Martina Petranikova, from Chalmers University of Technology in Sweden, speaks to AZoCleantech about her team's optimized battery recycling process which is a vital step towards accelerating the electromobility society of the future.
Can you tell us briefly about your role at Chalmers University of Technology and how you began researching electric vehicle battery recycling?
I am an associate professor at Chalmers University of Technology. I began work on EV batteries in 2013 when I became a postdoc at the same university. The project was related to NiMH batteries. In 2014 however, we started to work on Li-ion batteries together with Swedish car producers and recyclers.
Why is it important that we find ways to recycle EV batteries?
There are three main reasons for recycling electric vehicle batteries:
- To minimize the impact of e-mobility and electrification on the environment
- To fulfill the directive
- To secure resources for battery production
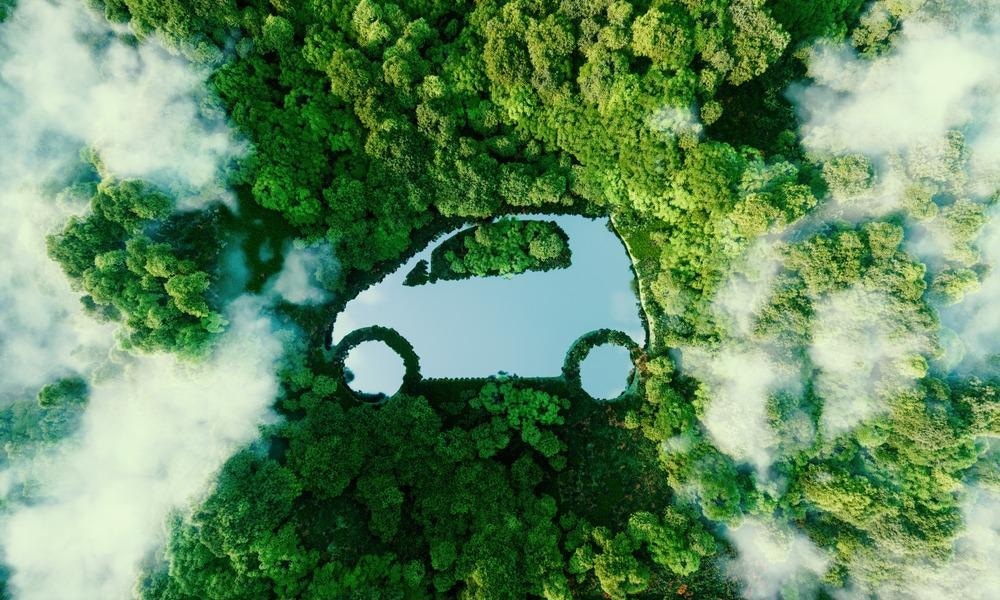
Image Credit: petrmalinak/Shutterstock.com
Recycling is mandatory based on the EU directive. We cannot incinerate or landfill any of the batteries. Battery production is also increasing in the EU (and world) and significant volumes of the raw material are needed. However, the EU depends on the import of those resources from other countries. The majority of cobalt comes from Africa, while most of the lithium comes from South America and Australia, and graphite comes from China.
We have to keep in mind that mining raw materials has a direct impact on the environment, therefore, we should maximize the utilization of secondary raw materials (spent batteries) and re-use metals, so less mining is needed.
What are the current limitations of recycling EV batteries?
Currently, the available volumes of waste are the main limiting factor, but this is going to change in upcoming years. Some technologies are not capable of fulfilling the requirements of the directive to recover lithium. Other components, including electrolyte, graphite, and polymers, are destroyed and not recycled, and some of the technologies are not optimized for energy and chemicals consumption.
Can you outline your study, including the methods taken and key findings?
We have compared two thermal pre-treatment methods: incineration and pyrolysis. We determined that pyrolysis was a better choice for further chemical processing as it made chemical treatment faster and led to metal recovery without the use of additional chemicals. We also determined that a shorter time of pyrolysis was sufficient to achieve high metal recovery, decreasing the energy demand and improving processing time. Moreover, our chemical processing was performed at room temperature, so no additional heat was required.
