Sep 15 2008
Scientists from the Carlos III University of Madrid (UC3M) have developed a system that can improve the efficiency of the conversion process of biomass to fuel gas that will contribute to the production of energy in a more sustainable manner.
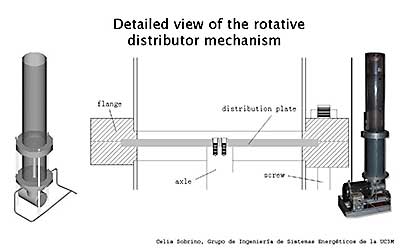
One of the challenges that chemical engineers face is placing solid materials in contact with gases to generate certain reactions. One of the options is to use a fluidised bed, consisting of a vertical cylinder with a perforated plate inside where solid particles are introduced using pressurised air.
This way, the solid particles are suspended, and behave much like boiling water. Solids behaving like a liquid depend on the speed of the air stream, making it key to achieving the desired behaviour. With insufficient air, the particles don’t move, but with too much the opposite happens, and they are carried away by the air stream.
Fluidised beds have relevant environmental applications because they allow the gasification of biomass to produce energy. That is, producing fuel gas from crushed biomass which can then be used for energy production. According to one of the authors of the study, Mercedes de Vega from the Energy System Engineering Group of the department of Thermal and Fluid Engineering of the UC3M, using fluidised beds as chemical reactors allows for a more efficient conversion by achieving high mixing degrees and high exchange rates of mass and heat.
This renewable source has great potential in Spain, especially in processes of co-combustion, direct combustion, and gasification. The applications are mainly industrial, open to be used in motors for the production of electricity, in gas turbines, drying processes, as well as in the pharmaceutical industry for the treatment of powder.
Greater efficiency
The study analyses the behaviour of a new bed designed with a rotating base. The base consists of a perforated plate where holes represent just 1% of its total area. The study evaluates the performance of this new design, considering the increase in pressure and the quality of the fluidisation. It also analyses the effect of the rotation speed of the perforated plate on the performance of the fluidised bed. This type of beds can usually present problems such as agglomeration of solid particles and points of high temperature. But one of the most important conclusions determined that the rotating perforated plate reduces these problems by maintaining a very uniform fluidisation.
The researchers now propose, for future investigations, to study different rotation speeds over a hundred revolutions per minute, and to alter the configuration of the holes in the plate. Celia Sobrino, author of the study, states that the new rotating distribution plate produces smaller bubbles inside the fluidised bed and distributes them better, while improving the efficiency of the conversion in gasification applications.
The study ‘Fluidization of Group B particles with a rotating distributor’ carried out by the Energy System Engineering Group of the department of Thermal and Fluid Engineering of the Carlos III University of Madrid has been published in the journal Powder technology.