The most recent machine technology from AERZEN is the AERZEN turbo blower, which is a compact, low-maintenance, and highly efficient turbo machine. The experience and skill of the company in the turbo sector dates back to 1911, when Aerzener Maschinenfabrik had already begun constructing and distributing the first turbo blowers.
.jpg)
Image Credit: Aerzen
The blower stage concept utilized at that time was based on the principle of a radial compressor, and is essentially indistinguishable from current modern turbo blowers, aside from the significant changes in blower size and drive technology over time. Considering these developments, modern-day speed-regulated units are significantly more compact, more efficient, and almost maintenance-free.
Aerzener Maschinenfabrik has developed the new Generation 5 AT turbo blower series that has been exclusively developed to fulfil the demands of industrial, biological, and communal wastewater treatment plants. The AERZEN turbo blower is operated with high speed, permanent-magnetic motors and can be easily adapted to shifting process air demands of between 40% and 100%, without the need for mechanical adjusters.
Versatility in Numbers
- Overpressures up to 1,000 mbar
- Intake volume flows from 110 m3/hour to 9,000 m3/hour
- Regulation range from 40 to 100%
- Nominal sizes DN 100 to DN 300
Applications
- Wastewater cleaning
- Ventilation of lakes, rivers, and much more
Advantages
- Low maintenance
- High reliability and durability
- Reduced life cycle costs
- Outstanding energy efficiency
Frequency converters and a line reactor are integrated into the systems ready for connection. This high-speed motor is considerably more efficient than standard motors. An entirely oil-free, contact and vibration-free air-foil bearing is used to speed regulate and drive the air-cooled, compact motor. The result is excellent efficiency, reduced wear, and less maintenance effort.
Technology
Compression Principle and Specific Work of a Radial Compressor Stage
The AERZEN turbo blower is a radial compressor. Radial compressors are classed as turbo machines, and here they differ principally from displacement units, for example, positive displacement blowers and screw compressors. Compression is pulsation-free in turbo machines since it is constant.
Usually, ambient air is sucked into the impeller in the axial direction and redirected through the impeller and the housing construction at a 90° angle. Since the air exits in the radial direction, this is reflected in the name “radial compressor”. Rotating at high speed, the impeller charges the suctioned air with kinetic energy through its speed. This is due to the rotation of the impeller.
In this case, the air is continuously moved outwards. The high-speed air escaping from the impeller is slowed down by the downstream diffusor and subsequently collected in the spiral housing surrounding the impeller. When the air is slowed down, the high kinetic energy levels are converted into potential energy, thus creating pressure.
When the accelerated air in the diffuser is slowed down, congestion occurs and the subsequent air molecules collide at high speed with molecules that have slowed down. This compresses the air and generates static pressure in the system. After the air has been collected in the spiral housing, the air in the downstream cone diffusor is again slowed down to make sure that the remainder of the still remaining “kinetic energy” is transformed into potential pressure energy with no major losses.
.jpg)
Pressure is generated by expansion and delay of the fluid in the spiral housing and the diffuser. Image Credit: Aerzen
.jpg)
Pressure and flow velocity throughout the compressor. Image Credit: Aerzen
Bernoulli's Law and the equation P + 0.5 pv2 = P0 mainly explain the operating principle. This explains that when the mass flow through a system is constant, the total energy of a system remains constant. Hence, if there is an increase in the flow speed of the air in the system, there will be a simultaneous decrease in the static pressure of the air flow. In addition, this dynamic applies in reverse—that is, the system’s overall energy does not change. This principle mainly applies to the diffusors of the turbo blower stage.
Energy is only introduced into the system of the radial compressor through the impeller in the form of kinetic energy.
.jpg)
Image Credit: Aerzen
This principle becomes apparent on considering the basic formula of an impeller. Here, the torque acting on the shaft is determined to be equal to the mass flow multiplied by the ratio of the speed of the inlet impeller to the outlet impeller—that is, the air quantity/mass and the isentropic conveyor height measured by the system, or the pressure increase. It is these basic parameters that define the ideal basic geometry of the housing and the impeller.
That is why the impeller has the most important role to play in this process. Its geometry can take several forms and can be decisive for the flow pattern in the entire blower stage. Since the turbo blower is a turbo machine with very high flow speeds within the stage, a turbulent-free flow, and thus one free of losses, becomes a key parameter for achieving high insentropic stage efficiency levels.
The specific work of a radial compressor stage is determined by its enforced conveyed-air mass flow as well as the contribution of the supplied energy, that is, the supplemental effect that accounts for increasing speed.
.jpg)
Torque= m(r2V02-r1V01). Image Credit: Aerzen
.jpg)
Characteristic Diagram of a Turbo Machine. Image Credit: Aerzen
Characteristics of the Turbo Blower
A special characteristic map recognizes each turbo blower. This map shows the operating range within and beyond the operating limits. In majority of cases, various efficiency fields are also included. Illustrating the operating point of the blower within its characteristic map enables it to be instantly apparent whether the blower is operated within its physical limits and at an economically advantageous point. The following four parameters determine the limits of the physical blower:
- The choke limit defined by the maximum throughput
- The maximum possible drive performance
- The pump limit defined by the minimal possible throughput
- The maximum speed
When compared to other blower technologies, the turbo blower reaches a high isentropic efficiency level within this characteristic map, and mainly in the center of the characteristic map.
Efficiency levels differ and are in direct relation with the given conveyed volume flow and the pressure increase. On the basis of operating range of the system, the exact layout of the turbo blower is assumed to be a deciding factor for reliability and profitability. The blower cannot be operated outside the characteristic map as this can damage the machine.
If the turbo blower is properly designed, it can achieve very high levels of efficiency, especially for medium and high volume flows and, based on the pressure increase, a relatively wide control range between the pump limit and the maximum drive performance and/or choke limit.
Inside the AERZEN turbo blower, the components are all exclusively designed for turbo applications and have no application range beyond them. As a result, a turbo blower with the greatest current power density and excellent profitability are realized.
These characteristics can only be reached by using directly-driven radial blower stages without loss-generating drives and regulation devices, and with field-based regulation of the synchronous motor. It is for this reason that each blower unit comes with a frequency converter, control system, drive motor, and the unit components necessary for operation, as standard.
The constant conveying and compression of the process air without pulsation shows that noise levels and the strain on vibration-sensitive components and locations are decreased.
W2P Wire to Process = Total Efficiency Level
Since the number of integrated components is increased, the overall efficiency level is the only major concern for the user. The overall efficiency level includes all partial efficiency levels of the unit, for example, the motor, control system, motor cooling, frequency converter, and other potential partial efficiency levels of built-in components.
It is important that the full scope of the employed air generators is considered, especially in comparison with other technologies that do not incorporate all components required for the preferred operating type. This occurs because subsequent, additional losses can occur if add-on components, such as coolant pumps, frequency converters, gears, fans etc. are used.
.jpg)
Image Credit: Aerzen
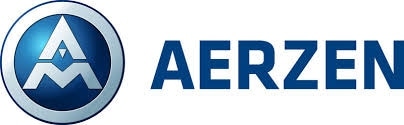
This information has been sourced, reviewed and adapted from materials provided by Aerzener Maschinenfabrik GmbH.
For more information on this source, please visit Aerzener Maschinenfabrik GmbH.