The elemental examination of lithium battery electrolytes is crucial in guaranteeing the performance and quality of contemporary energy storage systems. Lithium batteries are essential in various technical applications, from mobile devices to electric vehicles.
Electrolytes are essential for lithium battery performance. Their efficacy and longevity depend on the purity and specific composition of the electrolytes used. In lithium batteries, the main function of the electrolyte is to enable ion flow between electrodes.
The in-depth and consistent quality control of electrolyte solutions is vital in ensuring ideal performance. The Chinese industrial standard HG/T 4067-2015 denotes the comprehensive requirements and processes for the chemical analysis of lithium battery electrolytes.1
The standard guarantees that all applicable elements in the electrolytes are correctly identified and quantified, maximizing lithium battery performance and safety. It also offers a homogeneous method that enables compliance with global quality standards and comparability of results.
Lithium hexafluorophosphate (LiPF6) is used in lithium batteries because of its superb conductive properties. The standard referred to above defines a process for assessing the LiPF6 electrolyte and specifies that a mix of methyl ethyl carbonate, ethanol, and water in the ratio 1:4:5 should be used to prepare calibration and sample solutions.
This article elucidates the practical implementation of the Chinese standard, focusing on the analytical procedures for determining various elements in lithium battery electrolytes. Under the standard, three electrolyte samples were assessed for 14 elements, each using the high-resolution ICP-OES PlasmaQuant 9100 Elite (PQ9100).
As LiPF6 results in the formation of hydrofluoric acid, the measurement system was fortified with a hydrofluoric acid-resistant sample introduction kit (HF kit).
The carbon-rich matrix creates spectral overlaps on some analytical lines, an effect that was corrected using the Correction of Spectral Interferences (CSI) software tool. This led to an improved baseline without spectral disturbances and an enhancement of the results’ reliability.
Methods
The reagents and samples used were LiPF6 electrolytes, a multi-element standard solution for ICP (100 mg/L Al, As, Ca, Cd, Cr, Cu, Fe, Mg, Na, Ni, Pb, Zn), single-element standard solutions for Hg and K (1000 mg/L each), ethanol, and ethyl methyl carbonate.
The test samples were diluted by weight by a factor of 10. Under the standard, the diluent was prepared in a ratio of 1:4:5 with methyl ethyl carbonate, ethanol, and deionized water.
Due to the small amount of sample material provided, analysis was performed in manual operation mode (without the auto-sampler) on the PQ9100 fortified with an HF kit. Table 1 summarizes the individual settings and components; Table 2 provides comprehensive information about the method parameters and settings.
External calibration standards were made using single- and multi-element standard solutions with the diluent. Table 3 lists the concentrations of the calibration standards; examples of the resulting calibration functions are shown in Figure 1.
Table 1. Instrument configuration and settings. Source: Analytik Jena US
Parameter |
Specification |
Plasma power |
1450 W |
Plasma gas flow |
15 L/min |
Auxiliary gas flow |
0.5 L/min |
Nebulizer gas flow |
0.35 L/min |
Nebulizer |
parallel path, PFA, 1 mL/min |
Spray chamber |
cyclonic, 50 mL, PTFE |
Outer tube / inner tube |
ceramic/ceramic (alumina) |
Injector |
alumina, 2 mm id |
Pump tubing |
PU (sample: black/black, waste: red/red) |
Pump rate |
0.2 mL/min |
