Nov 10 2008
Extrusion Dies Industries, LLC (EDI) is working with solar industry innovators to help develop next-generation products that will enable solar-generated electricity to be cost-competitive with energy from fossil fuel-burning power plants, the company announced today at CPP Expo (Booth E-9414).
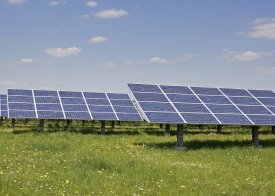
While EDI dies are already used in producing components for traditional rigid solar panels, the company has begun a program to assist designers and manufacturers in developing new flexible photovoltaic systems that can be produced as continuous webs in reel-to-reel processes typically used by converters, and can be shipped on reels for installation on rooftops by contractors. These will be complex multilayer products whose production will call for advanced film and coating technologies, according to Mark. D. Miller, manager of EDI's Market Development Group.
Among EDI innovations being explored by producers of these thin-film systems are:
- Lane coating. EDI has adapted its Liberty® slot die coating systems for applying conductive and semiconductive slurries in continuous machine-direction "lanes," alternating with uncoated lanes; in addition, the company has developed systems for simultaneously coating two sides of a substrate with up to 48 separate lanes, each 20 mm wide and separate from other lanes by 10 mm gaps. The coating fluid has been applied in register on both sides—a critical requirement for preventing short circuits.
- Microlayer film. EDI can outfit its Contour™ cast film dies with a new system, based on technology licensed from The Dow Chemical Company, which makes it possible to produce film of standard thickness yet with dozens of exceedingly thin "micro-layers." The multiple layer-to-layer interfaces create a torturous path for gas molecules and thus substantially increase the barrier properties of the film. This is critical for photovoltaic applications, which require barrier layers to prevent performance losses caused by infiltration of oxygen or moisture vapor.
"Though as yet little known in the solar industry, the continuous-web production methods familiar to EDI and its converter customers are a key to developing high-volume, low-cost production of solar electric systems," said Miller. "In working with solar manufacturers, EDI draws on extensive experience in other applications that require thin-gauge, optically clear, close-tolerance films and coatings with critical functionalities, including films and coatings for flat panel displays and flexible batteries—particularly relevant, since solar cells are a kind of battery."
Flat-Die Technology Provides Many Benefits for Thin-Film Solar Systems
In the familiar rigid solar panel, the energy of incoming photons is converted to electricity in cells containing two thin layers of crystalline silicon. What makes roll-to-roll production of flexible film solar products possible is replacement of the crystalline silicon with amorphous silicon supplied in high-solids slurries that can be deposited onto substrates by web-converting processes like slot die coating.
"In comparison with conventional coating methods, such as spray, roll, and spin coating, slot dies provide greater control over coating weight and distribution because they are closed systems into which coating material is pumped at closely pre-determined rates; in turn this greater control makes possible thinner coatings," said Miller.
A typical thin film solar system would include polymer films, foil substrates, and up to six active coatings, each of which would require curing and thus could not be applied simultaneously with any of the others. One possible structure, from sun-facing side to back side, might look like this: PET film with UV-block coating; EVA protective layers; PET barrier film; a multi-component PV sandwich; a spacer film; a reflective film; an aluminum foil layer; and an EVA back layer. The PV sandwich would include amorphous silicon semiconductor, electrode, and other layers, including special coatings.
For slot die coating, EDI supplies Liberty® fixed-lip and Ultracoat® adjustable-lip systems, each with different advantages; Wetware™ complete trial-size coating modules that enable companies to test-run Liberty slot dies in their own plants; and the Modular Coating System (MCS), a complete Ultracoat coating station that can simply be rolled into place on existing coating lines, eliminating hours of setup in switching from roll to slot die coating.
EDI's Contour Die is now its standard system for all cast film applications. The die is particularly valuable for critical optical and electrical applications like solar energy because it eliminates the transverse cross-sectional distortion called "clamshelling," often encountered with conventional dies, and yields a uniform layer structure in coextrusion.