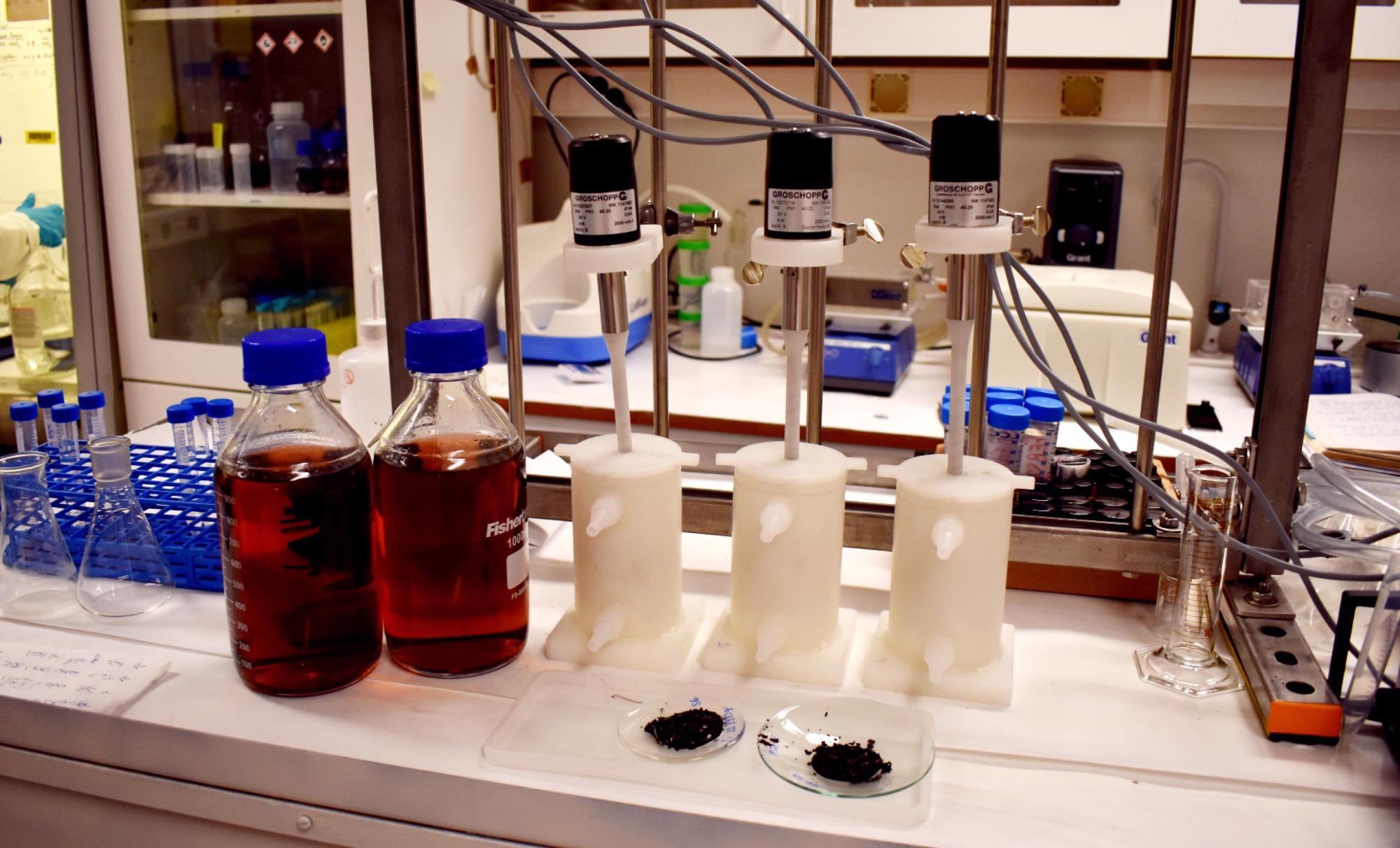
Laboratory equipment for the filtration process with the final liquid-based solution of recycled metals and solid residues containing graphite. Image Credit: Chalmers University of Technology
How does your optimized recycling process represent a vital step towards electrifying our society?
