Numerous industrial processes and manufacturing applications necessitate highly precise gas analysis techniques to enhance workplace efficiency, product quality, and overall safety. However, conventional methods like gas chromatography (GC) and GC mass spectrometry (GC-MS) often have slow results and high maintenance costs.
To address these challenges, Thermo Fisher has introduced an innovative technology, the Thermo Scientific™ MAX-iR™ FTIR Gas Analyzer. This cutting-edge analyzer provides real-time detection capabilities, delivering single-digit parts-per-billion (ppb) to parts-per-trillion (ppt) detection limits in industrial scenarios.
In this interview, AZoCleantech talks to Kelly McPartland from Thermo Fisher Scientific about utilizing Fourier Transform Infrared Spectroscopy (FTIR) in industrial gas analysis.
Could you provide an overview of FTIR-based gas analysis?
Fourier transform infrared (FTIR) spectroscopy is a robust quantitative and qualitative analytical method, proficient in quickly measuring numerous gases with low parts-per-million (ppm) detection limits, providing a rapid response.
The underlying principle of FTIR analysis is that each compound has a unique chemical structure, leading to a distinct infrared absorbent spectrum based on the vibration, stretching, and bending of chemical bonds.
While the spectrum remains consistent, the intensity of these absorbance bands varies with concentration, allowing researchers to establish calibrations for individual components and analyze various constituents within intricate gas mixtures.
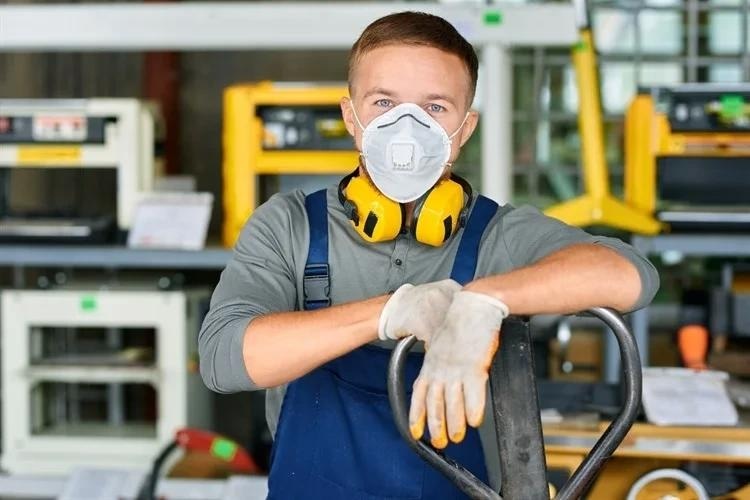
Image Credit: Shutterstock/Seventyfour
What are the main advantages and limitations of FTIR analysis?
The primary advantage of FTIR is its capability to sustain constant calibration and enable instrument-to-instrument calibration transferability.
By maintaining the sample pressure and temperature at the calibration values, a quantitative spectral library can be utilized across all identical FTIR gas analyzers throughout their operational lifespan, eliminating the need for frequent field recalibrations.
The main limitation hindering widespread industrial adoption of FTIR gas analysis has traditionally been sensitivity. Industrial applications often demand detection limits down to parts-per-billion (ppb) or parts-per-trillion (ppt), a requirement that, until recently, remained unattainable for FTIR.
What primary advantages does FTIR have over other forms of gas analysis?
FTIR is an excellent choice for process or emissions monitoring, primarily due to its remarkable speed. The gas cell maintains a constant flow with an IR beam continuously probing the gas, enabling real-time results.
In contrast, traditional gas analysis methods, such as gas chromatography (GC), involve laborious steps of collecting batch samples, transporting them, and waiting for results before incorporating them back into operations, necessitating repetition.
Comparatively, the FTIR analyzer stands out with its cost-effective ownership since it demands minimal maintenance and has no consumables. Notably, the FTIR analyzer does not require frequent calibration, making it operable by field engineers rather than analytical chemists in a lab.
FTIR analysis boasts a more comprehensive dynamic range, eliminating the need for sample splitting or dilution even when dealing with high concentrations – an issue often encountered with specific GC detectors like GC-MS.
Unlike mass spectrometry, FTIR allows the use of multiple bands for analysis, enabling the measurement of concentrations ranging from high percentages to as low as ppb levels. Users can gain structural insights and speciate isomers, a capability beyond the scope of mass spectrometry.
Due to its robustness and minimal maintenance requirements, FTIR is exceptionally well-suited for field and process applications, designed to operate autonomously for extended periods.
What advantages does the MAX-iR FTIR gas analyzer platform have compared to other systems?
