Jun 6 2019
Many modern plastics, rubbers and ceramics cannot be recycled, but new polymers made from waste sulfur are promising to solve one of the planet’s biggest recycling problems – and even create new industries of the future.
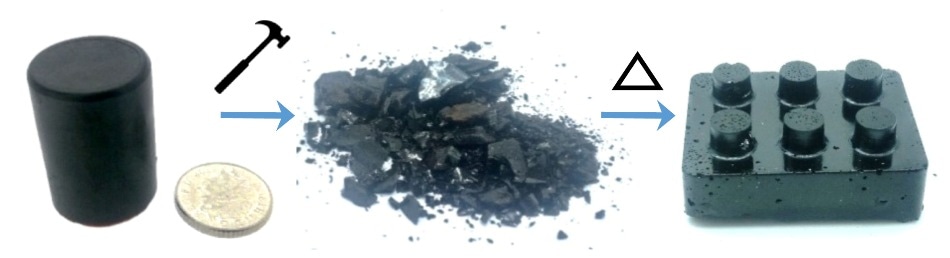
Researchers around the world have taken the next step to develop a range of these versatile and recyclable materials by controlling and improving their physical and mechanical properties to make them closer to scaleup for manufacture.
Sulfur polymers are already being used in next-generation batteries, IR imaging (such as night-vision lenses), environmental remediation, and agriculture, but it has been difficult to control the hardness, flexibility, colour and other key properties of these polymers.
A new study reported in Chemistry - A European Journal identifies design principles that can better control the properties of these polymers, making them more adaptable and attractive for other types of manufacturing.
“Controlling their properties takes a big step towards these new polymers being able to replace plastics, rubber and ceramics that are currently unrecyclable,” says Flinders University’s Dr Justin Chalker, co-director of the study.
“Polymers made from elemental sulfur have emerged as versatile materials for energy storage, optics applications, environmental remediation and agriculture. It’s therefore critical that we establish design principles to control the thermal, mechanical and optical properties of these materials. This study provides a foundation stone for this endeavour.”
The research team’s goal was to establish, in a predictive way, which chemical building blocks impart which properties to the polymer.
For instance, making a polymer from sulfur, used canola oil and another low-cost industrial byproduct dicyclopentadiene (DCPD) can create several different types of materials. Add more canola oil, and it becomes a soft rubber. Add more of the rigid dicyclopentadiene molecule and the material becomes harder and more durable.
Through this research, the team was able to establish the precise compositions of monomers that impart a desired property.
For example, various polymer made from sulfur, limonene (a byproduct of the citrus industry) and DCPD at different ratios resulted in durable materials varying from soft waxes to hard glass all easily moulded into various shapes.
As another example, adding terpinolene (an essential oil found in allspice and other plant products) to the sulfur polymer turned from orange to red to black while the DCPD more shape persistent at higher temperatures.
These discoveries are important, with new optics applications emerging for sulfur polymers as lenses and optical filters in infra-red thermal imaging, night-vision lenses and LIDAR surveying methods.
This new paper – “Crosslinker co-polymerisation for property control in inverse vulcanisation”, by JA Smith, SJ Green, S Petcher, DJ Parker, B Zhang, MJH Worthington, X Wu, CA Kelly, T Baker, CT Gibson, JA Campbell, DA Lewis, MJ Jenkins, H Willcock, JM Chalker and T Hasell – has been published in Chemistry: A European Journal. (https://onlinelibrary.wiley.com/doi/abs/10.1002/chem.201901619)