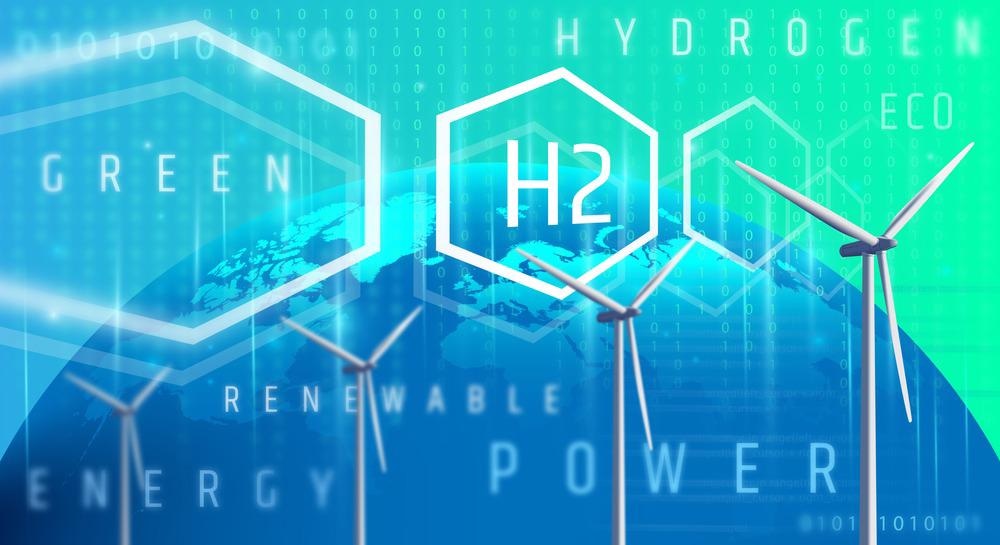
Image Credit: Tomasz Makowski/Shutterstock.com
Globally, we are transitioning to an electrified world; the realization that humanity’s reliance on fossil fuels is responsible for climate change has driven the desire to find alternative ways of providing power for the future. Renewable energy is seen as the solution; energy generated by the sun and wind is being harvested for immediate use or stored for times of peak demand.
Renewable energy is increasingly used to power our transport networks, keep our homes comfortable, and drive industrial processes. While many industries are in the process of switching to renewable fuels, not all can be electrified.
According to a new report from IDTechEx, Green Hydrogen Production; Electrolyzer Markets 2021-2031, some of the most environmentally threatening industries cannot be electrified. This includes the ammonia and gas sectors, as well as the steel industry which uses coal in the coking process to eventually produce steel.
While hydrogen cannot be used in a steel-producing blast furnace, it can be used as an auxiliary agent to reduce the amount of coal needed, and, because it only forms water after reacting with iron ore instead of carbon dioxide, it can reduce emissions. This hydrogen can be produced from renewable energy using electrolyzer systems.
Uses of Hydrogen and Methane Domination
While the use of hydrogen in fuel cells and vehicles is widely noted, this only represents a small part of the hydrogen market. The gas is mostly used for ammonia production and refinery products; the remaining 20% accounts for energy storage, automotive uses and methanol production combined.
Hydrogen production is currently dominated by reforming methane. Steam Methane Reforming (SMR) converts methane into hydrogen using high-temperature steam (between 700 and 1000 °C), a pressure of between three and 25 bar, and a catalyst. The other byproducts are carbon monoxide and a small amount of carbon dioxide. But, while it produces hydrogen relatively inexpensively, it has considerable emissions.
The Future is Green
All electrolyzers use electricity to split water (H2O) into oxygen (O2) and hydrogen (H2), which can be used as an alternative fuel. There are three types, which differ depending on which ions are exchanged at their electrodes. Each type, therefore, requires different electrolytes and materials, which can have an effect on their performance and properties.
AWE: The oldest type is the alkaline water electrolyzer (AWE). It was first adopted at an industrial scale in the 1920s and has dominated commercially for the last century. It has two electrodes in a liquid alkaline electrolyte of potassium hydroxide or sodium hydroxide, and exchanges OH- between its electrodes.
PEMEL: Proton exchange membrane electrolyzers (PEMEL) have emerged in the last 20 years or so as an innovative and more efficient means of splitting water. The cell is prepared with a solid polymer electrolyte that aids the conduction of protons, separation of product gases, and electrical insulation of the electrodes, where it exchanges H+.
SOEL: Solid oxide electrolyzers (SOEL) are making their way to market. It runs in reverse mode, i.e., the anode becomes the cathode and vice versa, to split water using a solid oxide or ceramic electrolyte to produce hydrogen. SOEL operate at a much higher temperature compared to AWE and PEMEL (between 600 and 850 °C compared to between 50 and 90 °C), and exchange O= between electrodes.
Although it requires resistant materials and is more expensive to fabricate, the higher temperature negates the use of expensive catalysts and enables the use of other fuels such as carbon dioxide and water vapor to obtain syngas, another important industrial feedstock.
Green Hydrogen
To decarbonize the sector and create a strong hydrogen economy, electrolyzer systems must provide green and high-purity hydrogen utilizing renewable electricity. This is likely to have a higher cost and needs the strong financial backing of the industry.
Despite being in the early stages, there is strong support for the use of electrolyzers for hydrogen production, with the European Parliament highlighting its importance in the future economy in the ‘Green Deal’.
As a result, many countries are promoting the adoption of hydrogen strategies, and electrolyzer systems are likely to be vital to their success, with projects in Europe, Australia, Chile, Japan, South Korea, and Canada.
References and Further Reading
Gatti, D. (2021), Electrolyzers are the First Step Toward Green Hydrogen Production, IDTechEx: https://www.idtechex.com/en/research-article/electrolyzers-are-the-first-step-toward-green-hydrogen-production/23478. Accessed 15 April 2021.
Gatti, D. et al (2021), Green Hydrogen Production: Electrolyzer Markets 2021-2031, IDTechEx: https://www.idtechex.com/en/research-report/green-hydrogen-production-electrolyzer-markets-2021-2031/807. Accessed 15 April 2021.
Office of Energy Efficiency and Renewable Energy, Hydrogen Production: Natural Gas Reforming, energy.gov: https://www.energy.gov/eere/fuelcells/hydrogen-production-natural-gas-reforming. Accessed 15 April 2021.
Bellona Europe, (2021), Hydrogen in steel production: what is happening in Europe – part one, Bellona Europe: https://bellona.org/news/climate-change/2021-03-hydrogen-in-steel-production-what-is-happening-in-europe-part-one. Accessed 15 April 2021.
Disclaimer: The views expressed here are those of the author expressed in their private capacity and do not necessarily represent the views of AZoM.com Limited T/A AZoNetwork the owner and operator of this website. This disclaimer forms part of the Terms and conditions of use of this website.