In April 2022, the prototype for a 100% recyclable wind turbine blade was installed in a facility in Denmark for testing. The world’s largest thermoplastic blade was manufactured in Ponferrada, Spain, and is a crucial milestone for the international ZEBRA Project for zero-waste blade research.
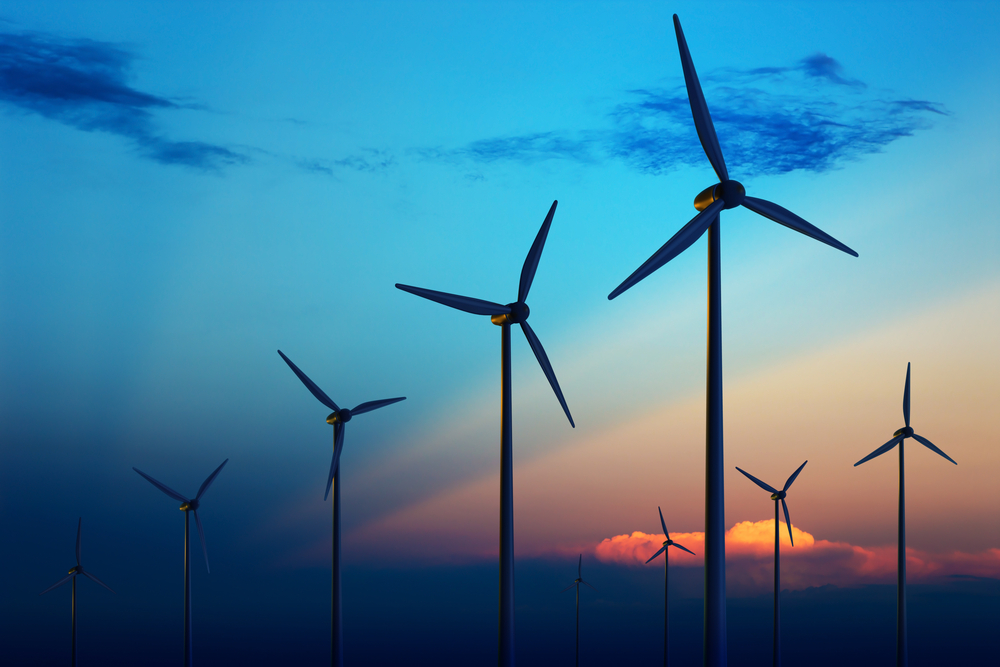
Image Credit: Johan Swanepoel/Shutterstock.com
100% Recyclable Wind Turbine Blade
The wind turbine blade is constructed from Elium resin, a thermoplastic manufactured by consortium partner Arkema. Elium was selected due to its recyclability – it can be shredded and reused as a pellet or extruded into new forms with minimal loss of structural integrity – combined with good performance.
The final blade material includes high-performance glass fabric supplied by project partner Owens Corning along with the thermoplastic. The resulting composite maximizes the strength, flexibility, and weight performance of Elium while maintaining its key feature: recyclability.
Recycling is achieved with a chemical method that depolymerizes the thermoplastic resin in the material to separate out the glass fabric fibers. This recovers a new near-virgin resin as well as high modulus glass. Both recovered materials can be reused with minimal further processing to close the waste loop for the wind turbine blade.
Waste generated in the blade production was also recycled throughout the project, giving partners opportunities to refine the recycling process to maximize efficiency and achieve the best possible sustainable outputs.
The part was produced with a liquid resin infusion process which is well-adapted to manufacturing large parts with strict engineering load requirements, such as wind turbine blades.
Partners focused research and development on automating as much of the production process as possible. This enabled reductions in energy consumption as well as resource needs due to creating less waste.
The project will shift to a full-scale structural lifetime testing phase in LM Wind Power’s test and validation center in Denmark. The blade will undergo tests to verify its performance as a part and the performance of the thermoplastic and glass fabric composite material used to make it.
The testing phase will also evaluate the feasibility of putting the blade into mass production for the wind power market and ensuring wind turbine blades in future installations and retrofits can be recycled. This includes evaluating the blade’s end-of-life processing and validating recycling methods.
The Companies Involved in the ZEBRA Project
Several international technology and industrial companies support the ZEBRA Project. Each represents a separate component of the entire value chain that will allow the construction of the final 100% recyclable wind turbine blade.
Arkema
Arkema Group, which the Wall Street Journal recently ranked as the 11th most sustainably managed company in the world, is a global producer of a wide range of materials ranging from acrylics to thiochemicals. Arkema’s role in the ZEBRA project is primarily through its product Elium®, a thermoplastic resin that has already been successfully integrated into various wind turbine blades. Some of the key advantages of Elium® include its energy efficiency, cost savings, durability, and recyclable properties.
While Elium® is manufactured through many of the same processes responsible for producing other liquid epoxy resins, its energy consumption requirements are much lower, as this specific resin does not require mold heating. In addition to eliminating the need to heat wind turbine components during their assembly, the Elium® has also demonstrated exceptional durability compared to parts made from conventional thermoset composites. Since the ZEBRA project primarily focuses on generating a fully recyclable wind turbine, the incorporation of Elium® is ideal, as its thermoplastic nature makes it easily recyclable.
