This interview is with Alex Blum, the CEO of Applied Bioplastics and award-winning philanthropic filmmaker. Blum has had a fantastic career and heads a company leading the way in the bioplastics industry with its development of innovative decarbonized plastics used in refugee housing. AZoCleantech delves into Alex Blum's career, plastic recycling challenges, and what Applied Bioplastics brings to the sustainable plastics industry.
Can you tell us briefly about your career so far and your role at Applied Bioplastics?
I spent most of my early career as a salesman, and my last role consisted of selling network monitoring software to the enterprise. I did very well in that role, and in my second year, I closed my entire annual quota in the first two months of the year.
As a debt-free 27-year-old, I donated 100% of my bonus check to charity. I gave to local Austin charities anonymously, but that did not scratch my itch to actually help people. A few months later, a friend called and told me that two million refugees had crossed the border from Myanmar into Bangladesh. He said Bangladesh could help with this crisis, so I booked a flight.
When I arrived in Bangladesh, I realized the scale of the problem was beyond what I could ever imagine, so I settled for the second-best thing: I spent my funds to hire a director and a film editing studio. Together, we made a documentary in the world’s largest refugee camp in only three weeks, a film I wrote, narrated and was the sole producer of.
This film won multiple awards, including the Special Jury Remi Award at the WorldFest International in Houston, where it was picked up by a distributor and put on Amazon.
Parts of the film were also used as evidence against the government of Myanmar in international court. I was then introduced to Dr. Mubarak Ahmad Khan, a senior scientist in biopolymers, who had invented a technology that enabled the use of a common agricultural product and a common thermoset resin to produce rudimentary housing using zero power, specialized tools, or even exceptionally well-trained labor. I asked him if he needed help commercializing the product, and he told me in no uncertain terms that the invention was his baby and he would not partner with me in its use.
So I went home, but I could not get the idea of highly sustainable housing that would benefit the host community of the refugees off my mind. I presented the idea to my housemate, Colin Ardern, and asked him to help me.
Together, we spoke with and then hired several plastics experts. These scientists told us they thought they could convert the housing technology into something that would benefit the plastics industry as a whole. I stayed in touch with Dr. Khan, and after about six months of negotiating, Colin and I flew back to Bangladesh to sign an IP transfer agreement for the housing material and an employment contract with him.
We worked together for two years and eventually began a pilot in the refugee camp, creating villages for the people there. We incorporated the company in June 2019 after quitting our jobs to focus on Applied Bioplastics full-time.
I began as the company’s Chief Impact Officer, and as our roles evolved, my co-founder and I decided to change up the C-Suite, after which I became CEO. My job mainly includes strategic planning, sales, investor relations, and prospecting, and participating in accelerators and competitions.
A recent study has highlighted that approximately 171 trillion plastic particles are polluting the world’s oceans. How is plastic waste finding its way into the oceans despite recycling efforts?
Over 95% of the plastic we consume globally goes unrecycled. There are many reasons for this, but most of all it is the absolute apathy of a vast (but shrinking) number of people on the planet towards the importance of and responsibility for plastic.
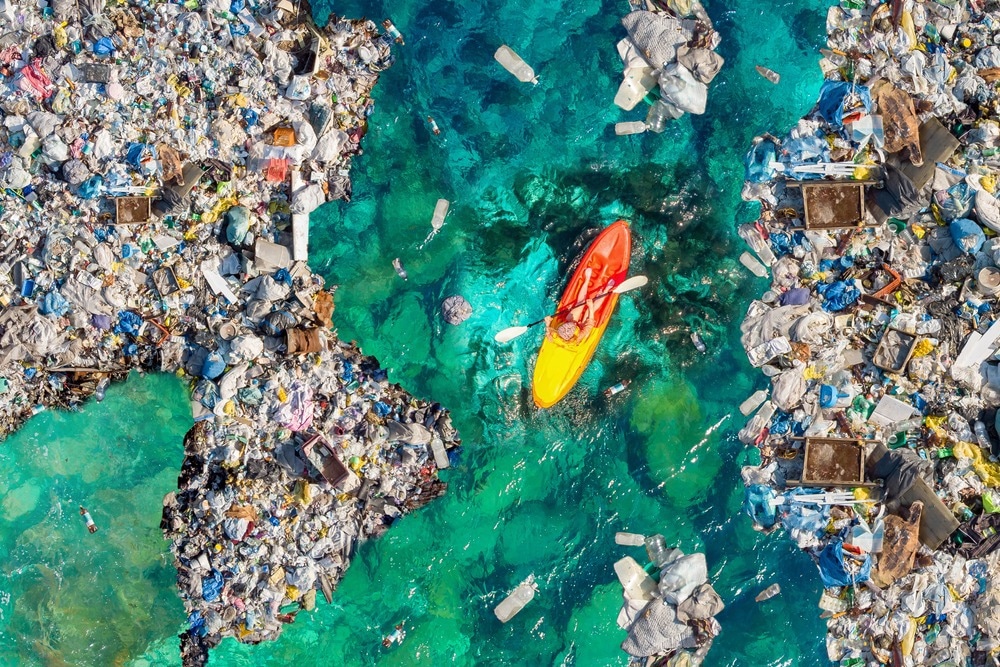
Image Credit: Parilov/Shutterstock.com
Plastic is a fantastic invention; you can make nearly anything out of it, and if cared for properly, it can be recycled and reused many times. When not cared for or used correctly, it is extremely hard to recycle and is a massive pollutant.
