IIT and the spin-off Be Dimensional collaborated on a study that found a solution based on ruthenium particles and a solar-powered electrolytic system.
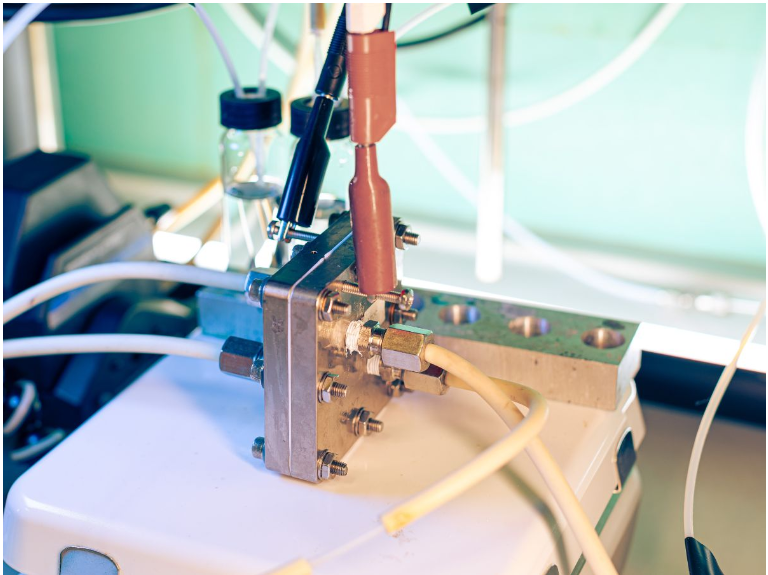
Image Credit: Italian Institute of Technology
How can green hydrogen be produced more cheaply and efficiently? Small ruthenium particles and a solar-powered water electrolysis device, it seems. The Istituto Italiano di Tecnologia (Italian Institute of Technology, IIT) in Genoa and BeDimensional S.p.A. (an IIT spin-off) collaborated to identify this approach.
The technology is based on a new family of electrocatalysts that could lower the cost of producing green hydrogen on an industrial scale. It is developed within the Joint-lab’s activities and is recently published in Nature Communications and the Journal of the American Chemical Society.
Hydrogen is regarded as a viable and sustainable energy source that can replace fossil fuels. However, in terms of its effects on the environment, not all hydrogen is created equal. In fact, the primary method used today to make hydrogen is the methane steam reforming process, which is reliant on fossil fuels and produces carbon dioxide (CO2) as a byproduct. When CO2 is released into the atmosphere, the hydrogen created by this process is categorized as “grey,” while when CO2 is captured and stored geologically, it is classified as “blue.”
These technologies need to be replaced with more ecologically friendly ones that produce “green” hydrogen, or net-zero emissions, in order to drastically cut emissions to zero by 2050. The setup (the electrolyzer) that separates water molecules into hydrogen and oxygen has a critical energy efficiency that determines how much “green” hydrogen costs.
The scientists from the joint team of this research have developed a novel process that guarantees maximum efficiency than currently existing processes in the conversion of electrical energy (the energy bias exploited to split water molecules) into the chemical energy stored in the manufactured hydrogen molecules. In addition to using renewable energy sources, such as solar energy, the team has invented the concept of a catalyst.
“In our study, we have shown how it is possible to maximize the efficiency of a robust, well-developed technology, despite an initial investment that is slightly greater than what would be needed for a standard electrolyzer. This is because we are using a precious metal such as ruthenium, ” notes Yong Zuo and Michele Ferri from the Nanochemistry Group at IIT in Genoa.
The noble metal ruthenium, which behaves chemically like platinum but is significantly less expensive, is utilized by researchers in nanoparticle form. The cathode of the electrolyzer uses ruthenium nanoparticles as its active phase, which increases the electrolyzer’s overall efficiency.
“We have run electro-chemical analyses and tests under industrially-significant conditions that have enabled us to assess the catalytic activity of our materials. Additionally, theoretical simulations allowed us to understand the catalytic behavior of ruthenium nanoparticles at the molecular level; in other words, the mechanism of water splitting on their surfaces,” noted explained Sebastiano Bellani and Marilena Zappia from BeDimensional, who were involved in the discovery.
Sebastiano Bellani and Marilena Zappia add, “Combining the data from our experiments with additional process parameters, we have carried out a techno-economic analysis that demonstrated the competitiveness of this technology, when compared to state-of-the-art electrolyzers”.
Ruthenium, a precious metal obtained in smaller quantities (30 tons annually) compared to platinum (200 tons yearly) during platinum extraction, is available at a lower cost ($18.5 per gram compared to $30 for platinum). The innovative technology involves using merely 40 mg of ruthenium per kilowatt.
This stands in stark contrast to the extensive usage of platinum (up to 1 gram per kilowatt) and iridium (ranging between 1 and 2.5 grams per kilowatt, priced at approximately $150 per gram) in proton-exchange membrane electrolyzers.
The robustness and durability of alkaline electrolyzers, a technology that has been utilized for decades, have been enhanced by the researchers at IIT and BeDimensional by the application of ruthenium. For instance, this technology was present in the Apollo 11 spacecraft, which launched humans to the moon in 1969. The newly developed family of ruthenium-based cathodes for alkaline electrolyzers is capable of lowering the cost of producing green hydrogen because of its high efficiency and extended operational life.
The scientists conclude, “In the future, we plan to apply this and other technologies, such as nanostructured catalysts based on sustainable two-dimensional materials, in up-scaled electrolyzers powered by electrical energy from renewable sources, including electricity produced by photovoltaic panels.”