The MAX-iR analyzer represents a highly optimized gas analysis system, boasting an exceptional optical throughput and featuring a 10-meter multi-pass gas cell. These attributes grant it superior sensitivity compared to other FTIR gas analyzers.
The MAX-iR analyzer offers the cutting-edge Thermo Scientific™ StarBoost™ Technology, an optical enhancement (OE) technology that significantly improves the signal-to-noise ratio (SNR) within a narrower spectral range.
This revolutionary OE-FTIR technology encompasses all the advantages of traditional FTIR and delivers detection limits that rival GC-MS. It is important to note that this exclusive technology is solely available through Thermo Fisher on the MAX-iR gas analyzer platform.
Another key benefit of the MAX-iR platform is its elimination of the need for liquid nitrogen, unlike many FTIR analyzers that rely on mercury cadmium telluride (MCT) detectors with liquid nitrogen cooling.
The MAX-iR analyzer chooses between a deuterated triglycine sulfate (DTGS) detector, a thermoelectrically cooled indium arsenide (TE-InAs) detector, or a TE-MCT detector.
The MAX-iR platform has a robust software package that enables seamless data acquisition and reporting automation. This software includes a quantitative gas library, facilitating effortless method switching and enabling customers to develop their methods as needed.
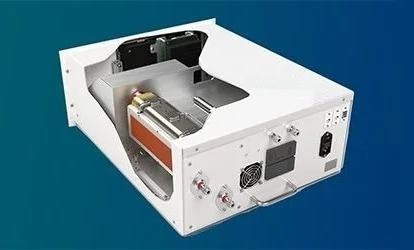
Image Credit: Thermo Fisher Scientific – Process Analytical Systems for Environmental Monitoring
Why is the MAX-iR FTIR gas analyzer appropriate for industrial environment applications?
Aside from the previously mentioned robustness and real-time results of the MAX-iR analyzer, the Thermo Scientific™ MAX-Analytics™ Software further enhances its suitability for industrial and process environments by offering automation and factory integration capabilities.
By enabling remote control through Modbus or digital inputs, the software empowers users to manage the MAX-iR analyzer efficiently. Its extensive data publishing capabilities allow seamless integration with factory data collection systems. The software includes an array of alarms and alerts for hardware diagnostics and gas concentration limits.
This proactive approach enables users to receive early warnings about upcoming preventative maintenance issues, effectively preventing potential downtime.
Integrating the MAX-iR system into an industrial environment becomes effortless, as the software ensures smooth operations for extended periods without frequent interventions. Users will be promptly alerted if hardware issues or gas concentration alarms arise.
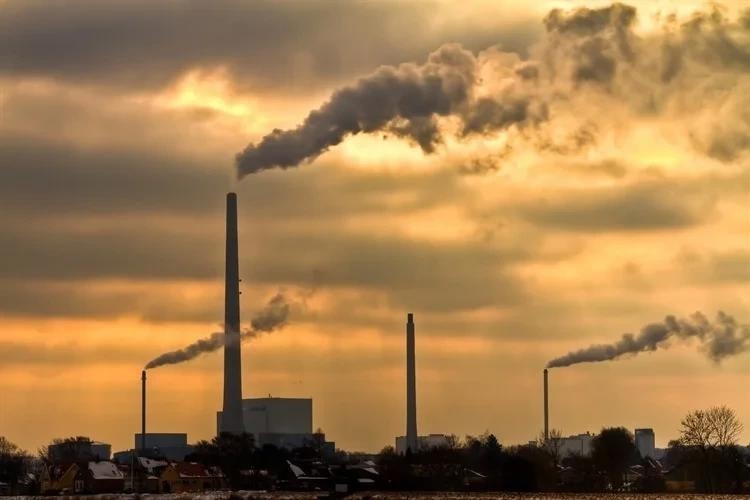
Image Credit: Shutterstock/GertLavsen
What are the current challenges in industrial gas analysis, and how does the MAX-iR platform help industry overcome them?
Beyond addressing uptime concerns, the primary challenge lies in sensitivity. Traditionally, FTIR gas analysis struggled to achieve low ppm range detection limits, leading users to opt for GC-MS due to its superior sensitivity.
The MAX-iR analyzer equipped with StarBoost technology overcomes this challenge by providing efficient real-time analysis of multiple gases down to single-digit ppb and mid-ppt levels.
Which industries rely on ultra-sensitive gas analysis?
The semiconductor industry heavily relies on ultra-sensitive gas analysis, a capability now facilitated by OE-FTIR technology. Similarly, other sectors, such as chemical manufacturing, demand high sensitivity in their gas analysis applications.
