply with as stated in the latest US EPA National Emission Standards for Hazardous Air Pollutants (NESHAP).6
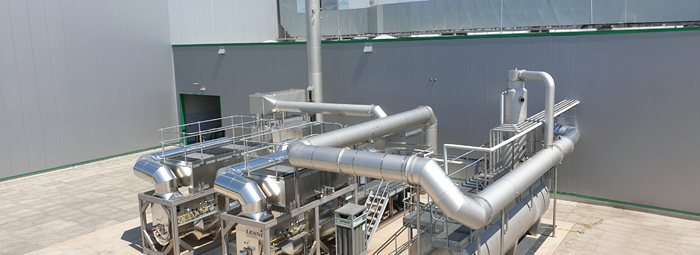
Figure 1. LESNI EO CAP, which Picarro technology shows abates EtO emissions well below the new NESHAP requirements proposed by the US EPA. Image Credit: Picarro
Introduction
Ethylene Oxide (EtO, EO) is a sterilant gas and a key chemical precursor/intermediate broadly used across a number of industries, including refining,2 food processing,3 and medical device sterilization.4
EtO is an important sterilization method for medical devices as the gas demonstrates the capacity to rapidly penetrate a variety of materials, killing microbes in a non-destructive manner.
EtO is used to sterilize devices such as pacemakers and spinal cord stimulators, which cannot be exposed to sterilization by irradiation, steam, or other alternatives.
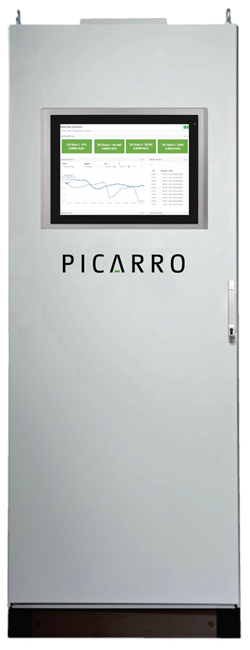
Image Credit: Picarro
In fact, because it is so effective, EtO has been employed extensively across the US to sterilize more than 50% (over 20 billion)5 of all medical devices sold in the US in a 12-month period. These numbers secure its position as the technological backbone behind the safe sterilization of life-saving medical equipment.
Recently, industry workers, community groups, and regulators have raised several concerns about EtO’s carcinogenicity, which has led to a more careful reconsideration of how to use the gas.
This scrutiny helped bring about new regulatory measures designed to minimize EtO emissions and any associated occupational exposure. These measures have come primarily from the United States Environmental Protection Agency (US EPA) and will be legislated and enforced between 2024 and 2026.
This legislation is anticipated to include the following points:
a) Revised EtO NESHAP (40 CFR Pt 63 Subpart O).6
b) Performance Specification 19 (PS-19) for source emissions monitoring.7
c) The Federal Insecticide, Fungicide, and Rodenticide Act (FIFRA) Proposed Interim Decision for workplace and lifetime exposure.8
These regulations also cover stringent measures that local, statewide, regional, and other international authorities9 have produced, although most of these bodies adhere to the US EPA guidelines.
These rules and measures call for a reevaluation of emissions containment and abatement strategies in both the US and International contexts. Companies that employ EtO gas in their processes are advised to apply emissions management systems that have been developed in line with the relevant regulatory compliance.
Anticipated upgrades to these systems, combined with intelligent monitoring, are core elements that allow industrial sectors to meet EPA and other international requirements before the 2024-2026 deadlines.
LESNI paves the way when it comes to planning and integrating emission abatement systems across industries with the most demanding standards by supplying an extensive range of solutions, which include catalytic, recuperative, and regenerative thermal oxidizers as well as chemical scrubbers and solvent recovery systems.
They are committed to delivering solutions that comply with the stringent industrial requirements as set out in the regulatory environments. Furthermore, they are renowned for effectively limiting EtO emissions from sterilization processes, going well beyond the historical 99 % destruction efficiency (DE) level.
While LESNI systems have long been known to abate EtO past the 99.9 % mark, few monitoring technologies have had the sensitivity to prove this, with the likely impact that facilities’ true emissions—often estimated using a DE emission factor—are being significantly overstated.
Legacy analytical techniques are lacking when it comes to proving the necessary destruction efficiencies that the latest regulations demand. This puts abatement system manufacturers in a complicated situation.
