Nov 25 2009
Energy efficiency is especially important when operating container terminals in order to be able to reduce operating costs. With the new generation of ECO RTG from Siemens Drive Technologies, improved control functions for the operation of rubber-tired gantry cranes are now available. The basis of the new control is the simulation of the load curve and the resulting optimized control of the diesel-electric hybrid drive. By storing braking energy in ultra-capacitors when containers are lowered and by optimizing the utilization of energy due to the new control function, fuel consumption can be reduced by approximately 70 percent.
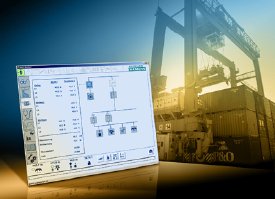
Diesel-electric hybrid drives are now commonly used in rubber-tired gantry cranes. When the container is lowered, the braking energy is stored in ultra-capacitors and made available for operation. In order to improve the energy efficiency of the system even more, Siemens Drive Technologies has further optimized the control system. The energy demand of the respective gantry crane is determined by means of simulation tools and optimized with the help of special drive algorithms. The amount of energy supplied from the motor/generator units and ultra-capacitors is monitored by applying the energy management strategy.
In order to optimize the drive system, the ECO-RTG from Siemens applies the ECMS strategy (Equivalent Consumption Minimization Strategy). Based on a mathematical model of the motor and the ultra-capacitors, the exact performance setpoint value is determined in real time for the motor and the ultra-capacitors to ensure minimum fuel consumption. This means that when required the control algorithm receives as much energy as possible from the ultra-capacitors, but at the same time it also ensures that the stored energy is never completely used up. During the entire operating cycle of the crane there is a balance between the amount of energy supplied from the ultra-capacitors and the amount of energy that is stored in them when braking and lowering.
The new control function does not only optimize energy consumption based on the known load structure. Even if conditions are changing, the energy consumption is continuously adjusted by means of approximations and permanent adaptations. If, for example, more containers than usual must be loaded, the system adapts itself to the new situation. If a standard, rule-based strategy were applied, the predefined behavior could not be changed.
By adapting the amount of energy supplied by the individual components, the overall efficiency of the system can be optimized. If, for example, the crane is in no-load mode and only auxiliary systems are consuming energy, this energy is only supplied by the ultra-capacitors and the motor is switched off.
For more information see www.siemens.com/cranes