Scientists in Japan have developed an energy-efficient means of converting carbon dioxide (CO2) into functional materials. The new method transforms CO2 into structures known as metal-organic frameworks (MOFs). This cutting-edge research may provide a better and simpler way of taking CO2 out of our atmosphere, as well as being a viable synthesis method for MOFs, which have a range of applications.
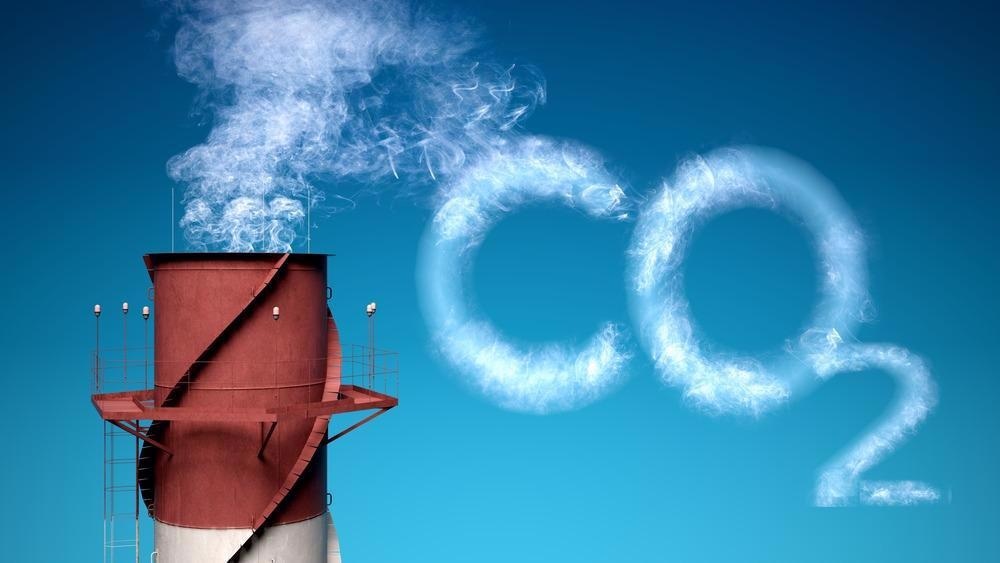
Image Credit: Billion Photos/Shutterstock.com
This development was the result of research carried out by scientists at the Institute for Integrated Cell-Material Sciences (iCeMS) based in Kyoto University, Japan, and colleagues. The results were published in the Journal of the American Chemical Society.
CO2 Conversion Technology for a Carbon-Neutral Future
Converting CO2 into functional materials at room temperature has been a major challenge for scientists seeking to usher in the future carbon-neutral society we need to avoid the worst-case scenario outcomes of climate change.
Since CO2 is a very inert and stable molecule, it has been challenging to make it react with conventional conversion processes. The latest research shows that converting CO2 can be possible at ambient conditions, with relatively low environmental temperature and pressure.
Making it simpler – and less resource and energy-intensive – to convert CO2 can have wide-reaching benefits, according to the study’s authors. Reactions that need to use CO2 can be popularized, leading to more demand for captured carbon and therefore more carbon capture activity taking place.
MOFs: Widely Applicable Functional Materials
The team from Kyoto University targeted MOFs as the end product for its CO2 conversion technology due to their wide range of applications, such as in biosensors and catalysts. MOFs’ porosity also means that these structures can hold large amounts of gas, generating interest in them as potential storage devices for sustainable hydrogen fuel.
MOFs have been studied extensively due to their designability – their structures can be fine-tuned and precisely controlled to optimize their performance.
MOFs consist of metal ions or clusters that are coordinated to organic ligands. This forms one-, two-, or three-dimensional structures. MOFs are a subclass of coordination polymers, differentiated from other coordination polymers by their high porosity.
In some MOFs, pores are stable while guest molecules such as solvents are eliminated, and they can be refilled with other compounds. This makes them particularly interesting for gas storage applications, such as for hydrogen and CO2.
MOFs are also widely applicable in a number of sectors. They can be used in gas purification, gas separation, water remediation, catalysis, conduction, and supercapacitor applications.
Synthesizing MOFs
The wealth of possible applications for MOFs has resulted in several synthesis methods being developed in recent years.