Fast pump |
0.2 mL/min |
Delay time/rinse time |
100 s/100 s |
Torch position |
0 mm |
Table 2. Method parameters. Source: Analytik Jena US
Element |
Line [nm] |
Plasma view |
Integration |
Read time [s] |
Evaluation |
Pixel |
Baseline fit |
Poly. deg. |
Correction |
Al |
308.215 |
axial |
Spectrum |
3 |
3 |
ABC |
auto |
- |
As |
193.698 |
axial |
Spectrum |
3 |
3 |
ABC |
auto |
CSI |
Ca |
317.933 |
axial |
Spectrum |
3 |
3 |
ABC |
auto |
- |
Cd |
228.802 |
axial |
Spectrum |
3 |
3 |
ABC |
auto |
CSI |
Cr |
205.552 |
axial |
Spectrum |
3 |
3 |
ABC |
auto |
CSI |
Cu |
324.754 |
axial |
Spectrum |
3 |
3 |
ABC |
auto |
- |
Fe |
259.940 |
axial |
Spectrum |
3 |
3 |
ABC |
auto |
- |
Hg |
184.886 |
axial |
Spectrum |
3 |
3 |
ABC |
auto |
CSI |
K |
769.897 |
axial |
Spectrum |
3 |
3 |
ABC |
auto |
- |
Mg |
285.312 |
axial |
Spectrum |
3 |
3 |
ABC |
auto |
- |
Na |
589.592 |
axial |
Spectrum |
3 |
3 |
ABC |
auto |
- |
Ni |
231.604 |
axial |
Spectrum |
3 |
3 |
ABC |
auto |
- |
Pb |
220.353 |
axial |
Spectrum |
3 |
3 |
ABC |
auto |
CSI |
Zn |
213.856 |
axial |
Spectrum |
3 |
3 |
ABC |
auto |
- |
ABC: Automatic Baseline Correction, CSI: Correction of Spectral Interferences
Table 3. Concentrations of the calibration standards. Source: Analytik Jena US
Element |
Concentration [mg/L] |
Cal. 0 |
Std. 1 |
Std. 2 |
Std. 3 |
Std. 4 |
Al, As, Cd, Cr, Cu, Hg, K, Mg, Ni, Pb, Zn |
0 |
0.02 |
0.06 |
0.12 |
0.2 |
Ca, Fe, Na |
0 |
0.2 |
0.6 |
1.2 |
2.0 |
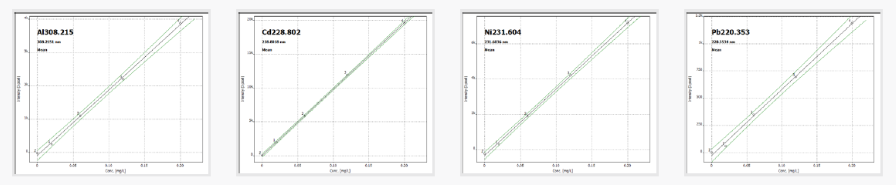
Figure 1. Examples for calibration functions. Image Credit: Analytik Jena US
Results and Discussion
Table 4 shows the results for the three electrolyte samples. After the sample analysis, an independent QC standard of 0.12 mg/L was also prepared and quantified. The recovery is listed in the results table.
Table 5 shows the method-specific detection limits (MDL) of the analysis. These values were determined using the reagent blank method (three times the standard deviation of 11 repeated measurements of the reagent blank). The calculation of the results and the MDL includes the sample preparation dilution factor of 10.
Table 4. Measuring results and QC standard recovery. Source: Analytik Jena US
Element |
Measured values [mg/kg] |
QC std. recovery
[%] |
Electrolyte 1 |
Electrolyte 2 |
Electrolyte 3 |
Al |
<MDL |
< MDL |
0.02 |
103 |
As |
<MDL |
<MDL |
<MDL |
109 |
Ca |
0.61 |
0.711 |
0.60 |
107 |
Cd |
< MDL |
< MDL |
< MDL |
101 |
Cr |
< MDL |
< LOQ |
< LOQ |
101 |
Cu |
< MDL |
< MDL |
< LOQ |
99.0 |
Fe |
0.21 |
0.477 |
0.45 |
103 |
Hg |
< LOQ |
< MDL |
< LOQ |
94.0 |
K |
0.85 |
1.12 |
0.80 |
95.0 |
Mg |
0.04 |
< LOQ |
< LOQ |
104 |
Na |
1.36 |
1.65 |
0.92 |
109 |
Ni |
< LOQ |
< LOQ |
< LOQ |
103 |
Pb |
< LOQ |
< MDL |
< LOQ |
96.0 |
Zn |
< MDL |
< MDL |
< MDL |
104 |
MDL/LOQ: Method specific Detection Limit/Limit Of Quantification (3 or 9 times the standard deviation of 11 reagent blank measurements)
Table 5. Method-specific detection limits (MDL). Source: Analytik Jena US
Element/Line
[nm] |
MDL
[mg/kg] |
Element/Line
[nm] |
MDL
[mg/kg] |
Al308.215 |
0.15 |
Hg184.886 |
0.11 |
As193.698 |
0.13 |
K769.897 |
0.02 |
Ca317.933 |
0.06 |
Mg285.312 |
0.01 |
Cd228.802 |
0.01 |
Na589.592 |
0.01 |
Cr205.552 |
0.07 |
Ni231.604 |
0.03 |
Cu324.754 |
0.02 |
Pb220.353 |
0.11 |
Fe259.940 |
0.01 |
Zn213.856 |
0.01 |
MDL: Method-specific Detection Limit
Summary
The high matrix tolerance, combined with the high resolution and measurement sensitivity of the PQ9100, allows robust and interference-free analysis of lithium battery electrolytes. Software tools, including automatic baseline correction, facilitate spectra evaluation and offer consistent results.
