Mar 26 2009
SKF, the leading knowledge engineering company, has launched the third generation version of its successful wind turbine condition monitoring system. SKF WindCon 3.0 is designed to enable wind farms to extend turbine maintenance intervals, manage resources more effectively, and avoid costly downtime.
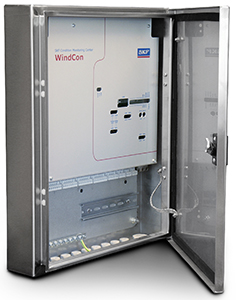
The new WindCon system features CAN-bus interconnectivity to a number of systems typically found in modern wind turbines, such as centralised lubrication, blade monitoring, and gearbox oil condition systems. These elements can be remotely monitored simply and accurately at any maintenance centre with Internet access, using SKF WebCon software.
Using vibration sensors mounted on a turbine’s main shaft bearings, drive train gearbox, and generator, SKF WindCon 3.0 collects, analyses, and compiles a range of operating data that can be configured to suit a wind farm’s specific requirements. The data collected facilitates root cause failure analysis to eliminate recurring failures and keep costs down.
A new brochure is available to accompany the solution, which explains the functionality of the new WindCon 3.0 system in detail and includes information on SKF’s WindLub automatic lubrication solution, which provides wind farms with even greater reliability from turbines.
Additionally, SKF has launched an engineering consultancy service for wind farms, which helps ensure new turbines are able to deliver optimum productivity and reliability, and provides valuable support with troubleshooting a wide range of design related problems.