State-of-the-art EtO systems offered by Picarro Inc.,10 an industry leader in analytical instrumentation and solutions, have tackled the issues the industry has faced by using PS-19-compliant continuous emissions monitoring systems (CEMS). These systems have the ability to measure down to as little as 0.25 ppb, facilitating abatement performance validation and compliance.
This article highlights how Picarro CEMS demonstrates exceptional destruction efficiencies in a LESNI EO Catalytic Abatement Plant, while providing the subject facility with verifiable EtO abatement of the highest level.
Methods and Materials
LESNI EO Catalytic Abatement Plant
The LESNI EO Catalytic Abatement Plant (CAP) used in this study was located at a manufacturing facility that manufactures and sterilizes medical devices in the US. This facility will soon have to implement the revised NESHAP6 and the recently-published PS-19 CEM standard,7 as well as local emissions standards that can be more restrictive than those at the federal level.
Operations in this facility run on a 24-hour schedule which is split into three working shifts. During each shift, one 12-pallet sterilization chamber and two LESNI accelerated degassing cells, which are paired together, along with additional sources of fugitive emissions, are connected to the abatement system, as displayed in Figure 2.
The facility operates LESNI’s EO CAP, which is positioned directly in front of the stack and couples a balancer and a catalytic oxidizer.
The balancer is a unique preconditioning step that absorbs elevated levels of EtO from the sterilizer vessels into water and, then, over a prolonged timeframe, desorbs this gas slowly to leverage push gas from aeration cells where EtO concentrations are known to run much lower.
The intelligent functionality of the system allows operators to run their sterilization cycles freely without downtime. The LESNI EO CAP also does not necessitate chemicals and produces no waste product.
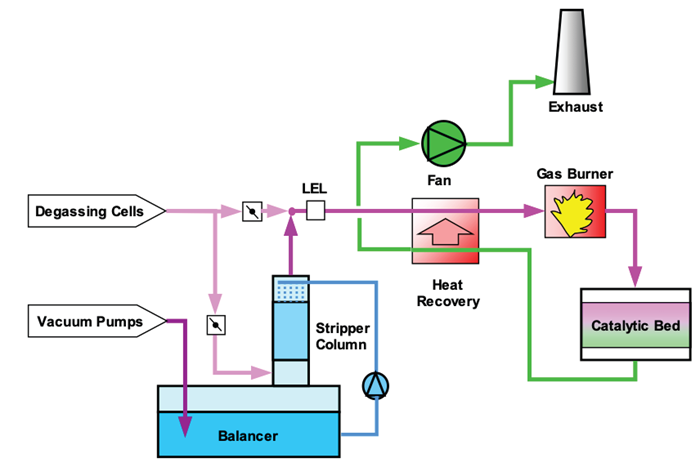
Figure 2. LESNI EO CAP. The Balancer uses water and aeration cell air to modulate EtO concentrations at the CatOx, ensuring safe and efficient destruction efficiency. The CatOx recaptures the heat produced by EtO destruction to minimize the gas needed to maintain the CatOx bed temperature. Image Credit: Picarro
The catalytic oxidizer itself is designed with efficiency in mind, using the intrinsic exothermic reaction of the stripped EtO at the catalyst with heat recovery technology to lower the cost of maintaining the CatOx bed temperature at its set point (see Figure 2).
This well-proven two-step system helps to ensure that all process gas and fugitive emissions are effectively captured and routed to the CatOx at safe, low levels, ensuring that the CatOx itself sees concentrations of EtO well below the LEL (lower explosive limit).11
Picarro CEMS: A CRDS Monitoring Solution
As only a small handful of monitoring systems have the low detection limits required to establish 99.9+ % destruction efficiency for concentrations of EtO below 1000 ppm, LESNI decided to partner with Picarro Inc.10
As an industry leader, Picarro Inc.’s CRDS systems are used around the world, and the company is famed for manufacturing analytical instrumentation with the capabilities to measure hazardous air pollutants and greenhouse gases across an extensive range of industrial applications.
Picarro’s EtO CEMS has guaranteed lower detection limits of 0.25 ppb and has some of the best stability and selectivity obtainable across the industry for EtO.
As well as providing instant responsiveness and one-second measurement intervals, it also records extremely accurate concentrations of CH4, CO2, and H2O, which facilitates the validation of destruction efficiencies using passive and stoichiometric-ratio tracer methodologies.