Any improvement of the recycling process will boost the raw material supply and decrease the entire impact of recycling on the environment. Our research can help to process larger capacities of the waste in a shorter time once the batteries start to come back from the market. It will also decrease the consumption of the chemical needed for the processing.
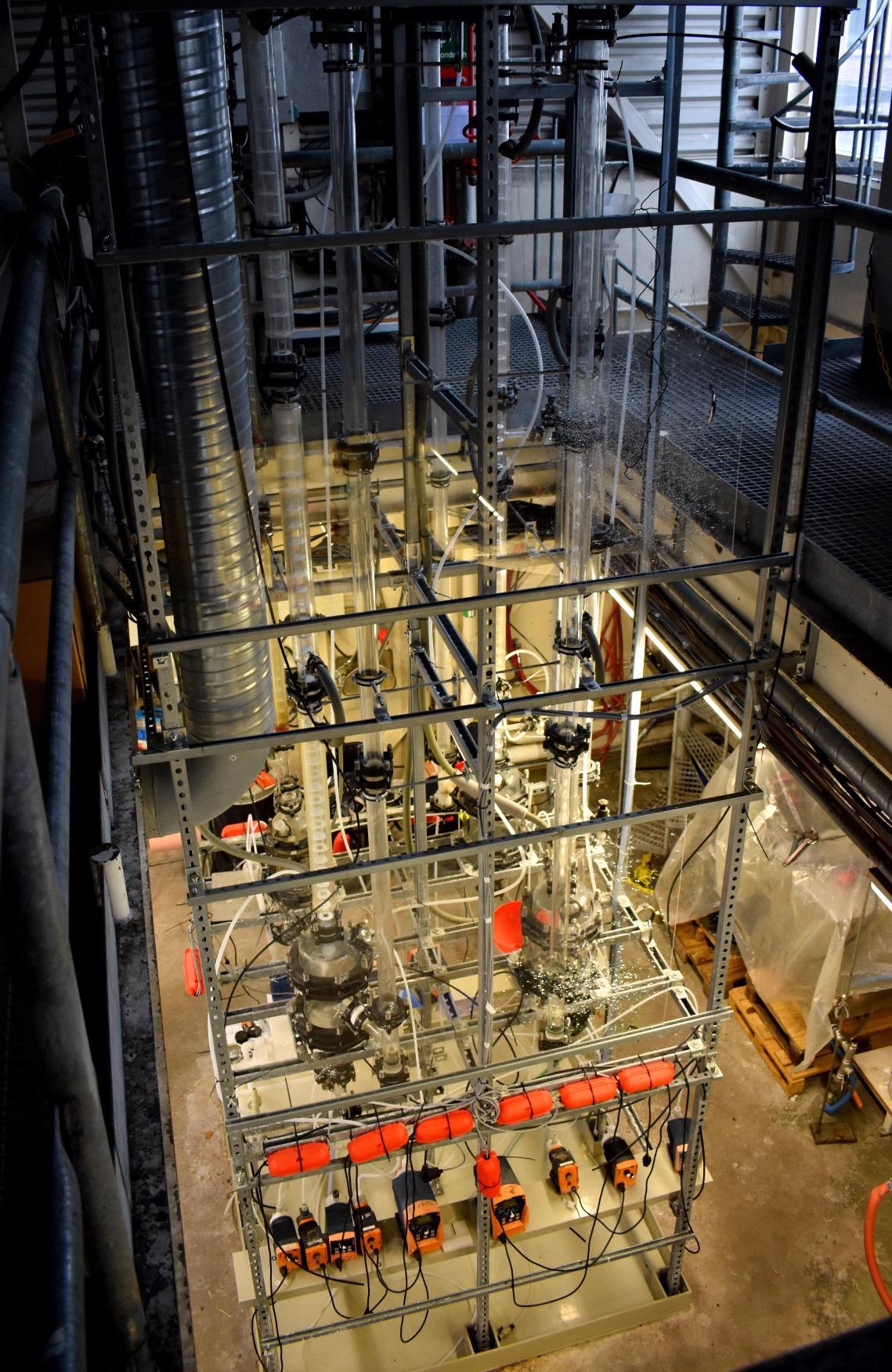
The pilot plant used for research on battery recycling at Chalmers. Image Credit: Chalmers University of Technology
Thermal pretreatment and hydrometallurgy recycling and recovery processes are currently attaching a lot of interest. Can you tell us more about what these processes involve?
