Jan 6 2009
One of the first passive houses with a load-bearing wood construction of stacked board elements and facade insulation using BASF’s Neopor® has now been finished. The free-standing duplex house, located in Weinheim, Germany stands out for a stacked board wall that is visible on the inside and for the highly efficient use of the construction space, thanks to its arched roof merging with a slanted wall. The extra space and comfort were made possible by a 30 cm thick, external thermal insulation composite system (ETICS) with Neopor (EPS: expandable polystyrene). Because of Neopor's high insulating capacity, façades can be insulated with panels that are nearly 20% thinner than those made of conventional EPS. Neopor is instrumental in reducing heat losses and in lowering CO2 emissions. The certified passive house has a residual heat demand of 13 kWh per square meter per year, which corresponds to a heating value of 1.3 liters of heating oil.
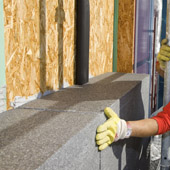
Interior insulation unnecessary
An arched roof and an east wall that is slanted by 5° towards the outside give the house the silhouette of a traditional wicker beach chair while also optimally utilizing the space. In conjunction with the smooth wood construction, the façade was insulated with ETICS made of Neopor, which is simpler and faster to install than other insulating materials. This also means that interior insulation becomes unnecessary: together with the ventilation system, the uncovered wood walls provide a comfortable living climate. As is typical of passive houses, the living areas and bedrooms are ventilated with fresh air that flows through the halls and is exhausted from the bathrooms and kitchen. The wood-aluminum composite windows are triple-glazed. The basement is made of precast concrete components and is insulated with BASF’s compression-resistant and water-repellant Styrodur® C (XPS: extruded polystyrene rigid foam panel) that serves as perimeter insulation under the foundation slab and in the area in contact with the ground.
All of these measures contribute towards making this house largely independent of fossil fuels. The total demand for primary energy for hot water, heating and auxiliary power amounts to 118 kWh per square meter per year, distributed over two residential units covering around 250 square meters. The energy that is still needed for heating and hot water is generated by a compact heat pump and ground-source heat pump baskets; the sides of the house facing the front and the yard supply most of the solar heat. Extra pipes for retrofitting solar-thermal modules have been installed on the south wall.
Passive house concept: economic feasibility and climate protection
A passive house can make do without a conventional heating and air-conditioning system, yet it remains cool in the summer and warm in the winter. Typical aspects of this building style are a well-insulated building shell and a refined ventilation and heat-recovery system. The requisite energy resources are low: In certified buildings, all of the primary energy for any extra heat, for hot water and electricity has to remain under 120 kWh per square meter per year. Passive houses are not only energy-efficient but also have a palpably better living climate than conventional buildings. A current EU stipulation sets the passive house as the energy standard that will be required by law for all new buildings in the future.