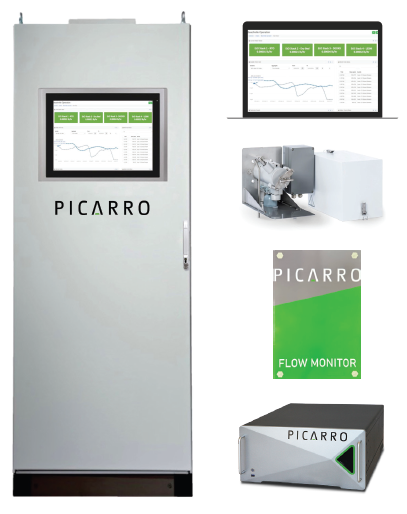
Figure 3. The Picarro EtO CEMS. State-of-the-art Picarro CRDS technology sits within a NEMA-12 (or better) industrial enclosure, with an umbilical connecting the system to the stack, where industry-leading flow monitoring and sample probes feed back essential parameters, and sample and calibration gases to enable real-time monitoring of both concentrations and mass emissions. Image Credit: Picarro
Results
The data outlined below is indicative of a Picarro system measuring the CatOx inlet and stack effluent at the subject facility. As demonstrated in Figure 4, inlet EtO concentrations are in parts per million (ppm) during three sterilization cycles, which lasted for a total of 33 hours.
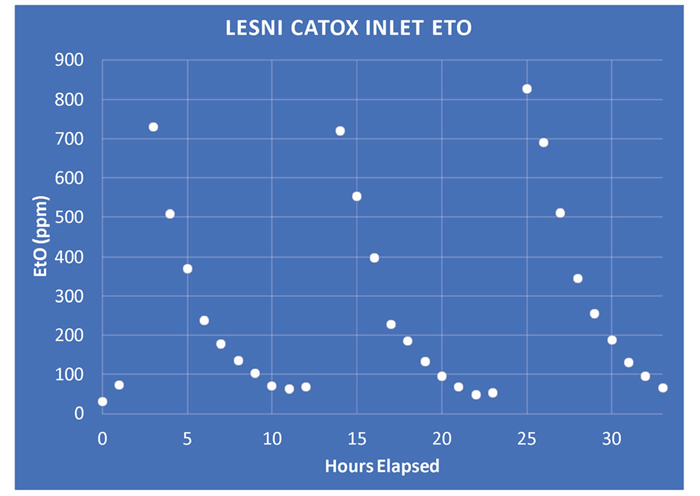
Figure 4. CatOx Inlet EtO (ppm) showing repeatable balancermodulated EtO well below lower explosive levels. Image Credit: Picarro
The balancer impedes the introduction of what would typically be elevated EtO peaks (double-digit %) permeating the sterilizer chambers and passing into the CatOx, which keeps levels under the EtO LEL.
The second data set generated by the Picarro system has been sorted into one-hour averages to allow for easy viewing capabilities. This enables simple quantification of destruction efficiency and exhibits stack concentrations at the required temporal resolution in line with PS-19.
The data demonstrates, as anticipated, that concentrations are as high as 820 ppm in the CatOx per hour on average out of the balancer, with EtO levels slipping under 100 ppm prior to the initiation of the subsequent sterilization cycle.
The stack data (CatOx outlet) is outlined in Figure 5, this time in parts per billion (ppb), closely mimicking the Inlet values in shape but roughly four orders of magnitude lower due to the abatement achieved by the catalytic oxidizer.
The stack registers values ranging from 3 to 60 ppb, with an average reading of 12 ppb. While NESHAP and PS-19 have yet to finalize the precise number relating to average emissions levels, it is likely to be somewhere around 100 ppb.
The LESNI stack also keeps concentrations well below “above span” levels (likely to be 2-3x the span value as seen on two consecutive hourly averages), but if for any reason it exceeded this value, the Picarro CEMS would automatically trigger an above-span calibration check to maintain compliance with Procedure 7 Section 4.1.5,12 a feature standard CEMS solutions do not offer.
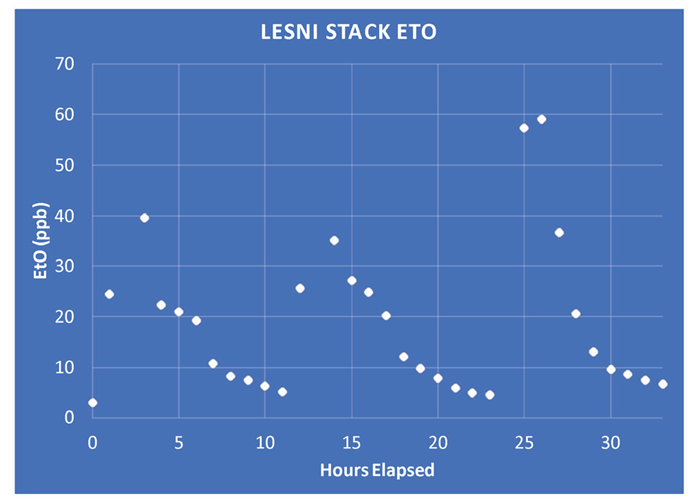
Figure 5. Stack EtO (ppb), showing roughly a four order of magnitude reduction in EtO due to the efficiency of the CatOx. Image Credit: Picarro
Hour-averaged destruction efficiencies can be derived using the inlet and outlet concentrations, as shown in Figure 6.
