Advances in carbon capture technologies form keystones in reducing industrial CO2 emissions amidst the incoming climate crisis.
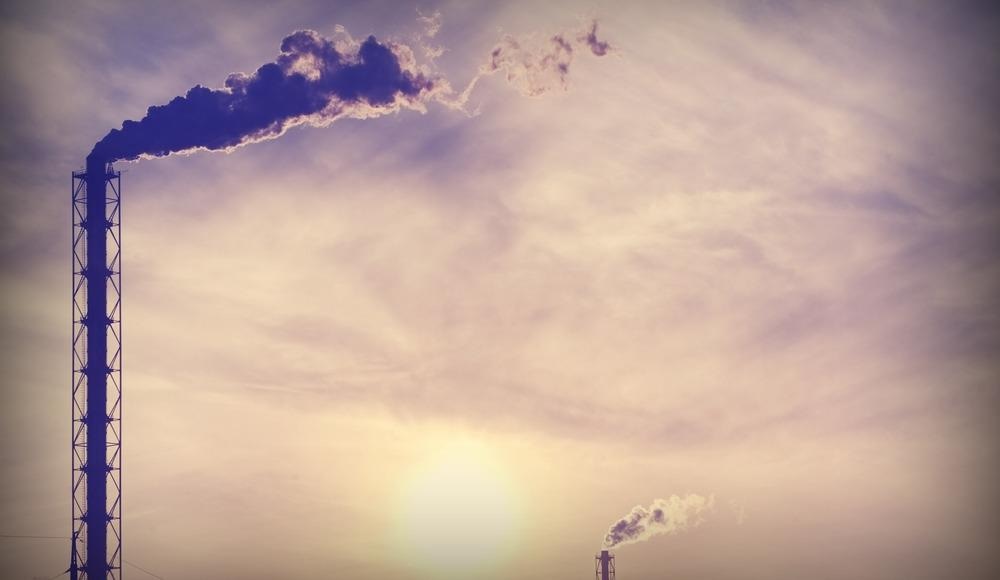
Image Credit: Svetlana Turchenick/Shutterstock.com
Carbon dioxide (CO2) emissions are prevalent in the power and manufacturing industry as it is difficult to develop methods that fully strip CO2 from waste exhaust gases. Decarbonization methods, such as replacing coal with renewable options, have been deployed instead.
Following the COP26, countries have pledged to reduce CO2 emissions to limit the global temperature rise to a maximum of 1.5 °C by 2050. For example, the UK currently relies on fossil fuels to supply 53.1% of its total energy demand to power essential operations, businesses, and households. In comparison, renewable energy supplies only 11.7% of the total demand and is not always reliable since it depends on weather conditions that continuously change.
Until we can design and operate a power supply system consisting of cleaner alternatives to fossil fuels, such as nuclear and hydrogen, carbon capture and storage (CCS) shows the most promise in reducing CO2 emissions from current big emitters.
Carbon Capture Technologies
There are three definitive groups that fall under CCS:
- Post-combustion
- Pre-combustion
- Oxy-fuel combustion
However, carbon capture, utilization and storage (CCUS) also exists as an extension of CCS and has its own separate categories, including direct air capture, where CO2 is captured directly from the atmosphere. It can also be utilized, instead of stored, to make foam packaging, decaffeinating coffee, and cement. The three CCS technologies are as follows:
Pre-combustion
Involves pre-treating the fuel before combustion. These procedures are specific to the fuel being used.
Steam reforming of natural gas enables more H2 to be created as a by-product of combustion, allowing easier separation of CO2 from the flue gas – the post-combustion gases produced in industrial and power plants – as well as producing hydrogen as a by-product, which can also be used a clean fuel source.
Coal or biomass as a raw fuel can be pre-treated similarly and incorporated in the integrated gasification combined cycle (IGCC), which also allows for more H2.
Oxy-fuel combustion
The technology involves the combustion of carbon-based fuel in pure oxygen instead of air. This results in the flue gas having a high CO2 concentration mixed with water vapor, which can be removed easily. The remaining CO2 can be separated easily from the flue gas, however, pre-treatment is required before the CO2 can be separated.
Post-combustion
The raw fuel is allowed to undergo combustion as normal, and the resulting flue gas is then pre-treated to remove any impurities such as sulfates and particulates. The remaining gaseous mixture is passed through a solvent-absorption system to remove the CO2. This procedure is more expensive as the flue gas is at a high temperature and needs to be cooled down; it is also at a low pressure, which needs to be increased before separation.
Carbon Capture Technology Explained | Seachange
Video Credit: Freethink/YouTube.com
Amine Absorption: A Promising Development
A recent study published in the Environmental Science & Technology journal demonstrates how an amine-based absorption system could capture 99% of CO2 from post-combustion flue gas using a simulated system.
The scientists conducting the study have used a solvent-based absorption system that absorbs CO2 from the mixture of gases that are about to be ejected into the atmosphere, hence capturing it.
Monoethanolamine (MEA) is an ammonia derivative commonly used in CCS. However, the scientists modified the solution, demonstrating that, by using the advanced solvents KS-1, CANSOLV, or AMP/PZ (2-aminomethylpropanol/piperazine), this procedure is more cost-effective and accessible.
In general, the higher the percentage of CO2 required for separation from the flue gas, the higher the cost is likely to be. The pressures needed to absorb the last few moles of the gas would be extremely high and would require more power and stronger vessels to contain the pressure.
Research was also conducted on different variations of flue gas that the amine-based absorption system can be used to successfully strip CO2 from. For example, the flue gas of an iron and steel plant or a cement production plant would contain different gases and requires different pre-treatments before the amine-based system can be used for CCS. Therefore, each industry uses different CCS technologies or a combination of two, depending on what works best with their raw fuel and waste gases.
The Future of CCS and CCUS
CCS and CCUS on their own will not be enough to significantly reduce the carbon dioxide present in the atmosphere causing climate change. However, they are effective in ensuring that a reduced amount of CO2 enters the atmosphere.
New technology developments, such as the one conducted in this study, reduce costs and capture as much as 99% of CO2. These developments are essential in reducing overall emissions and ensuring the COP26 targets are reached.
To solve the climate crisis in the long term, CCS and CCUS need to be utilized alongside renewable power sources, green technologies, and nuclear power to replace the current fossil-fuel dependant power supply system.
References and Further Reading
Danaci, D., Bui, M., Petit, C. and Mac Dowell, N. (2021) En Route to Zero Emissions for Power and Industry with Amine-Based Post-combustion Capture. Environmental Science & Technology, 55(15), pp.10619-10632. https://doi.org/10.1021/acs.est.0c07261
Khosroabadi, F., Aslani, A., Bekhrad, K. and Zolfaghari, Z. (2021) Analysis of Carbon Dioxide Capturing Technologies and their technology developments. Cleaner Engineering and Technology, 5, p.100279. https://doi.org/10.1016/j.clet.2021.100279
Disclaimer: The views expressed here are those of the author expressed in their private capacity and do not necessarily represent the views of AZoM.com Limited T/A AZoNetwork the owner and operator of this website. This disclaimer forms part of the Terms and conditions of use of this website.