According to recent scientific studies, EtO is a more dangerous carcinogen than previously thought. Results from the latest National Air Toxics Assessment (NATA) have made EtO an increased focus of concern for the EPA, state regulators and worldwide regulatory authorities.
This understandably makes sterilization companies concerned about the safety of employees and the community. In a number of instances, the traditional abatement technologies cannot meet the new EtO destruction requirements.
In the United States, the selected air pollution control device must be in compliance with NESHAP (National Emission Standards for Hazardous Air Pollutants) regulations that dictate more than 99% destruction efficiency of EtO (Ethylene Oxide), or concentration levels which are less than one part-per-million by volume.
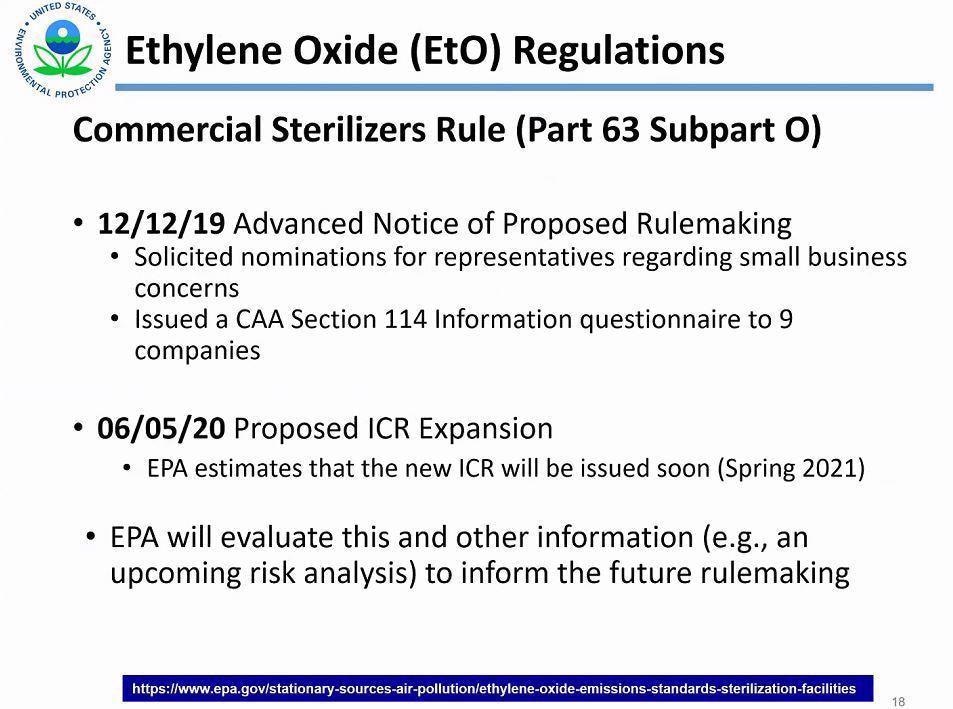
Image Credit: US EPA

Image Credit: US EPA
The Challenge
For many commercial sterilizers, ethylene oxide is the only viable chemical for the sterilization of their products, many of which go into the pharmaceutical industry. The treatment of exhaust gases from aeration rooms, sterilization chambers, and vessels are typically required to use a pollution control device, sometimes referred to as an abator.
Capturing and destroying harmful emissions from sterilization processes can be difficult. In many cases, the scrubber and sorbents technologies traditionally applied on this application cannot meet the increasingly stringent regulations and standards. The volatile organic compounds (VOCs) in the process streams raise safety concerns, both when they are collected in vents and when they reach the final combustion equipment. The concentrations can come in highly concentrated, batch operations making them highly explosive if not diluted.
Application Specifics
- Pollution abatement solutions must be built with alloy construction due to corrosive process streams.
- There is typically a high cost of production requiring the quick installation of pre-assembled, pre-tested environmental systems to minimize process shutdowns.
- There are emerging EPA CFR regulations and increasing wastewater discharge surcharges.
- Guidance and guaranteed solutions are required for tightening and rapidly evolving Ethylene Oxide (EtO) regulations.
- Continuous and batch process operations need custom environmental systems to ensure proper operation and employee safety.
One of the most widely accepted control technologies available to control VOC emissions from the EtO sterilization processes is Catalytic Oxidizers with integrated peak shaver.
Case In Point
A contract sterilizer was using a wet scrubbing system that was no longer a viable means of EtO removal. To complicate the situation further, their high production levels meant they could not afford a factory shutdown which was more than eighteen hours.
