In many fields of industry, the manufacturing processes must be carried out at sub atmospheric pressures, as in the food, pharmaceutical or chemical industries, or process engineering. When the pressure is -700 mbar (300 mbar abs.) it is termed negative pressure, but below this level it is in the vacuum range – rough, fine, high and ultra-high vacuum, as shown in the following chart:
.png)
Image Credit: Aerzen
The absolute pressures are measured in millibar (mbar) in the area of vacuum technology, the term ‘absolute’ simply meaning the perfect vacuum, which has a pressure of 0.0000 mbar absolute. The term ‘absolute pressure’ is used by convention in the vacuum industry to avoid having to add the suffix “abs” each time.
To achieve all levels of vacuum up to high, at a cost-effective rate, pumping sets are utilized to work in two stages, using backing pumps and positive displacement blowers simultaneously. Aerzener Maschinenfabrik GmbH has been a leading manufacturer of positive displacement blowers from its inception in 1868. In 1940, it began producing among the first special positive displacement blowers for the generation of vacuum.
Thus, it continues to lead the field in pioneering and developing innovation in this technology, with both negative pressure and vacuum blowers. Its expertise in this technical area, the extreme accuracy of manufacturing processes, durable design, long experience, and openness to communicate and receive feedback, as well as tailor solutions for the client’s individual needs have led to its success over time.
The Aerzen positive displacement blowers G5 series Delta Blower can create negative pressure up to 500 mbar abs, while the newer rotary lobe compressors series Delta Hybrid takes it up to 300 mbar abs. A single stage is already able to produce these pressures.
Combining Backing Pump and Vacuum Positive Displacement Blower
To enable the generation of negative pressures below 300 mbar abs. a double-stage equipment setup is required in the form of a backing pump with a vacuum positive displacement blower. This leads to the safe creation of the required volume flow or maximum vacuum required, which is called the operating point.
The first stage uses the backing pump to bring the medium, contained in a reservoir or room, to a pre-vacuum stage of about 200 mbar abs. for instance. The next stage uses the vacuum positive displacement blower additionally to bring it down to the final volume flow.
In one scenario, a steelwork in China indicated the need for the following parameters for the vacuum plant to be set up as part of the factory:
- The size of the room or the reservoir which is to be drained
- The operating point
- The maximum pumping time possible
This is discussed with the manufacturer of the pumping equipment who then puts together the most appropriate combination in partnership with Aerzen.
.png)
Diagram of a 4-stage pumping set: stages 1 and 2 with HV blower. Image Credit: Aerzen
Close Coordination
Different types of backing pump systems are considered, including the water ring vacuum pumps, oil-lubricated rotary vane pumps or controllable claw pumps if neutral gases are to be used. The choice depends on the application, and for top-grade applications as in the chemical industry where process gases are to be sucked out, more expensive screw vacuum pumps may be opted for.
Aerzen has specialist experience drawn from decades as a famous manufacturer and supplier in this field. It advises the pumping equipment producer on the optimal choice and the corresponding Aerzen vacuum positive displacement blower that matches the pump set and backing pump profile with regard to energy and heat parameters, and the client’s specifications.
.png)
Image Credit: Aerzen
Picture 1 depicts the outcome of the theoretical calculation as to how the backing pump shown as an orange line will behave with the Aerzen vacuum blower series Gma, shown as a green line, in a double-stage setup. Multistage solutions also work well and bring down the pumping time, such as a single backing pump with a series of consecutive vacuum blowers.
The x-axis shows the pressure ranges within which the backing pump and vacuum blower operate, while the volume flows are plotted on the y-axis. In the current instance, the backing pump begins to work on its own, until the vacuum is at approximately 200 mbar abs. At this point, the Aerzen vacuum blower is started up.
The green curve continues to rise until the operating point is reached at 1 mbar. Now, the volume rate flow is about 1,750 m³/h. This calculation shows two heat-critical pressure ranges, which can be modified by changing the parameters of the design. For instance, this combination of the backing pump and Aerzen vacuum blower allows the operating point to be achieved at 1 mbar, which results in successful operation.
In this way, by using the thermal limits and selecting the most ideal backing pump and vacuum blower from the options, the pumping set manufacturers and Aerzen were successful in meeting the pumping set requirements as stipulated by the client operator. This in turn ensures that pumping is economical and energy-efficient at the same time.
Aerzen has a wide range to choose from as per the vacuum range:
- From 300 to 10 mbar: mHV series vacuum blowers with pre-inlet cooling
- From 200 to 10-3 mbar (0,001 mbar): Vacuum blowers series HV
- From 200 to 10-5 mbar (0,00001 mbar): Vacuum-blowers with canned motor drive (so-called canned motor blowers) series CM and HM.
Vacuum Blowers with Pre-inlet Cooling
Aerzen vacuum blowers of the series mHV which produce vacuum from 300 to 10 mbar are also called pre-inlet blowers. They come in 11 sizes and their theoretical nominal intake volume flows range from 250 to 61,000 m³/h.
They produce a maximum differential pressure which depends on the thermal load. These are suitable for rough vacuum and negative pressures, either as a backing pump or a negative pressure stage against the atmospheric air, so that high differential pressure is created in one stage and high compression ratios can be achieved in the range of rough vacuum, at up to p2/p1 = 5.
