Carbon dioxide emissions are a major global threat; human activity, namely the combustion of fossil fuels, releases the equivalent of 40 billion tons of greenhouse gas into the atmosphere each year, driving up temperatures worldwide.
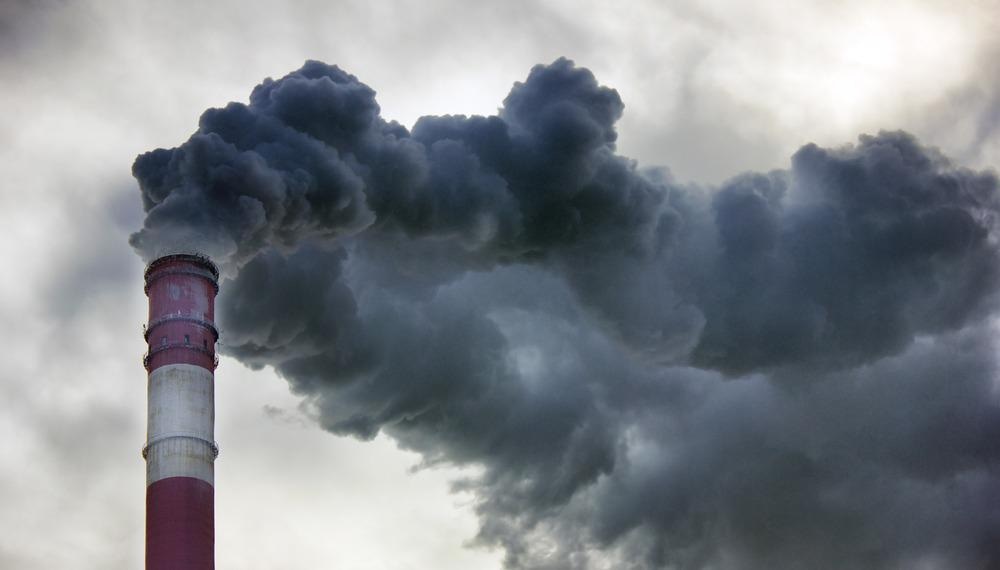
Image Credit: Anastasiia Tymoshenko/Shutterstock.com
It is predicted that global temperatures will rise by 1.5 °C above preindustrial levels by 2040; humanity needs to limit it to this temperature rise to avoid the most dangerous impacts of climate change. Emissions need to be reduced, immediately and dramatically, to ensure the future of our planet.
Mosaic Materials: Negative Emissions Technology
One means of achieving this is with negative emissions technologies (NETs) which remove and sequester the offending gas, preventing it from ever being released into the atmosphere. Such technologies are likely to form part of a vital strategy to mitigate the effects of climate change.
California-based cleantech innovator, Mosaic Materials, aims to create a cleaner future with advanced materials. It utilizes a promising NET called a metal-organic framework (MOF) in a proprietary gas separation technology that selectively removes pollutants, such as CO2, from a mixture of gases.
Mosaic Materials’ highly efficient CO2 removal technologies lower the cost and environmental impact of fossil fuels and could find applications in submarines to improve the quality of breathable air, or in power plants to remove CO2 from waste gases.
Gas Separation Solutions using Metal-Organic Frameworks
Mosaic Materials’ novel gas separation solutions rely on metal-organic frameworks, a class of highly porous crystalline solids that essentially function like ultra-high-capacity sponges for gases.
MOFs have been around for 20 years, but it is only in the last decade that there has been an explosion in research. They consist of metal ions or clusters and an organic molecule called a linker in structures that may be one, two, or three-dimensional. The MOF’s structure and properties are determined by the choice of metal and linker.
MOFs have a very high internal surface area. Approximately 1 g of MOF – roughly equivalent to a cube of sugar – can have a surface area greater than the size of a football field. It possesses a large number of adsorption sites, where gas molecules become stuck to the surface, meaning a small amount of MOF can remove huge amounts of CO2 from exhaust gases produced by burning fossil fuels.
The MOF’s adsorption sites can be chemically tuned to selectively capture a specific gas from a complex mixture of gases. By changing the chemical properties of the adsorption sites, the MOFs can be designed to meticulously seize and remove CO2, using significantly less energy than competing CO2 removal technologies.
