Getting to net-zero carbon emissions will require a massive increase in capacity in renewable energy. Wind power is the most promising renewable energy technology we have but inspecting and maintaining wind turbines is currently prohibitively expensive and often dangerous. An ambitious robotics project in the UK may hold the key to unlock wind’s full energy potential.
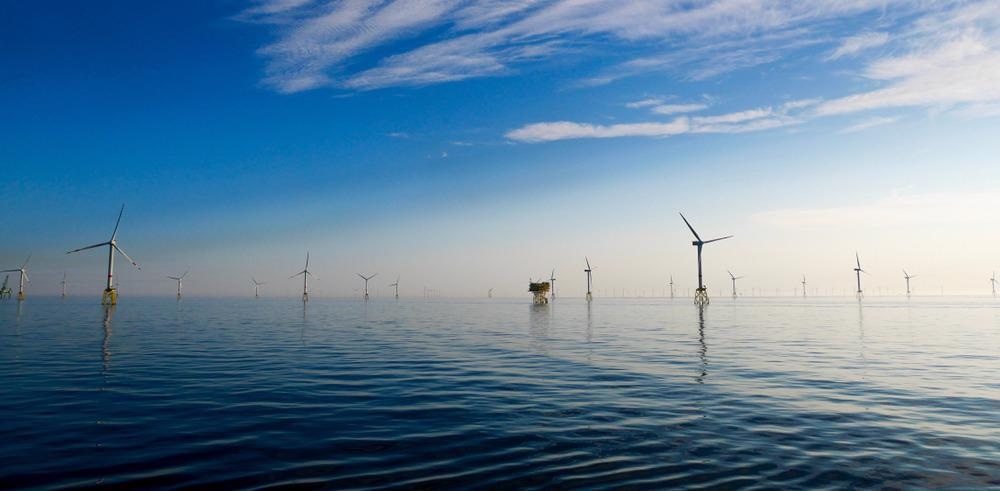
Image Credit:/Kaisn/Shutterstock.com
Is Robot-Based Wind Farm Maintenance Possible?
The £4 million MIMRee project was funded by Innovate UK, a government-backed technology investor. It was tasked with developing a proof of concept for robot-delivered repair and maintenance on offshore wind farms.
The project recently concluded and delivered positive results. According to project partners, human-robot maintenance teams could be deployed to wind farms within 10 years – and wind farms designed for maintenance by robots only will be possible by 2050.
OREC (Offshore Renewable Energy Catapult), another UK government-backed organization, led this project. Ben George, OREC’s Operations and Maintenance Centre of Excellence boss, said:
Today, conditions at sea make human-only missions subject to safety risks, delays, cancellations and extensive turbine downtime. This will not be a feasible way of running the super-sized offshore power stations of tomorrow that lie in deep waters hundreds of miles from shore.”
As well as OREC, the MIMRee team included academics and technologists at the forefront of wind energy development. The project lasted for two years and tested new technologies and systems for robot-based wind farm maintenance and repair.
George commented:
“This project has proven that such a system is possible and can handle the extreme environments at sea. We have tested each of its components in real-world settings, including at our offshore demonstration turbine off the coast of Scotland.”
How Does the Robot-based Maintenance System Work?
For the MIMRee project, an autonomous mothership robot produced by robotics pioneer Thales uses an onboard inspection system to find defects in wind turbines’ blades. The inspection system is capable of scanning turbine blades’ structure while they are still spinning, at speeds of up to 200 mph at the tip.
Once a defect is found, the mothership sends signals to the turbine to stop spinning and launches a specially adapted drone to the problem turbine. This drone carries a six-legged “blade crawler” robot that latches onto the blade and carries out the repair.
UK start-up, BladeBUG, supplied the blade crawler robot to the project. The project developed this robot to be more effective at repairing blades and trained it using an advanced simulation.
George commented:
“We’ve also developed a hardware-in-the-loop simulation system that allows individual robots to connect to a simulated environment so we can fine-tune their team behaviour before they go into the field.”
This use of robotics and autonomous sensing is currently a focus for wind energy technology developers at the forefront of innovation. Dr Paul Gosling, Chief Technical Officer for Thales in the UK, said:
“Increasingly we are seeing the technologies around robotics, autonomy sensing and AI providing solutions enabling activities involving harsh environments to be undertaken using unmanned systems.”
The mothership is supported with data from sensors attached to components in the turbine. There are more than 8,000 individual components in a wind turbine and acquiring performance data from these remotely is key to the success of autonomous maintenance and repair schedules.
Connecting the data from these sensors and from the mothership’s autonomous inspection capability is a powerful AI. This was inspired by engineering solutions to repair and maintenance in space, another severely extreme environment.
Professor Sara Bernardini, previously of NASA’s Mars Exploration Rovers missions, developed the AI system that links robots together and communicates with human operators. She said:
“Space provides a good example of humans working with robots. The current Mars exploration programme uses a team of robots, from helicopters to rovers, that can withstand extreme conditions. Astronauts are deployed selectively, where human ingenuity is most needed and risk to life is lowest.
“Likewise, future offshore work will be about humans being in the control room, developing and managing robotics and learning the skills required to work in teams with them.”
What Have We Learned from this Project?
George concluded:
This is not just a way for the sector to reduce costs, it is essential if the offshore wind industry is to achieve the scale of expansion needed for Net Zero.”
OREC believes that a human-robot maintenance team for offshore wind farms will be possible within 10 years. Such a system would work under human supervision and only send human workers to intervene where they are absolutely necessary.
By 2050, OREC predicts that robot maintenance and repair systems could be fully autonomous, capable of planning their own missions and conducting them without human control.
OREC calculated that this would reduce the cost of energy by 10%, including a 27% reduction in operating expenses.
References and Further Reading
Offshore Wind Innovation Hub (2021) Quantifying the Impact of Robotics in Offshore Wind. Offshore Wind Innovation Hub. [Online] https://offshorewindinnovationhub.com/industry_insight/quantifying-the-impact-of-robotics-in-offshore-wind/.
OREC (2021) Meet the Robot A-Team that will be vital to the future of offshore wind and Net Zero. OREC. [Online] https://ore.catapult.org.uk/press-releases/meet-robot-a-team-vital-future-offshore-wind-net/.
Pilkington, Ben (2021) The Benefits of Installing Sensors on Wind Turbines. AZoSensors. [Online] https://www.azosensors.com/article.aspx?ArticleID=2253.
Disclaimer: The views expressed here are those of the author expressed in their private capacity and do not necessarily represent the views of AZoM.com Limited T/A AZoNetwork the owner and operator of this website. This disclaimer forms part of the Terms and conditions of use of this website.