Aerzen uses oil-free air compressors which do not use absorption, to achieve complete purity of the final product in any pneumatic process for the conveyance of sensitive bulk material. Production requirements are high in the food, pharmaceutical, chemical, and petrochemical industries, and these are met by using cutting-edge technology to ATEX certification.
In such fields, compressed air purity is vital to keep all processes at top quality, and this is especially so if the product may come into contact with the compressed air, as when pneumatic conveyance is used. In this case, oil-free compressed air to ISO 8573-1, class 0, must be used. If the product is contaminated with even traces of oil the entire production batch may have to be destroyed.
Oil-free Operation for Purity - Aerzen Guarantees 100% Purity
Any compressed air machine which is lubricated by oil, such as installed bearings or gear wheel lubrication, which may come into contact with the bulk material during pneumatic conveyance at any point or in any form, and must be carefully protected against this possibility, as this may lead to product or bulk material contamination, and also wreck the compressed air installation partly or completely, which is a costly affair to repair.
Aerzen Guarantees Total Purity
Aerzen is a famous manufacturer of compressors of different sorts, including the positive displacement blowers or Delta blowers, rotary lobe compressors or the Delta Hybrid, and screw compressors or Delta Screw models.
These are used to compress air in many industries using pneumatic technology, and Aerzener Maschinenfabrik GmbH is proud to have innovated new standards of safety in these fields. The following standards and guidelines are used to define the Aerzen safety regulations in coordination with TÜV Rheinland LGA Products GmbH:
- ISO 8573-1: 2010 Part 1: Contaminants and purity class
- ISO 8573-2: 2007 Part 2: Test methods for aerosol oil content
- ISO 8573-5: 2001 Part 5: Test methods for oil vapor and organic solvent content
Since the full range of Aerzen machines comply with these certifications, the company is responsible for making it possible for these industries to be confident of obtaining compressed air at high quality, assured of being oil-free, for use in any of the numerous processes and applications for which it is required in these fields.
.jpg)
Bulk material contaminated with oil during the pneumatic conveying process. Image Credit: Aerzen
.jpg)
Deposit of insulating material from silencers with absorption material. Image Credit: Aerzen
.jpg)
Burnt compressor system after sparking in the blower. Image Credit: Aerzen
Aerzen Absorption-free Silencers – 100% Reliability
The new patented line of silencers from Aerzen increases the lifetime and reduces energy usage while complying with noise emission regulations.
Aerzen Technology for Stable, Safe and Efficient Silencers
Compressor stages need to be durable, efficient, and widely available, and this limits silencer technology in actual industrial use. When a discharge silencer is lined with absorption material, it undergoes wear and tear mostly because of the high air temperature at intake, up to 280 °C, and the pulsation within the silencer which causes abrasion of the absorptive material.
This results in fine particles of absorption stuff which are washed out of the silencer to enter the air stream in the conveyor, bringing them into contact with the bulk material. This prevents 100% purity of conveying air as well as posing a potential fire hazard when the absorption material is one used for ATEX applications.
The Aerzen Solution
Aerzen research and development has come up with a patented revolutionary silencer technology (European Patent No. 1857682). These are termed reactive silencers and will be Aerzen’s standard silencing technology for its Delta Blower (positive displacement blower), Delta Hybrid (rotary lobe compressor) and Delta Screw (screw compressor) range to reduce the pipe noise.
Its use has been shown to bring down safety risks and boost efficiency considerably, especially as it reduces pressure losses markedly in contrast to the traditional absorptive-type silencers.
Aerzen also ensures that the sound pressure will remain at the required levels if the component has useful service life, and indeed over the lifetime of the compressed air system. These new Aerzen silencers have eliminated the use of any absorption material, using air deflection to reduce sound levels.
As seen below, the sound pressure (the blue curve) is kept within mandatory limits over the machine’s life cycle as a result of this technology, since there is no chance of stray absorption material which would increase the pipe sound level. The yellow curve, representing the noise level, remains constant, as shown.
Thus Aerzen has brought out a significant contribution to achieving compliance with the VDI directive 2058 and TA Lärm (German Technical Guidelines for noise reduction), not just soon after installation but over its lifetime. The technology also contributes to work safety in accordance with the occupational safety regulations on protecting workers against noise and vibration, by making sure that there is no exposure to a subtle and progressive increase in noise level.
.jpg)
Noise development due to wear of the absorption material in the discharge silencer. Image Credit: Aerzen
100% Safety – ATEX-ready Technology
Aerzen compressors and blowers are the first choice in critical areas of application, and clients can trust in decades of expertise and know-how when it comes to Aerzen equipment, especially in ATEX-certified processes.
100% safety is achievable using Aerzen’s product range for any ATEX zone because of the many options for high-performance blowers and compressors, at cost-effective rates and with complete adherence to the increasingly strict regulations.
All Aerzen Delta range packages including screw compressors have been designed in accordance with categories two and three which deal with dust and gas industrial zones to European Machinery Directive 2014/34/EU. They are also tailored to meet explosion protection to ATEX directive 137 (1999/9/29 EC).
No Absorption Material, No Sparking
One safety aspect largely overlooked in pneumatics is the risk of sparking from the blowers and compressors, which could lead to the sparks blowing into the pressure conveying pipe and igniting the mixture of dust and air. In this case the Aerzen ATEX-certified solution already has TUV certification because of its inbuilt spark arrester in the base or discharge side of the silencer which avoids sparking in hazardous zones in any emergency situation.
Spark arresters need not be independently installed, saving costs and space, as well as reducing energy consumption in a sustainable manner by avoiding downstream pressure losses at the site of the outlying spark arrester.
No Explosion while Conveying Bulk Material Pneumatically
While pneumatic conveyance is in use for bulk goods which are flammable or explosive, it is possible for a mixture to be inadvertently formed which is hazardous. Aerzen supplies all types of ATEX system parts, preventing explosive risk. ATEX guidelines also mandate obligatory explosion protection in the event of any disruption, real or potential, in zone 21.
For this reason, Aerzen has designed its systems to be safe even if unexpected failures occur at any point, beyond prediction. For different systems and configurations, as well as different products, bulk material transport is ensured by overpressure conveyance or pneumatic suction. If the separation filter breaks down or malfunctions during the suction phase, the blower must not suck in dust-air mixtures which are highly flammable.
For this cause Aerzen includes a TUV-certified filter element called the police filter or a zone separation filter in the inlet silencer, which is observed by measuring differential pressure. This again provides a big benefit to Aerzen clients in that they need no additional filters of this sort in the system.
.jpg)
Image Credit: Aerzen
Conclusion
Aerzen has gone to great lengths to design very safe systems for client and process safety. This means their devices may be used whenever there is a critical process which cannot tolerate any form of oil injection technology. Aerzen safety packages are also complete with filter elements, silencers, custom-made oils and tested systems for explosive zone applications.
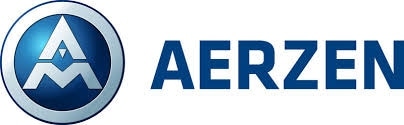
This information has been sourced, reviewed and adapted from materials provided by Aerzener Maschinenfabrik GmbH.
For more information on this source, please visit Aerzener Maschinenfabrik GmbH.