This time limitation made the procurement of a pre-assembled, pre-tested pollution control system a necessity.

Image Credit: Anguil Environmental Systems
The Solution
After assessing multiple suppliers and numerous technology alternatives, the sterilization company selected Anguil Environmental Systems to supply a catalytic oxidizer, resulting in minimal downtime and regulatory compliance.
In order to prevent emission spikes from causing an upset condition, a back-vent and peak shaver were also considered upstream of the oxidizer. Yet, a detailed application analysis showed it was not necessary on this particular application.
The Result
The catalytic oxidizer had to control both the high concentration, low air volume exhaust from the sterilization chamber’s vacuum pump, as well as the low concentration, high volume exhaust from the aeration room.
The high concentration from the vacuum pumps of nearly 300,000 parts per million by volume led to a sharp increase in temperature and demanded that the catalyst have a large operational temperature window.
When treating the low concentration exhaust (10 parts per million by volume) from the aeration chamber, the catalyst also had to have a low operational temperature.
In order to satisfy both of these requirements, Anguil and their catalyst supplier carried out extensive research to supply a base metal type catalyst with an operational temperature of 275°F and an operational temperature window of more than 500°F.
The highly concentrated chamber emissions present another set of challenges On some sterilizer installations. Anguil often recommends and installs a peak shaver or wet scrubber upstream of the oxidizer as a safety precaution, as they usually come in spikes when the chamber is evacuated.
Safety is always a priority on Anguil oxidizers. This buffer before the combustion device alleviates any concerns of personal injury or property damage. Designing and building a system that not only met NESHAP regulations for miscellanous organics, but would also operate cost-efficiently was the next challenge Anguil faced for this application.
Catalyst bed bypassing had to be completely avoided due to stringent ethylene oxide regulations. Anguil altered their traditional design to facilitate this and placed the base metal catalyst in horizontal tray configurations. This solution minimized the bypassing concerns associated with air passing around the catalyst media or bed.
A 65% effective 304L stainless steel leak-and-dye tested shell, and tube heat exchanger was utilized in the oxidizer in order to keep operating costs down and prevent leakage, which could lead to a comingling of the clean and dirty air streams.
Anguil could guarantee 0% leakage of VOC-laden air into the clean air stream, unlike other manufacturers who recommended a plate-type heat exchanger. They installed an induced draft fan on the catalytic oxidation system as a fail-safe.
The system was under continuous negative pressure by placing the fan on the discharge side of the oxidizer instead of on the inlet side. This meant that any leakage associated with the oxidation system would be released back into the system instead of out into the work environment.
The whole interior reactor of the oxidizer was made from 304L stainless steel, surrounded by mineral wool insulation and an outer aluminized steel frame. This unique design provides a number of advantages, including increased equipment life compared to the industry-standard aluminized steel reactor interior.
The customer’s time restrictions due to high production levels was another accommodation Anguil needed to consider. Their solution was to completely pre-wire, pre-assemble, and pre-test the system before shipment. The customer’s 18-hour time restriction was met with time to spare.
A Proven EtO Abatement Equipment Design
Combining Anguil’s flagship catalytic oxidizer with a peak shaver, their EtO abatement systems have helped users achieve over 99% destruction efficiency and limited EtO concentrations to under one part-per-million by volume.
Anguil systems ensure zero leakage of EtO from the oxidizer and safe operation by integrating the peak shaver, which is a packed tower counter-flow water scrubber that absorbs ethylene oxide gas into the water by ensuring a high contact area between the water and the gas, preventing unsafe, high concentration conditions.
Anguil is proud of its reputation in the industry and offers solutions that help ensure safer communities and sterilization operations. Sterilizers cannot afford to take the risk on an unproven company. Experienced pollution experts are able to provide a quality engineered solution that exceeds compliance requirements, no matter how complex, without stopping production.
