A new collaboration between the US Department of Energy’s (DOE) Argonne National Laboratory and Toyota Motor North America is exploring a method for recycling battery components directly, reducing waste and reliance on foreign materials.
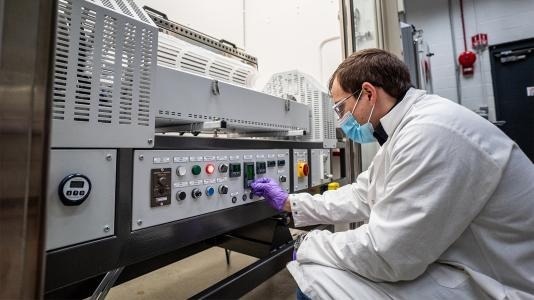
A step in Argonne’s direct recycling process. Image Credit: Argonne National Laboratory
To ensure a successful transition to clean energy in the US, the production of electric vehicle (EV) batteries must be significantly expanded. However, the US depends heavily on other countries for the materials required for these batteries, making it vulnerable to supply chain disruptions.
Argonne, Toyota Research Institute of North America, and Toyota's Battery Lifecycle Solutions group are investigating novel approaches to recycling battery components. If successful, this endeavor could strengthen and improve the circularity of domestic battery supply chains, allowing the United States to deploy EVs quickly.
A Cheaper, Less Wasteful Recycling Process
Most battery recycling involves chemically disassembling end-of-life battery components to produce the raw materials needed for manufacture. In contrast to this conventional method, a process known as direct recycling carefully separates the constituent parts of spent batteries. Manufacturers can reuse the components if they preserve their original structure effectively.
Batteries' positive electrodes, or cathodes, have intricate chemical compositions. Their manufacturing procedures are, therefore, expensive and wasteful.
Direct recycling can effectively minimize waste and manufacturing expenses by preserving the cathodes from batteries nearing their end of life. It may also reduce the requirement for pure raw materials.
Direct recycling is cutting-edge in the battery industry, there are a few startup companies with small-scale pilot projects underway. But implementation at commercial scale is still in need of innovations.
Albert Lipson, Principal Materials Scientist, Argonne National Laboratory
Applying Argonne’s Direct Recycling Process to Toyota’s Batteries
Argonne and Toyota Motor North America have signed a cooperative research and development agreement to create a direct recycling method for the cathodes in lithium-ion batteries, which are common in electric vehicles. The group focuses on cobalt, manganese, and nickel cathodes.
The partnership uses a successful, patent-pending direct recycling method created by the ReCell Center in Argonne. Batteries' cathodes and anodes, or negative electrodes, are separated using a magnet.
Toyota is supplying Argonne with both end-of-life and new plug-in hybrid EV batteries.
Besides recycling end-of-life batteries, we are also interested in recycling new batteries, manufacturers produce some battery cells that fail quality testing. We can potentially demonstrate that manufacturers can take cathodes out of failed cells and put them back into their production process. This capability could translate into huge cost savings.
Albert Lipson, Scientist, Principal Materials Scientist, Argonne National Laboratory
At Argonne’s Materials Engineering Research Facility (MERF), researchers will use ReCell’s direct recycling process on Toyota’s battery cells to extract and regenerate the cathode material. Using coin cells, the team will evaluate different facets of the cathodes' performance, such as capacity, lifespan, and impedance (a form of resistance to electric current).
Researchers at MERF plan to increase the recycling process if the cells function well. Then, using the extracted cathodes, Argonne's Cell Analysis, Modeling, and Prototyping Facility will construct larger pouch cells and evaluate the functionality of the cells. At the same time, Toyota will construct and test cells at its research facilities.
The team will assess the performance of the recycled cathodes against that of new, pristine cathodes. They will also utilize Argonne’s EverBatt model to analyze the costs and environmental impacts of implementing the direct recycling process for Toyota’s batteries.
Albert Lipson concludes, “Our goal is to prove that the process can make high-performing cathodes cost-effectively while reducing energy use and emissions, if we are successful, EV and battery manufacturers can potentially commercialize the process.”
The research project is a component of the ReCell Center, which receives support from the DOE’s Vehicle Technologies Office.