In the year 2009, the global economic downturn in general and the Spanish market crash in particular almost shut down the solar power manufacturing industry. However, during the third and fourth quarters of the year the PV industry experienced extraordinary growth in a number of segments.
According to marketing research firms, the production volume of silicon solar cells in 2009 was over 8GW, with more than 50% growth over 2008. Throughout the second half of 2009, nearly all cell manufacturers were operating at full capacity and this trend went on till 2010.
Additionally, despite concerns over the German government cut of the feed-in tariff (FIT) in July 2010, the general outlook for the PV industry was positive. In fact, a number of leading solar cell producers announced plans to expand production capacity. These companies also agreed that the PV industry must achieve grid parity in the utility markets as early as possible, rather than depending on government incentive programs. Several key players in this industry are already targeting a goal of $1 per watt between 2012 and 2015. To this end, solar cell manufacturers, equipment vendors, and material suppliers would need to join forces to meet this goal.
Fundamentals of Silver Paste
Some similarities exist between conventional thick film applications and silver paste for silicon solar cells. The manufacturing process, components of the paste, and certain application processes are quite similar. For instance, glass helps penetrate antireflective layers and silver powder provides conductivity, but it is the systematic grouping of all functional elements that distinguishes the performance of one paste from another.
Factors Affecting Efficiency of Silicon (Si) Solar cells
While the theoretical efficiency of a Si solar cell is nearly 29%, most production screen-printing cells are presently running at ~16.3% for multi crystalline cells and ~18% efficiency for mono crystalline cells. However, a number of factors from both the processing side and material side can considerably affect cell efficiency.
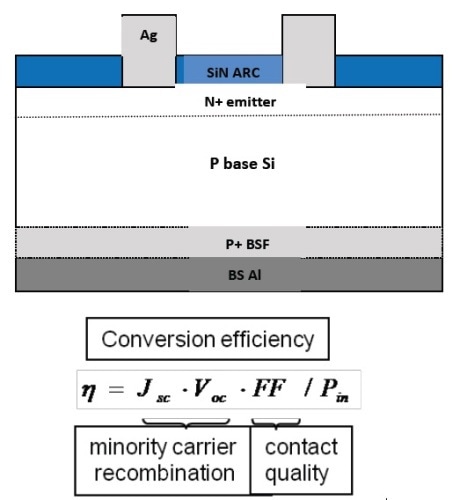
Figure 1. Schematic of traditional Si solar cell and efficiency equation factors of efficiency loss
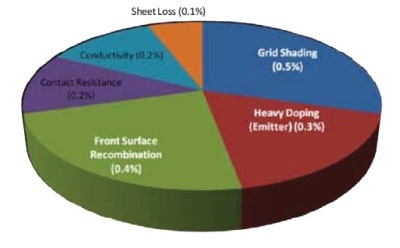
Figure 2. Loss factors in screen-printing Si solar cells
Figure 2 shows the loss mechanism in screen-printing production cells in comparison to photolithography lab cells. Despite improvements in screen-printing and pastes, major efficiency loss still results from grid shading, poor short wavelength response, and metallization pastes contact quality.
Differentiators of Silver Paste for Si Solar Cell
Contact Resistance:
"Spike firing”, one of the unique processing steps for silicon solar cells, presents a major challenge for silver paste. The low contact resistance of the paste is one of the most differentiating factors among the commercially available silver pastes for N+ contact.
Line Conductivity
A few trends in the industry, such as two steps of metallization, double printing, and three busbar designs are targeted at enhancing finger line conductivity. A silver paste which is well formulated could have nearly 50% higher conductivity when compared to other pastes.
Finger Aspect Ratio
PV cell manufacturers prefer single print with a target of high aspect ratio due to the complex nature of double printing. The capability to obtain finger lines with higher aspect ratio is another factor that distinguishes the commercially available silver pastes in the market today. Figure 3 depicts a comparison of finger lines between a non-Heraeus silver paste and Heraeus silver paste SOL9235H.
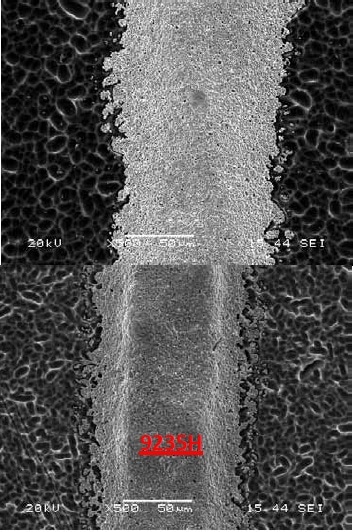
Figure 3. Higher aspect ratio of Heraeus SOL9235H
SOL9235H silver paste provides higher current density of cells owing to reduced shading from fingers and lower series resistance. The morphology is completely different, with SOL9235H providing narrower, but taller finger lines.
Adhesion Strength
Adhesion of silver paste is an important aspect and helps in extending the lifetime of cells. While there is no industry standard for adhesion testing, failure mode and pull strength are often two differentiators for silver paste. Flux types, ribbon types, and soldering methods and profiles affect both paste adhesion and solderability.
Firing Window
Since the actual wafer temperature during firing is influenced by furnace temperature fluctuation, emitter uniformity and AR coating uniformity, each wafer will see large temperature variations. This is one of the aspects that contribute to variation in efficiency. However, in many production lines SOL9235H has shown to maintain a high efficiency during wider temperature processing windows over other pastes.
Benefits of SOL9235H Silver Paste
In 2009, a renowned precious metals management and materials supplier, Heraeus launched its flagship product called SOL9235H silver paste in the silicon PV market. The silver paste significantly improves the performance-to-cost ratio of silicon solar cells. In fact, customers who used Heraeus paste in their production line saw an efficiency gain of 0.2% to 0.4% over other silver pastes on both mono crystalline and multi crystalline cells. This translated into a cost saving of 6% to 12% per cell.
Heraeus has recently launched SOL9383 silver paste for N type cell P+ contact application, which increases the cell efficiency to 19%. Later in 2010, the company launched new front side contact pastes for traditional cells.
Conclusion
Heraeus silver paste SOL9235H has a unique chemistry and offers one of the lowest contact resistance measurements in the PV industry. This translates into the highest fill factor of cells on a broad range of sheet resistance emitters, from 50 to 80ohm/sq. Heraeus develops silver pastes that help the PV industry increase cell efficiencies and output. These pastes can be produced at the company's worldwide production sites in large volumes.
About Heraeus Photovoltaics
The Heraeus Photovoltaics Business Unit is an industry leading developer and manufacturer of metallization pastes for the photovoltaic industry.
Heraeus has been a manufacturer of thick film pastes for over 40 years. Since 2008, we have been an innovative supplier to the photovoltaics industry, working with c-Si cell manufacturers to improve their cells’ efficiency for both conventional and advanced cell designs.
Heraeus have developed silver metallization pastes that have been integrated into commercially available technologies such as MWT, Double Print, Dual Printing, Selective Emitter, Back Side Passivation and N-Type Cells.
Heraeus have also expanded our capabilities and developed lower temperature processing pastes for Thin Film and other c-Si technologies.
Heraeus' goal is to improve our customers’ cell efficiency and reduce their cell’s cost per watt through our innovative paste design technology.
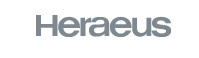
This information has been sourced, reviewed and adapted from materials provided by Heraeus Photovoltaics.
For the original article, please visit Heraeus Photovoltaics white papers and articles.