We need a cultural shift in how everyone views plastic to fix this. Most people separate their recycling, but everyone does it incorrectly because no one has figured out a way to simplify it, nor do much with the adequately cleaned and sorted plastic.
What challenges do we face in terms of polymer recyclability?
Everyone treats plastic poorly, starting with corporations, big and small. Many people do not have a choice in what they buy, and they buy the cheapest or only thing available. That is why I despise the idea of “the green premium”. If your solution costs more, you are cutting an enormous swathe of the population out of your potential buying pool, so they will keep using the same inexpensive, unsustainable item. That is the fault, primarily, of small businesses because it is hard to grow when you cost more than the competition.
Big businesses, impact-wise, are the worst offenders. They mix base polymer materials (nearly impossible to recycle), add toxic additives, and permanently adhere mixed materials. This is all done at a super-industrial scale. Most consumers would love to demand better. However, because these companies are solely beholden to the profit maximization motive, public opinion makes little difference—especially now in our Post-Accountability Era.
The burning, dumping, and landfilling of plastic is an existential threat, and the lack of governmental policies for reducing this is a terrible danger to our current way of life.
We should standardize and regulate the types of plastic produced internationally, control which plastics can be mixed with others and for what purpose, and limit the types and composition of additives to a specific set with a process of approvals for innovations.
Governments could mount social campaigns to the point of global ubiquity to educate the entire species on how to treat and properly dispose of different plastics.
Nations should hold billion-dollar competitions to see who can develop the next fantastic plastic and recycling method (and it would have to be both).
Lastly, we need national and international federally funded plastic recycling infrastructure. Most of our recyclers today lack the equipment to separate or reprocess most plastics accurately. As a result, most must pay for secondary transport for the unwanted plastics to the dump, with only around 5% of plastic being recycled.
With federal funding for and ownership of centralized plastic processing facilities and a massive awareness campaign to help people clean and sort their plastic correctly, we could lay waste to this problem. Cities could create public revenues by having centralized recycling as a service and creating logistics jobs to get the more complex plastics to the state-level advanced recycling facility.
What does Applied Bioplastics bring to the sustainable plastic industry?
Applied Bioplastics decarbonizes the plastic industry and how durable, long-service life polymers are made. We have figured out a way to produce durable plastics up to 25% cheaper, and reduce emissions upon creation (embodied carbon) and microplastics (at end of life) by as much as 85%. We are super scalable because we use standard equipment.
We provide a new pathway for manufacturers to make progress on their climate action commitments without sacrificing cost or functionality. Our technology broadly applies to most industries that make and sell physical products. We use non-food natural fibers grown water-efficiently on marginal land, invasive species, agricultural waste, industrial agricultural waste, and waste woods, which creates new revenue streams for waste producers while preventing methane emissions from rotting plant matter. These-low cost sources and our inexpensive treatment process enable us to offer our plastics at prices comparable to legacy petrochemical products in most markets.
Applied Bioplastics has designed non-biodegradable plastics that degrade around 10x faster than petroleum-based plastic.
Applied Bioplastics - The Future of Manufacturing
Video Credit: Notionhive/YouTube.com
Please discuss any key products Applied Bioplastics has developed and the industries they are most related to.
We have two main product lines, BioFi and BTTR Board. BioFi encompasses our licensable IP on the compounding of natural fibers into durable biocomposites, the grades of plastic we have available for sale (currently offering polypropylene and polyethylene pellets), and the cellulosic filler material.
BTTR Board stands for BioThermoseT Resin Board, and is a more straightforward composite material made from roughspun cloth, thermoset resin, and our additive package. This flat or corrugated material can be created easily in any country due to the simplicity of the process. After performing the process and 1-2 hours of drying, the resulting material is ready to be cut to size and immediately used.
BTTR Board is used in the Rohingya Refugee Camp near Cox’s Bazar, Bangladesh. We envision building 50 million simple homes for those who need them over the years by licensing the process inexpensively to governments, housing organizations, and NGOs.
BTTR Board can be made quickly in an emergency, stored indefinitely in a flat-packed and easy-to-deploy format, and uses local resources and labor to produce, creating economic development opportunities.
What are the next steps for your company?
We are raising a round to service the $63 million worth of off-takers interested in our first four grades of BioFi products and to begin licensing our IP to several more licensees now that our first licensee is starting to produce revenue.
We are also working on our first major licensing deal for BTTR Board. We will open a US facility later this year, hire some brilliant folks to fill it, apply for grants, and get off to the races. It is an exciting time.
Where can readers find more information?
www.appliedbioplastics.com
https://www.linkedin.com/in/alexappliedbio/
About Alex Blum
Alex Blum is a founder, humanitarian, and award-winning philanthropic filmmaker.
Alex has a long history of creating significant value for companies large and small, including Oracle, Amazon, and ThousandEyes (now part of Cisco), and for the past five years, has been a leading voice in the bioplastics industry.
Alex lives in Austin, Texas, where he leads Applied Bioplastics as its CEO, making decarbonized plastics for manufacturers and refugee housing for some of the world’s most vulnerable populations.
Disclaimer: The views expressed here are those of the interviewee and do not necessarily represent the views of AZoM.com Limited (T/A) AZoNetwork, the owner and operator of this website. This disclaimer forms part of the Terms and Conditions of use of this website.