Ultra-sensitive gas analyzers are indispensable for monitoring hazardous air pollutants (HAPs) in environmental health and safety (EH&S) applications and emissions monitoring, including greenhouse gas measurements.
OE-FTIR technology is a cost-effective and timely solution for all these ultra-sensitive gas analysis applications.
How is gas analysis relevant to producing semiconductors?
Semiconductor manufacturing entails depositing compounds onto a silicon wafer, necessitating ultra-high purity gases to ensure efficient operations and a clean environment. For instance, semiconductor manufacturing utilizes ultra-high purity nitrogen for purging gas distribution channels.
Oxygen plays a crucial role in the deposition reactions, oxidizing silicon to silicon oxide. Helium serves as a refrigerant, while argon creates an inert environment for the deposition reaction.
For efficient semiconductor production, these bulk gases (nitrogen, oxygen, helium, argon) must be of ultra-high purity.
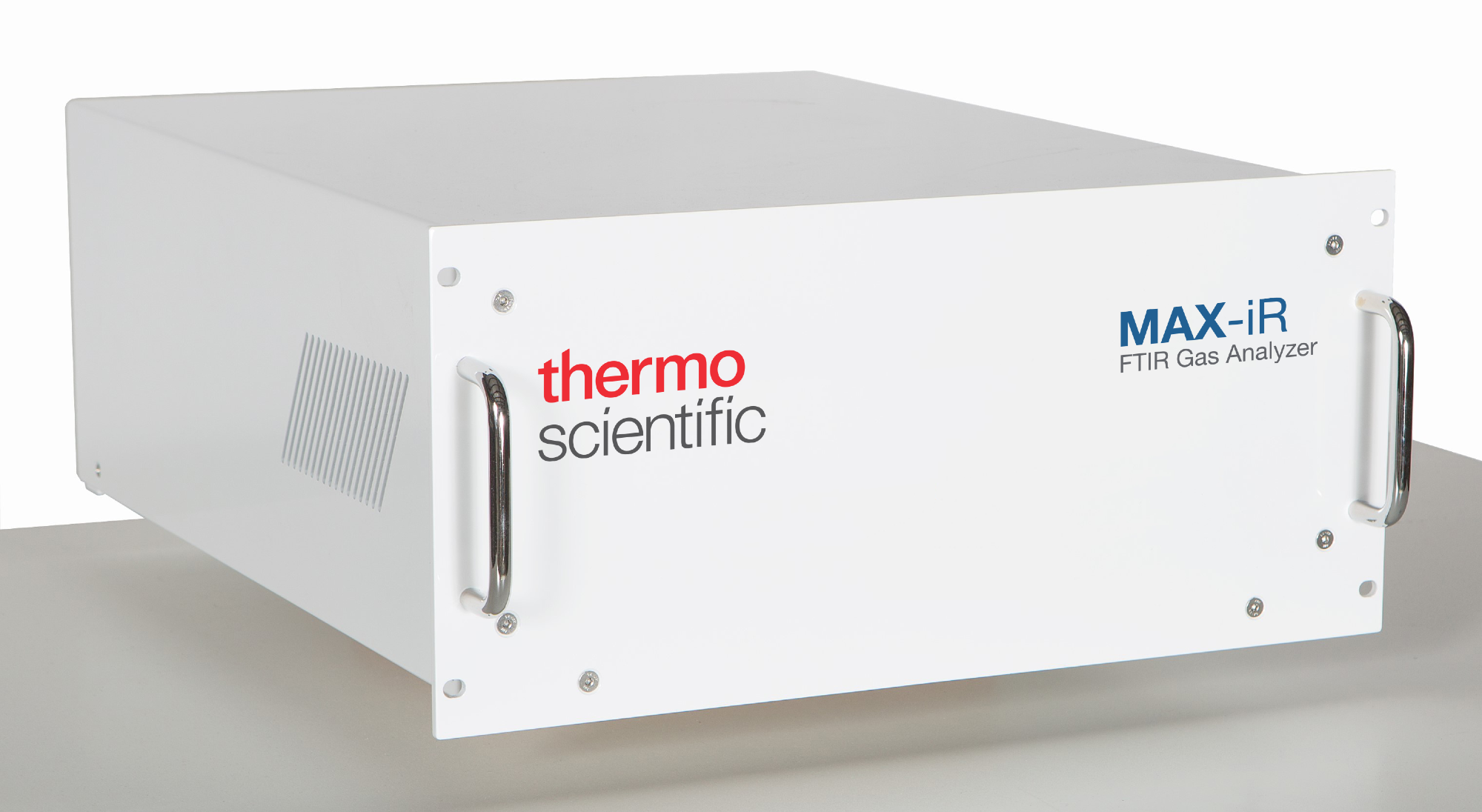
Image Credit: Thermo Fisher Scientific – Process Analytical Systems for Environmental Monitoring
Why should semiconductor manufacturers use the MAX-iR platform?