Thermal pre-treatment (heating up of the waste in the furnace at the temperature from 400-700 °C) is applied to deactivate the cells or to remove the organic components (electrolyte and binders).
This maximizes the metal compound’s recovery. If the electrolyte is removed, than the rest can be handled in a safer way, and if the binder is removed, more cathode materials can be recovered and less of the impurities (current collectors in the form of aluminum and copper foils) will enter the chemical processing.
Hydrometallurgy is based on two main steps. The first is the dissolution of the solid waste using mineral acids and additives (aka leaching). Once the metals are dissolved (present in the ionic form) their separation is needed. Methods used are precipitation, solvent extraction – the use of the selective organic molecules and ion-exchange – and the use of selective solid resins. Usually, precipitation is applied to remove the impurities such as aluminum, copper, and iron. Solvent extraction is used to separate manganese, cobalt, and nickel. Lithium is usually recovered last via precipitation.
How are thermal pretreatment and hydrometallurgy processes affected by each other?
Significantly. Thermal treatment can reduce the cathode materials from more complex oxides to more “leachable” forms using only the carbon from the waste. The hydroprocessing is then much faster without the need for additive chemicals.
Another advantage is that solid residue after the dissolution is generated in lower volumes and is purer. It is mostly residual graphite, which can be used for another application.
How will your team’s research help make a difference for developers in these areas?
We are actively cooperating with several recycling companies and helping them to optimize their processes.
How could costs be reduced in EV battery charging and why is this important?
Via the optimization of each step, since every unnecessary step brings higher costs to the entire process. I believe that the best model is when the battery producer is also a battery recycler. In that case, they know where to stop in the purification step, which metals to remove, and which ones separate from each other.
Another crucial step is to optimize the mechanical pre-treatment. Material recovery rate should be improved as well as the separation of the components. In that case, chemical treatment will be cheaper since less of the impurities have to be removed. This is important as it increases the motivation for recycling. Nowadays, the main motivation is a directive and metal (cobalt) price. But the concentration of cobalt is decreasing in new batteries. Thus, if recycling is too expensive, there will be a lack of motivation to recover materials beyond the directive requirement.
What challenges has your team faced during your research and how have these been overcome?
I would say too many ideas and too little time. There are a lot of approaches we could choose. Some more on the basic research platform and some more on the applied research side. So, we have to balance which one will we apply for a given task. In this research, we decided on a more applied approach due to the collaboration with the industry.
What are the next steps for the project?
We are currently focusing on improved lithium recovery. Therma pre-treatment allows its transformation to a leachable form just with water. It can be recovered before all the other metals and its loss can be minimized. We are currently achieving 93% recovery and 98% purity, but we want to achieve higher numbers.
Where can readers find more information?
https://doi.org/10.1016/j.wasman.2021.11.030
https://doi.org/10.3390/met11081240
About Martina Petranikova
Martina Petranikova and her research group have carried out research into recycling metals found in lithium-ion batteries for several years.
The group has particular expertise in hydrometallurgy and solvent extraction and a unique position in this field. This way of recycling gives a higher degree of purity of the recovered metals, compared to pyrometallurgy.
Since the heat that it requires is considerably lower, it is also much more energy efficient. The interest in research and development in hydrometallurgy is currently very high, partly due to new stricter EU rules for battery recycling. Last year alone, the Chalmers group published a dozen scientific articles.
Martina Petranikova has led a team of researchers from Chalmers who were part of developing the recycling process for the company Northvolt.
The group is involved in collaborations with several companies that are developing EV battery recycling and partners in major ongoing research and development, in Sweden and internationally, such as the project NyBat by Volvo Cars and Northvolt.
Disclaimer: The views expressed here are those of the interviewee and do not necessarily represent the views of AZoM.com Limited (T/A) AZoNetwork, the owner and operator of this website. This disclaimer forms part of the Terms and Conditions of use of this website.