They are ideally used when non-stop operation is to be performed without overheating the equipment. Either air from the atmosphere or re-cooled gas is used. This is led into the packaged unit through the discharge side using another intake channel, without requiring a valve or regulator. The cooled gas is re-cooled in a gas/air or gas/water cooler, fixed between the pre-inlet blower and the backing pump.
This blower has flanges on its housing which are fitted with O-ring seals. Splash lubrication drives lube oil to the vacuum blowers with pre-inlet cooling. The blowers move by a motor or a spur gear, the latter being required if the differential pressure is limited, using a slim V-belt. A combination of splash ring and piston ring labyrinth seal is used to seal the conveying chamber. The drive shaft seals are double radial and have an oil barrier.
Vacuum Blowers for the Fine Vacuum Range
When a vacuum range between 200 and 10-3 mbar is required, series HV air-cooled blowers are used, in one of 12 sizes, with theoretical nominal intake volume flows from 180 to 97,000 m³/h to achieve speeds from 3,000 to 3,600 rpm. The type Gma has vertical flow, while series Gla has a horizontal flow direction. This allows a very small size of device.
These two types can be made use of in various coating processes, in chemical or process engineering, in metallurgy, the packing industry, and central vacuum plants. They are also useful in helium compression and systems to detect leakage of helium, manufacturing of lamps and tubes, solar equipment, and automotive equipment.
Special applications can make use of specialized seals such as when air-cooled splash lubricated blowers are to be used, or less commonly used materials are utilized in the construction of cast parts and rotary pistons.
.png)
The air-cooled blower GMa 10.2 HV works with vertical direction of flow. Image Credit: Aerzen
The high energy efficiency is due to the standard type of drive with motors, type IE3, and makes them suitable for the wider market including Canada, Russia, and the USA. They are used to operate frequency converters. The flange connects the motors directly to the blowers. The splash ring-piston ring labyrinth seal is designed to keep oil out of the conveying chambers.
The large neutral chamber has condensate channels and can be purged using seal gas to purge it more effectively. The HV series of vacuum blowers can even be customized to ATEX approval 94/9/EG as another option, which is a unique advantage. These are spike-resistant up to explosion pressures of 13 bar and work without bypass controls.
These are one of a kind in that they alone are approved for zone 0 internally and temperature class T4 externally. The safety of the process can be enhanced by shutting down the monitoring option if the pressure falls below 50 mbar.
Canned Motor Blowers for High Vacuum Range
Aerzen offers a range of series CM canned motor blowers for aggressive gases and HM series for neutral gases. These can be installed permanently for very short pumping durations, as in industrial high-vacuum applications, to produce high vacuum of 200 to 10-5 mbar. They have a hermetic drive attachment with the drive shaft kept sealed off from atmospheric air by an inbuilt canned motor.
At the same size the pumping speed almost doubles from 6000 to 7200 rpm, which is responsible for the drastic reduction in pumping duration to a few seconds, ideal for high-speed production. Even higher speeds are made possible by linking two backing pumps with a single canned motor blower to function as a single pumping set.
This is available in a highly compact format which is important when many pumping sets are used in multi-system applications. Canned motor blowers are available from Aerzen in two types of construction:
- Type CM for corrosive gases, in 14 sizes, for theoretical nominal intake volume flows from 110 to 15,340 m³/h
- Type HM for neutral gases in nine sizes for theoretical nominal intake volume flows from 406 to 15,570 m³/h
Such systems are essential when industrial vacuum is to be generated, as in chemical or process engineering, detection of helium leakage, when hydrogen is evacuated, coatings on foil or glass, or just about anywhere that leakage is not acceptable. Other important applications include semiconductors and microelectronics, as in flat screens, solar, and laser industrial applications.
These blowers can deliver air horizontally or vertically and use standard water cleaning so that they are ideal for clean room applications. The high mechanical resistance of up to 230 mbar makes the pumping time shorter, while a frequency converter is used to increase the control range to 1:5, enabling the blower size to be reduced. A variety of motors is available for network, cyclic and non-stop operations, which makes it possible to find a solution to any client’s requirements.
Conclusion
To design a pumping set for generation of vacuum optimally, ready-made solutions must be dispensed with in favor of a careful matching of backing pump and vacuum positive displacement blower to each other by checking their respective performance parameters. This will help it to achieve the required levels of performance and the specified operating point, while saving energy and time.
Aerzen provides detailed advice as the supplier of intensively designed vacuum blowers, in consultation with the pump set manufacturer, since the backing pump along with the vacuum blower are acquired externally by the latter.
The advanced Aerzen software enables a thorough inspection of the combination with special attention to preventing pressure ranges which are heat-critical and providing the best gradation ratios in terms of efficient energy utilization. This leads to the optimal design of the whole pumping set.
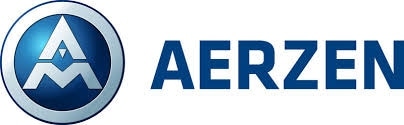
This information has been sourced, reviewed and adapted from materials provided by Aerzener Maschinenfabrik GmbH.
For more information on this source, please visit Aerzener Maschinenfabrik GmbH.