The unique performance characteristics of Mosaic’s gas separation solutions rely on cooperative binding, a process first developed by the company’s co-founders, Dr Thomas McDonald, Professor Jeffrey Long, and Dr Steven Kaye, at the University of California, Berkeley.
This one-of-a-kind switch-like mechanism allows the MOF to adsorb large quantities of CO2 more efficiently than other adsorbents, but then undergo regeneration using a moderate temperature or pressure, significantly increasing energy efficiency and reducing costs.
The process was optimized for the efficient removal of CO2 from the flue gas of a power plant, demonstrating that CO2 can be removed with high efficiency and low cost. Furthermore, the technology was shown to significantly outperform other gas separation technologies, such as absorption and distillation.
Potential Applications
MOFs are proving interesting for several applications, including the storage of gases such as carbon dioxide and hydrogen, in biological imaging and sensing, and in drug delivery systems. Other areas receiving attention are gas purification and gas separation, in catalysis as conducting solids, and as supercapacitors for energy storage.
Mosaic Materials are working on a number of gas separation solutions utilizing metal-organic frameworks. MOF technology could be used to slow the rate of CO2 emissions from large emitters such as coal and natural gas power plants and other industrial sources by capturing the greenhouse gas from a mixture of waste gases before it is released into the atmosphere.
It also has the potential to improve breathing air quality within confined spaces, such as submarines, or on space missions. The MOF is designed to selectively remove CO2 - exhaled by submariners and astronauts – from the air, allowing it to be safely recirculated.
The technique could also be used in paraffin and olefin separation. Natural gas is used as a raw material to make chemicals and plastics; Mosaic’s new MOF technology could replace the energy-intensive processes currently utilized to separate ethylene and propylene – used in plastics – from a mixture of gases.
The technology could also be used to sweeten natural gas. This is the process of removing impurities such as carbon dioxide, hydrogen sulfide, and mercaptans (organic sulfur compounds) to make them safe for transporting and for sale. The gas must be sweetened as carbon dioxide and hydrogen sulfide are corrosive, and so affect the gas pipeline, and are toxic to humans.
The Future of using Metal-Organic Frameworks for Gas Separation
Formed in 2014 specifically to pursue the commercial production of MOFs for CO2 separation processes, Mosaic states its technology can be used to separate greenhouse gas from almost any gas mixture, from raw natural gas to recirculated breathing air. It is certainly promising, having recently won the Early Stage Outstanding Venture award from the US Department of Energy’s National Renewable Energy Laboratory.
The technology is, relatively speaking, still in its infancy. More research is required to lower the cost of the process and further improve materials. At present, the cost of removing carbon dioxide is between $500 and $1000 per ton. This high cost can be attributed to the energy required to regenerate the MOF adsorbent so that it can be used to capture more CO2.
The company aims to reduce the cost to around $100 per ton by developing materials that have a high capture rate, fast kinetics for gas adsorption, and a lower regeneration temperature. It also hopes to limit the co-adsorption of water to reduce the amount of energy wasted on its desorption.
References and Further Reading
Lawrence Berkeley National Laboratory (2021) A Sponge to Soak Up Carbon Dioxide From the Air [Online] SciTechDaily. Available at: https://scitechdaily.com/a-sponge-to-soak-up-carbon-dioxide-from-the-air/
Mosaic Materials [Online] Available at: https://mosaicmaterials.com/
Kennedy, H. (2021) Mosaic Materials, Opus 12, others win NREL cleantech innovator award [Online] The Digest. Available at: https://www.biofuelsdigest.com/bdigest/2021/04/25/mosaic-materials-opus-12-others-win-nrel-cleantech-innovator-award/
Generon (2019) What is gas sweetening? [Online] Generon. Available at: https://www.generon.com/amine-gas-sweetening-process/
Disclaimer: The views expressed here are those of the author expressed in their private capacity and do not necessarily represent the views of AZoM.com Limited T/A AZoNetwork the owner and operator of this website. This disclaimer forms part of the Terms and conditions of use of this website.