Solvothermal synthesis grows crystals that are suitable for structure determination, growing over a period of hours or days. However, this method is not scalable and will not be used to produce MOFs for large-scale applications such as in consumer products.
Several studies have proposed using regular kitchen microwaves to nucleate MOF crystals rapidly from the solution. So-called “microwave-assisted solvothermal synthesis,” sees much use in research on zeolites, and it produces micron-scale crystals at similar yields to previous methods in just minutes or even seconds.
MOFs such as the mesoporous MIL-100(Fe) can be obtained at room temperature in mild conditions using just green solvents (water and ethanol). This synthesis method is also scalable, according to the researchers who developed it.
A range of crystalline MOFs has been synthesized without using solvents. Typically, the metal acetate and organic proligand are combined with ball mill and ground up. Cu3(BTC)2 can be synthesized quickly in this way, and with a large-scale yield.
Solvent-free MOF films and composites synthesis has also seen developments recently with the introduction of chemical vapor deposition. The process, MOF-CVD, has been successfully scaled up to an integrated cleanroom process that abides by industrial microfabrication standards.
The Kyoto University team noted that, even though it is an attractive resource for several environmental reasons, CO2 had been largely unexplored as a potential MOF synthesis material. This was due to the chemical inertness of CO2 that stops it from being converted into typical MOF linkers such as carboxylates without high energy requirements or harsh conditions.
How Did Researchers Achieve Results?
In the research, CO2 was simmered at a temperature of 25 °C and a pressure of 0.1 MPa, in a solution with piperazine, an organic molecule. Chemists refer to processes like this as “one-pot” procedures, prized for their simplicity and scalability.
This resulted in synthesized cubic [Zn4O(piperazine dicarbamate)3] that formed in situ with bridging dicarbamate linkers from piperazines and CO2.
The team performed nuclear magnetic resonance spectroscopy to confirm that the conversion took place as expected. The resulting MOF material showed high surface areas (∼2366 m2 g–1) as well as high CO2 contents (>30 wt %).
These features make the structures suitable as functional materials in a wide range of applications for MOFs.
References and Further Reading
Batten, S.R., et al. (2013). “Terminology of metal–organic frameworks and coordination polymers (IUPAC Recommendations 2013).” Pure and Applied Chemistry. Available at: https://doi.org/10.1351/PAC-REC-12-11-20.
Choi, J-S., et al. (2008). “Metal–organic framework MOF-5 prepared by microwave heating: Factors to be considered.” Microporous and Mesoporous Materials. Available at: https://doi.org/10.1016/j.micromeso.2008.04.033.
Cruz, A.J., et al. (2019). “Integrated Cleanroom Process for the Vapor-Phase Deposition of Large-Area Zeolitic Imidazolate Framework Thin Films.” Chemistry of Materials. Available at: https://doi.org/10.1021/acs.chemmater.9b03435.
Kadota, K. et al. (2021). “One-Pot, Room-Temperature Conversion of CO2 into Porous Metal–Organic Frameworks.” Journal of the American Chemical Society. Available at: https://doi.org/10.1021/jacs.1c08227.
Ni, Z., and R.I. Masel (2006). “Rapid Production of Metal−Organic Frameworks via Microwave-Assisted Solvothermal Synthesis.” Journal of the American Chemical Society. Available at: https://doi.org/10.1021/ja0635231.
Pichon, A., and S. L. James (2008). “An array-based study of reactivity under solvent-free mechanochemical conditions—insights and trends.” CrystEngComm. Available at: https://doi.org/10.1039/B810857A.
“Simple method for converting carbon dioxide into useful compounds.” (2021) Kyoto University. Available at: https://www.icems.kyoto-u.ac.jp/en/news/6312/.
Stassen, I., et al. (2015). “Chemical vapour deposition of zeolitic imidazolate framework thin films.” Nature Materials. Available at: https://doi.org/10.1038/nmat4509.
Steenhaut, T., S. Hermans, and Y. Filinchuk (2020). “Green synthesis of a large series of bimetallic MIL-100(Fe,M) MOFs.” New Journal of Chemistry. Available at: https://doi.org/10.1039/D0NJ00257G.
Disclaimer: The views expressed here are those of the author expressed in their private capacity and do not necessarily represent the views of AZoM.com Limited T/A AZoNetwork the owner and operator of this website. This disclaimer forms part of the Terms and conditions of use of this website.