Jan 26 2010
The Chinese government, large retailers and the Chinese packaging industry are increasingly setting high value on the environmental aspects of packaging materials for food, beverage and other consumer goods. Thus, plastics film producers are seeking innovative solutions to meet future market demands in terms of environment protection.
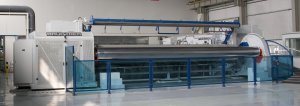
At Chinaplas 2010 (Booth E 1 B 21) Brückner Maschinenbau presents forward-looking technologies for an efficient, profitable and environmentally friendly production of various plastics films - according to the show`s theme “Green Plastics – Our Goal – Our Future”.
High performance lines for a better (energy) efficiency
Brückner`s solutions for a highly efficient and productive manufacture of plastics films show significant improvements in specific energy efficiency, output, production costs and specific investment per tons of film.
- Efficient and flexible BOPP lines up to 7,000 kg/h and up to 10.4 m wide
- High performance BOPET films from 0.5 to 400 µm, up to 8.7 m wide
- Highly efficient BOPA lines with unrivalled line widths up to 5 m
- Advanced capacitor film lines for films as thin as 0.5 µm to support the hybrid and electric driven automobile development
- Extra wide high speed CPP lines up to 6,2 m working width
- High volume PET sheet lines with chill roll or roll stack technology up to 5,000 kg/h net output for food packaging, blister packs, thermoforming applications, lid films
Stretching technology for multi-layer and high barrier films
Multi layer films can replace laminated packaging structures and help to reduce material usage, weight, energy consumption and material transport. Brückner has developed adequate line layouts allowing sequential as well as simultaneous stretching of such kind of films.
- Top economical film up to 7 layers for transparent barrier films saving raw material, converting steps and energy as well as using increased percentage of recycled material
- Opaque, density reduced barrier films for lower packaging weight
- Films with special surface polymer to achieve ultra high barrier substrate after metallization
Production lines for biodegradable film
- BOPLA thin film for various packaging solutions
- BOPLA thick film up to 350 µm for thermoforming applications
- MOPLA shrink film for sleeve applications
- PLA sheet lines for rigid packaging
Total energy management for less energy consumption and a reduced carbon footprint
- Twin screw technology saving energy: no resin pre-drying necessary, gentle resin melting and improved melt quality due to degassing ports
- TDO heat recovery system saving up to 270 kW per hour of energy by reusing exhaust heat and additionally absorbing disturbing condensate to improve film quality
- Direct drives system saving energy because gearboxes, flat belts and other transmission devices, e.g chains and shafts are not needed
- Regenerating energy in a multiple drive system
- Water cooled motors, saving air conditioning power
- Improved insulation further reducing energy waste
- Optimized recycling concept with direct flake feeding
- Additional re-extrusion via re-granulation plant avoided
- Size and energy consumption of the re-granulation plant reduced
- “Energy Audit” available for used lines, helping film manufacturers to find weak points regarding wasted energy
Brückner Servtec: Profitable and power-saving operation of existing lines
- Engineered solutions for energy savings
- Upgradings and software tools to increase productivity
- Latest audio/video communication tools for fast remote support
- Manufacturing Management System “MMS”
- Maximization of plant output and service level
- Complete transparency of the production process for all management levels
- Modern software technologies and algorithms, combined with deep film business knowledge