The MAX-iR analyzer's optical enhancement technology, StarBoost, makes it one of the most sensitive FTIR gas analysis systems available today, highly sought after by semiconductor manufacturers.
While cavity ring-down spectroscopy (CRDS) is commonly used for analyzing impurities in the semiconductor industry, the MAX-iR system's advantage lies in its ability to analyze multiple impurities with a single analyzer, unlike CRDS.
Previously, manufacturers might have used individual analyzers for CO, CO2, total hydrocarbon, moisture, methane, etc., but with the MAX-iR platform, they can measure all these gases simultaneously using just one analyzer, saving time and cost.
Has the increased need for emission monitoring influenced the platform’s development?
Yes, the heightened interest in emission monitoring greatly influenced the platform's development. The MAX-iR analyzer with StarBoost technology was originally designed to address challenges in emission monitoring for environmental analysis.
For example, it enables the measurement of low levels of formaldehyde in turbine emissions to comply with the US Environmental Protection Agency's (EPA) YYYY regulation.
The EPA requires limiting formaldehyde emissions to 91 ppb, an exceedingly low concentration. However, turbine flow rates are high, so even a low concentration can produce a substantial mass emission. Before this technology, no analytical technique reliably measured at such low levels.
As a result, offline techniques like method TO-11A, involving wet chemistry, were commonly used.
While an FTIR system could have provided real-time results in the field, the previous FTIR technology lacked the precision needed for a reliable pass-fail determination at 91 ppb.
The StarBoost optical enhancement was developed to lower the FTIR analyzer's detection limits for formaldehyde analysis. With this, the MAX-iR analyzer with StarBoost technology can now measure formaldehyde down to < 10 ppb, allowing users to determine whether emission results meet the 91 ppb threshold.
What were the main challenges faced during the MAX-iR system’s development?
When our journey to develop an ultra-sensitive OE-FTIR system began, we primarily focused on increasing sensitivity by expanding the spectral range. Initially, we believed that an ultra-narrow bandpass was necessary, but this approach limited the range of gases that could be measured.
As the MAX-iR platform evolved, we made significant progress with StarBoost technology, enabling us to expand the spectral range without compromising sensitivity.
Users can measure numerous gases with the latest system version while achieving single-digit ppb detection limits. Our main challenge was optimizing the system's spectral range without compromising sensitivity.
What advances and improvements are planned for the platform in the future?
We are growing the MAX-iR system's quantitative spectral library to empower users to measure an ever-increasing number of gases. Simultaneously, we constantly enhance the MAX-Analytics Software package to improve the user experience.
We plan to broaden the analyzer's applications across various industries to address diverse gas analysis challenges. Apart from semiconductor manufacturing, we see abundant opportunities within the petrochemical industry, industrial process monitoring, and potentially greenhouse gas monitoring.
About Kelly McPartland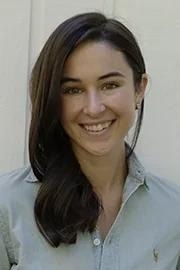
Kelly McPartland is an Applications Manager at Thermo Fisher Scientific, Gas Analysis Solutions. Holding a degree from Boston University, Kelly is an expert in FTIR gas analysis, method development, and data validation. As a senior-level technical liaison for gas analysis customers, Kelly has been instrumental in designing and managing data acquisition gas analysis software, ensuring exceptional results and user-friendly experiences. She works closely with state and federal regulatory agencies to develop Quality Assurance Plans and test methods for new technologies.
Kelly's expertise in FTIR gas analysis spans from hardware systems to method development and data validation, acquired through her work with customers and regulatory agencies.
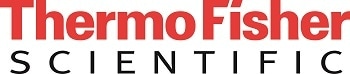
This information has been sourced, reviewed and adapted from materials provided by Thermo Fisher Scientific – Process Analytical Systems for Environmental Monitoring.
For more information on this source, please visit Thermo Fisher Scientific – Process Analytical Systems for Environmental Monitoring.
Disclaimer: The views expressed here are those of the interviewee and do not necessarily represent the views of AZoM.com Limited (T/A) AZoNetwork, the owner and operator of this website. This disclaimer forms part of the Terms and Conditions of use of this website.