May 14 2015
Maxsys is pleased to introduce the new T2 Maxsys Fuel System, a new smaller energy saving system designed for industrial burners up to 250 m3 (8,827 ft3) of gas per hour. Like its larger counterpart the T1, which has been successfully employed on a variety of energy intensive applications on much larger burners, the new unit guarantees annual savings in fuel consumption of 5%, with a corresponding reduction in CO2, VOC, almost eliminate CO. Most users report higher savings, in the range of 6%-9%.
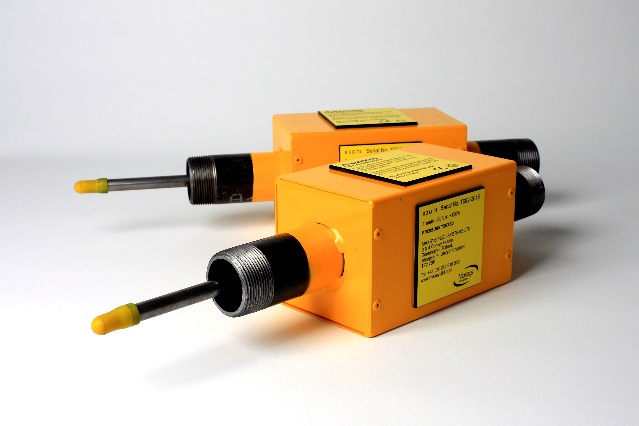
Drawing on his experience of design and development of the large T1 System and his knowledge of large combustion applications, Keith Bowden, Head of Operations at Maxsys Fuel Systems, was aware of many applications among high energy users with multiple burner configurations. “Large industrial ovens in the food industry or paint ovens of automotive components, for instance, use vast amounts of energy with ovens having multiple burners rather than a single unit,” said Keith. “To provide a much needed industrial energy solution for those types of applications, we developed the T2. The product can easily be retrofitted to a range of pipe sizes by the use of adapters in both BSP and NPT.”
Keith has been involved with a number of installations at large industrial plants worldwide such as Ford Motor Co, Union Papertech, Arkema, Dow Chemical and Croda Chemical. “Savings can be maximized by optimizing factors such as configuration and location of the System,” noted Keith.
Once the magnetic technology was prototyped, initial units were designed, manufactured and tested thoroughly by major clients in the food and automotive sectors. Successful early projects on bread ovens, paint ovens and fluidized bed dryers have led to multiple application orders.
About Keith Bowden
Keith Bowden has been involved with the development of Maxsys Fuel Systems from the beginning in 2004, and since 2008 has worked closely with Dr Generalis and his team at Aston University (UK). Dr Generalis helped the Maxsys team improve the performance of the technology and demonstrate to customers how they can reduce fuel use by at least 5%. With a strong background in combustion, Keith worked for companies such as NA-Stordy, Nu-Way and Aerogen, where he established flame treatment as ‘best practice’ before joining Maxsys.
Keith is driven by the prospect of improving energy efficiency and the development of new combustion techniques. Keith comments, “Early on, the guarantee of energy savings proved to be very popular across many industries faced with the ever increasing cost of fuel. It’s now considered essential in energy intensive industries like paper making or mineral drying where the fuel is a large proportion of the cost.”
Keith continues to head the Maxsys Operations team today, making sure the Maxsys Fuel System technology is engaged in a process of continuous improvement. “Working with the design and development team, our goal is to achieve continuous product improvement.” Keith Bowden’s profile can be viewed at http://www.maxsysltd.com/company/the-team