A wind turbine blade recyclable with Elium®
Video Credit: Arkema Group/YouTube.com
CANOE
A second French company involved in the ZEBRA project is CANOE, a research and development technology center dedicated to developing and manufacturing innovative materials within the composites and advanced materials industries.
As an expert in polymer formulation, CANOE will incorporate its recently developed recycling process of fiber-reinforced acrylic composite materials. This innovative dissolution process provides a high added-value recovery for separate recycled methyl methacrylate monomer and recycled fibers used in the final wind turbine system.
ENGIE
ENGIE has installed several projects worldwide, estimated to reach a total installed capacity of 33 gigawatts (GW) by 2021.
ENGIE has rapidly increased wind farm installation worldwide, including in Mongolia, Mexico, India, and Australia. The international presence and reputation of ENGIE will further promote the ZEBRA project’s goal of achieving a smooth and rapid transition to a carbon-neutral economy.
LM Wind Power
Initially founded in 1940, Denmark-based renewable energy business LM Wind Power has produced over 228,000 wind turbine blades since 1978. With unique expertise in designing and manufacturing wind turbine blades, LM Wind Power will further advance the ZEBRA Project’s 100% recyclable wind turbine.
Owens Corning
With more than 19,000 employees in 33 countries worldwide, Owens Corning is a global leader in the production of building and industrial materials, particularly insulation, roofing, and fiberglass composites.
The High Modulus Glass technology invented by Owens Corning is a crucial aspect of the ZEBRA project. It maintains complete sustainability while ensuring advanced performance rates of the final wind turbine product.
SUEZ
SUEZ began business around 150 years ago and continues to employ over 90,000 employees worldwide to advance its mission of protecting human and environmental health sustainably and economically.
SUEZ is dedicated to creating a more sustainable planet by investing in large wastewater treatment plants, soil remediation plants to eliminate contaminated sludge and soil, and innovative technologies that purify the air while simultaneously producing green energy.
As a leader in the advancement of sustainably managed projects, SUEZ will bring its expertise to ensure that the best recycling techniques are used throughout the 42-month period in which the ZEBRA project will take place.
The Importance of Sustainable Wind Power
In the United States alone, the wind industry is expected to reach a total power capacity of 404.25 GW by the year 2050 across 48 states. While this projection is inspiring for environmentalists, the lack of recyclable materials used in the conventional manufacturing of wind turbine blades limits their utility in making a real long-term and meaningful impact on the globe.
Although approximately 85% of current wind turbines are composed of recyclable and/or reusable materials such as steel, copper wire, electronics and gearing, the wind turbine blades are made of fiberglass, which is traditionally difficult to dispose of. As a result, in the United States alone, it is estimated that 8,000 wind turbine blades that have reached the end of their lifespan will end up in landfills by the end of 2024.
The ZEBRA Project's ultimate goal to create a 100% fully recyclable wind turbine blade will resolve many sustainability concerns currently putting pressure on the wind power industry.
In addition to developing the wind turbine blade itself, the ZEBRA project partners will also invest a considerable amount of effort towards optimizing the manufacturing process of these wind turbine blades to maximize their efficiency while simultaneously reducing any excess energy consumption and waste during this production process.
With a budget of approximately 18.5 million euros, the ZEBRA project's results will inevitably significantly impact the wind power industry and every other green energy project for years to come.
Next Steps for the ZEBRA Project
The ZEBRA Project’s next steps are to develop methods for recycling production waste, dismantling the prototype blade, recycling it, and analyzing the results of long-term testing.
The project will finish in 2023, at which point consortium partners hope to have realized the goal of introducing circular economy loops to the wind energy sector sustainably.
References and Further Reading
New Project to Develop Fully Recyclable Thermoplastic Wind Turbine Blades [Online]. Available at: https://omnexus.specialchem.com/news/industry-news/project-recyclable-turbine-blades
Arkema Group [Online]. Available at: https://www.arkema.com/en/arkema-group/
New award for Arkema’s Elium® technology! [Online]. Available at: https://www.arkema.com/en/media/news/news-details/New-award-for-Arkemas-Eliumsup-sup-technology/
Wind energy [Online]. Available at: https://www.engie.com/en/activities/renewable-energies/wind-energy.
ZEBRA project achieves key milestone with production of the first prototype of its recyclable wind turbine blade [Online]. Available at: https://www.ge.com/news/press-releases/zebra-project-achieves-key-milestone-with-production-of-first-prototype-of-recyclable-wind-turbine-blade
‘ZEBRA project’ launched to develop first 100% recyclable wind turbine blades [Online]. Available at: https://www.lmwindpower.com/en/stories-and-press/stories/news-from-lm-places/zebra-project-launched
Our purpose – SUEZ Group [Online]. Available at: https://www.suez.com/en/who-we-are/a-worldwide-leader/our-purpose
Wind Turbine Blades Can’t Be Recycled, So They’re Piling Up in Landfills [Online]. Available at: https://www.bloomberg.com/news/features/2020-02-05/wind-turbine-blades-can-t-be-recycled-so-they-re-piling-up-in-landfills
Disclaimer: The views expressed here are those of the author expressed in their private capacity and do not necessarily represent the views of AZoM.com Limited T/A AZoNetwork the owner and operator of this website. This disclaimer forms part of the Terms and conditions of use of this website.