Jul 25 2010
Consumers are beginning to realize that the products they use leave a lingering “environmental footprint”. They are not simply receiving this message from fringe groups like the so-called “tree huggers” but rather from mainstream media citing real-world examples of successful corporations like PepsiCo, Kraft Foods, 3M, Abbott, Dow Chemical, Johnson & Johnson, and Procter & Gamble which have already implemented far reaching sustainability measures.
This trend is apt to continue with more and more companies, either voluntarily or under market and regulatory pressures, implementing sound sustainability systems and procedures – the integration of social, environmental and economic considerations into product, process and energy systems’ design as well as the consideration of impact over the complete product and process lifecycle.
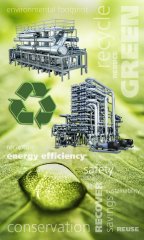
Having installed thousands of environmentally friendly process plants and systems, GEA Process Engineering is uniquely positioned to help companies meet their sustainability goals and objectives. To further emphasize our commitment to green (sustainable) engineering projects, GEA Process Engineering Inc. has created a multi-disciplined task force to efficiently and effectively handle all facets of your project. Our approach is designed to help you turn sustainability challenges into a competitive business advantages through:
- Feasibility studies
- Site surveys
- Process audits
- Conceptual designs
- Detail engineering
- Utility studies and calculations
- Project budgeting and scheduling
- Project management, equipment delivery and commissioning
The following are examples of typical sustainability issues that GEA Process Engineering has successfully addressed through our extensive process know-how and renowned engineering excellence:
- Reduced chemical and water consumption
- Water and wastewater treatment
- CIP (Clean In Place) chemical recovery using membrane filtration
- Reduced effluent and emission
- Minimized rework due to consistent product quality
- Reduced energy consumption
- through heat recovery networks
- through equipment & high efficiency motors/drives
- through efficient pipe and tank insulation
- through efficient heat transfer systems
- Increased yield through product recovery
- Recover by-products in effluents as a marketable product
- Energy optimization
- Electron beam sterilization of flat and sport caps (instead of harmful chemicals and vast quantities of rinse water)
- Zero Liquid Discharge (ZLD) solutions
- Flue gas desulphurization through spray drying absorption
- Installation of advanced automation systems to boost production efficiency, product traceability and enable repeatability