Beyond 100 ppm, the data demonstrates a rolling average of 99.994 %. Below this threshold but above 2.5 ppm (where the sensitivity of the CEM no longer effectively characterizes 99.99% efficiency), the efficiency stands at 99.989 %. Remarkably, the system achieves a destruction efficiency of 99.991 % for all inlet values exceeding 2.5 ppm.
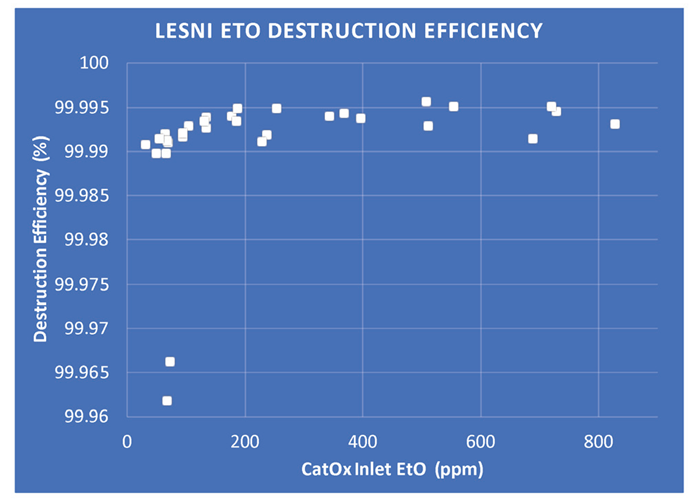
Figure 6. CatOx destruction efficiency as a function of inlet EtO. Image Credit: Picarro
Picarro EtO Technology and PS-19: Demonstrating Excellence in Compliance
It is absolutely vital that instrumented systems used for EtO CEMS monitoring are subjected to initial testing protocols in a laboratory setting. These are performed to ensure the system meets the necessary Interference, Measurement Error, and Level of Detection requirements of PS-19.
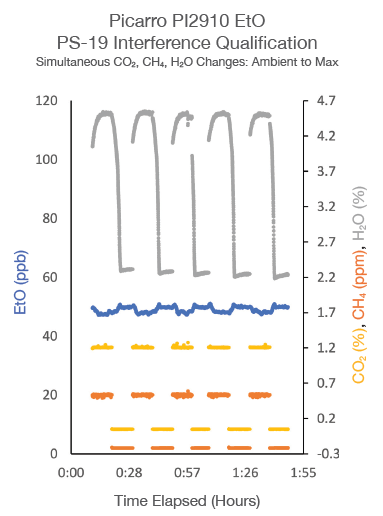
Figure 7. Picarro Interference Response Test, showing very minor changes to EtO when all specified interferent gases are sent to the analyzer simultaneously. Image Credit: Picarro
These tests are run to demonstrate how Picarro’s equipment lives up to expectations when it comes to assessing LESNI Catalytic Abatement Plants. The interference test should be performed with each of the interferent species present but can be conducted either individually or all at the same time; the latter is usually much harder to pass.
The results acquired with the Picarro CEMS instrument are shown in Figure 7. The tests were conducted with all three interferent gases present, alternating between real-world ambient conditions and the highest elevated conditions specified for PS-19 CEMS: CO2 at 1.2% (12,000 ppm), CH4 at 20 ppm, and H2O at 4.5%.
The average difference between the ambient and elevated EtO is shown at 1.44 ppb (<<30 ppb required in PS-19 Section 13.5.1), an astonishing value considering the concurrent introduction of the interferents at maximum concentration.
This statistic is not one that manufacturers of technologies, such as FTIR, commonly provide because of the performance challenges associated with simultaneous cross-talk correction algorithms, thermal oxidation modules, and optical filters.