Anguil System Design Features
- Ease of Use: PLC with a human-machine interface and remote connectivity system troubleshooting, alerts operator of equipment shutdowns
- On Schedule: Pre-Assembled, wired, and tested prior to shipment, can be installed within tight time restrictions due to high production levels
- Flexibility: Base metal catalyst offers a large operational temperature window for flow and concentration variations
- Compliance: Horizontal Catalyst Tray Configuration avoids catalyst bed bypassing per NESHAP requirements
- Performance: Leak-and-dye tested shell & tube heat exchanger guarantees 0% leakage of VOC-laden air into a clean airstream, reduces operational costs
- Safety: Induced draft fan functions as a failsafe to prevent leakage into the work environment
- Even safe VOC loadings: Integrated peak shaver evens out fluctuations in contaminant levels to a steady state, preventing unsafe, high concentration conditions
- Durability: 304L SS Construction with outer aluminized steel frame increases equipment life, provides a low-cost maintenance
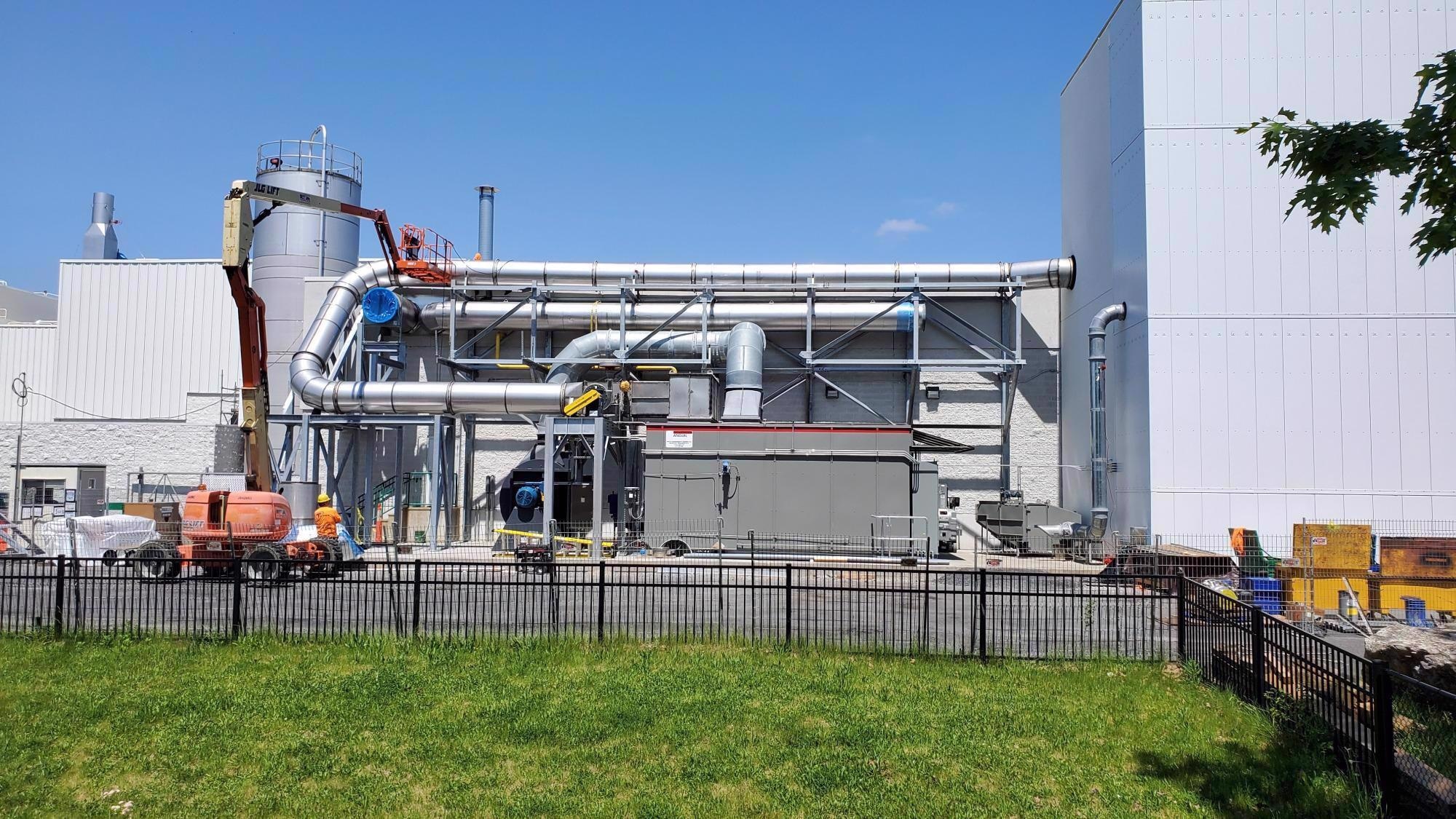
Image Credit: Anguil Environmental Systems
Additional Resources
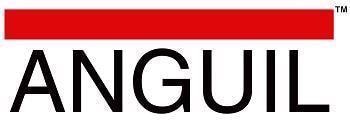
This information has been sourced, reviewed, and adapted from materials provided by Anguil Environmental Systems.
For more information on this source, please visit Anguil Environmental Systems.