Some lines of analysis show a spectral overlay by matrix-related emission bands. The CSI software tool, which is based on the least squares model, was applied to eradicate this structured background. A spectrum of a pure sample matrix solution (diluent) was logged at the related wavelengths and saved into a database. This correction spectrum was subtracted from the recorded sample spectra.
The created correction model can be employed in the method for automatic application during routine measurements. Figure 3 shows the high spectral resolution of the PQ9100 (2 pm at 200 nm) and the effect of using the CSI tool on the example of mercury (184 nm).
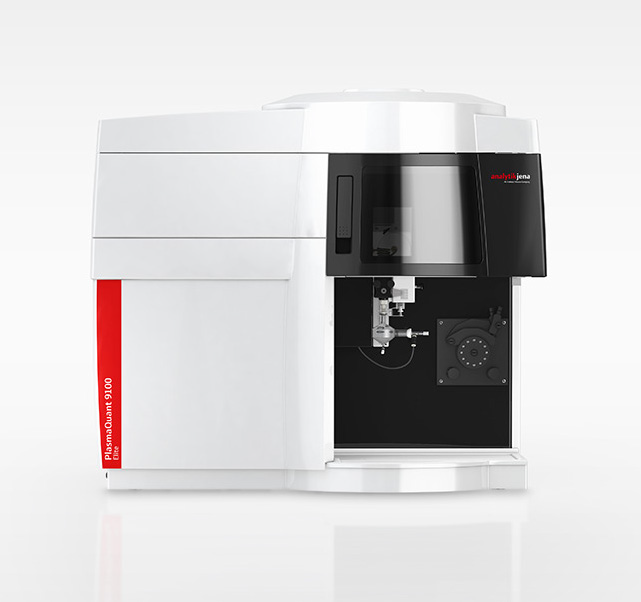
Figure 2. PlasmaQuant 9100 Elite. Image Credit: Analytik Jena US
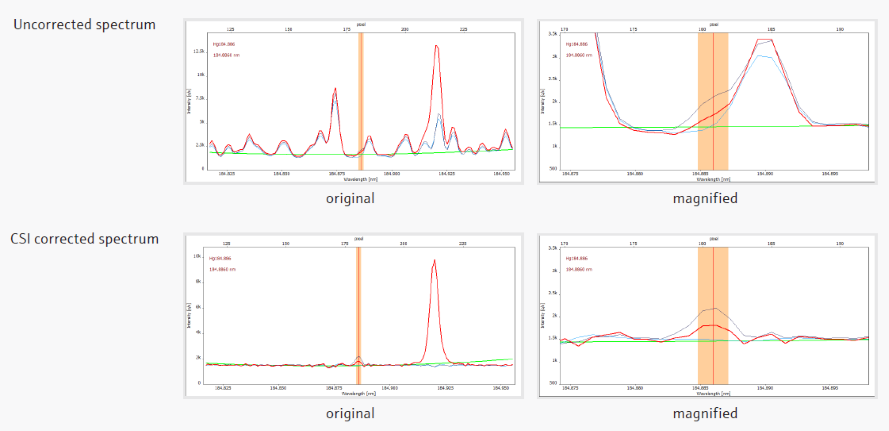
Figure 3. Effect of the CSI software tool on the example of Hg184. Image Credit: Analytik Jena US
Table 6. Overview of recommended devices, accessories, and consumables. Source: Analytik Jena US
Article |
Article number |
Description |
PlasmaQuant
9100 Elite |
818-09101-2 |
High-resolution ICP-OES |
Teledyne Cetac
ASX 560 |
810-88015-0 |
Teledyne-Cetac ASX-560 autosampler for ICP-OES and ICP-MS |
HF-Kit |
810-88007-0 |
HF-resistant sample introduction kit |
Consumable set
HF Kit |
810-88042-0 |
Consumables Set HF Kit for PlasmaQuant 9x00 series |
PU pump tubing (sample) |
418-13-410-528 |
PU pump tubing (black/black) for sample |
PU pump tubing (waste) |
418-13-410-529 |
PU tubing (red/red) for waste |
References
- Chinesestandard.net. (2015). HG/T 4067-2015 English PDF. [online] Available at: https://www.chinesestandard.net/PDF/English.aspx/HGT4067-2015 [Accessed 8 Nov. 2024].

This information has been sourced, reviewed, and adapted from materials provided by Analytik Jena US.
For more information on this source, please visit Analytik Jena US.