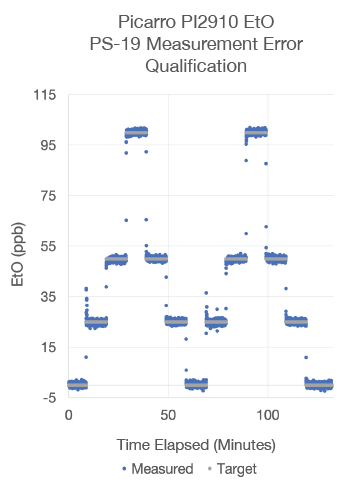
Figure 8. Picarro Measurement Error Test, showing measured (blue) and target (gray) concentrations, showing the power and linearity of cavity ringdown spectroscopy. Image Credit: Picarro
The Picarro CEMS passed the Measurement Error test with an average ME of 0.154 %, 0.154 ppb, <<5 %, or 10 ppb, as outlined in PS-19 Section 13.3 when making comparisons between measured vs. target gas concentration, as shown in Figure 8.

Figure 9. Picarro Level of Detection (LOD) test showing strongly reproducible and differentiable mean/StDev (orange dot with error bar) values for both zero and 10x LOD steps. Image Credit: Picarro
Picarro also ran the “Level of Detection” (a.k.a. “Limit of Detection”) test that is necessary to comply with PS-19 Section 11.2, which requires adjusting the EtO between 0 and 6 ppb (a rough estimated 10x LOD). The test is repeated seven times in an ambient matrix with maximum interferent concentrations, as shown in Figure 9.
The LOD is classified as three times the standard deviation of the mean of the seven zero steps.
While the precise definition of the LOD in PS-19 is somewhat ambiguous given the specified allowed emissions limit, the Picarro system would comfortably meet an LOD of 20 ppb if the limit were stated as 100 ppb (20% of 100 ppb = 20 ppb).
Based on this analysis, the tested limit was ascertained to be 0.239 ppb, exceeding the likely requirement by more than 80 times.
Conclusions
The findings from this evaluation demonstrate that LESNI’s Ethylene Oxide Catalytic Abatement Plant achieved an outstanding 99.991% destruction efficiency under real-world conditions.
Throughout three consecutive back-to-back sterilization cycles, the average Ethylene Oxide (EtO) concentration at the stack remains at just 12 ppb. This measurement is significantly below the likely 100-ppb rolling average limit and also comfortably below the 2-hour averaged “above-span” value limits anticipated in the US EPA Performance Specification 19.7
Therefore, it has been clearly demonstrated that LESNI’s EO CAP systems are able to meet the EPA’s revised NESHAP, which calls for 99.94 % destruction efficiency. Picarro’s Continuous Emission Monitoring Systems offer industry-leading sensitivity, enabling the validation and continuous monitoring of performance.
References
- Values where the Inlet concentration was above 2.5 ppm, the concentration below which a 99.99% efficiency cannot be measured by the CEM’s detection limit of 0.25 ppb.
- EtO use for manufacture of mono-ethylene glycol: https://en.wikipedia.org/wiki/OMEGA_process
- Choline Chloride Production with EtO and TMA: https://patents.google.com/patent/US3373201A/en
- CDC Summary of use of EtO in Medical Device Sterilization: https://www.cdc.gov/infection-control/hcp/disinfection-sterilization/ethylene-oxide-sterilization.html
- Gamma Industry Processing Alliance White Paper: https://gipalliance.net/wp-content/uploads/2013/01/GIPA-WP-GIPA-iia-Sterilization-Modalities-FINAL-Version-2017-October-308772.pdf
- EtO NESHAP 40 CFR Pt. 63 Subpart O: https://www. ecfr.gov/current/title-40/chapter-I/subchapter-C/part-63/ subpart-O
- EPA PS-19: https://www.regulations.gov/document/ EPA-HQ-OAR-2019-0178-0490
- FIFRA PID: https://www.federalregister.gov/documents/2023/04/13/2023-07727/pesticide-registration-review-proposed-interim-decision-and-draft-risk-assessment-addendum-for
- E.g.: South Coast Air Quality Management District Amended Rule 1405: https://www.aqmd.gov/docs/ default-source/rule-book/reg-xiv/rule-1405.pdf
- Picarro Inc. Ethylene Oxide Solutions: https://www. picarro.com/eto
- EtO MSDS: https://www.osha.gov/chemicaldata/575
- Procedure 7: https://www.regulations.gov/document/ EPA-HQ-OAR-2019-0178-0492

This information has been sourced, reviewed and adapted from materials provided by Picarro.
For more information on this source, please visit Picarro.