Fuel consumption in the marine sector is directly connected to emissions in the atmosphere and the worldwide shipping fleet is considered to contribute considerably to greenhouse gas emissions. Due to increased energy consumption, efficiency is a key issue that must be addressed in the marine industry and across all industries.
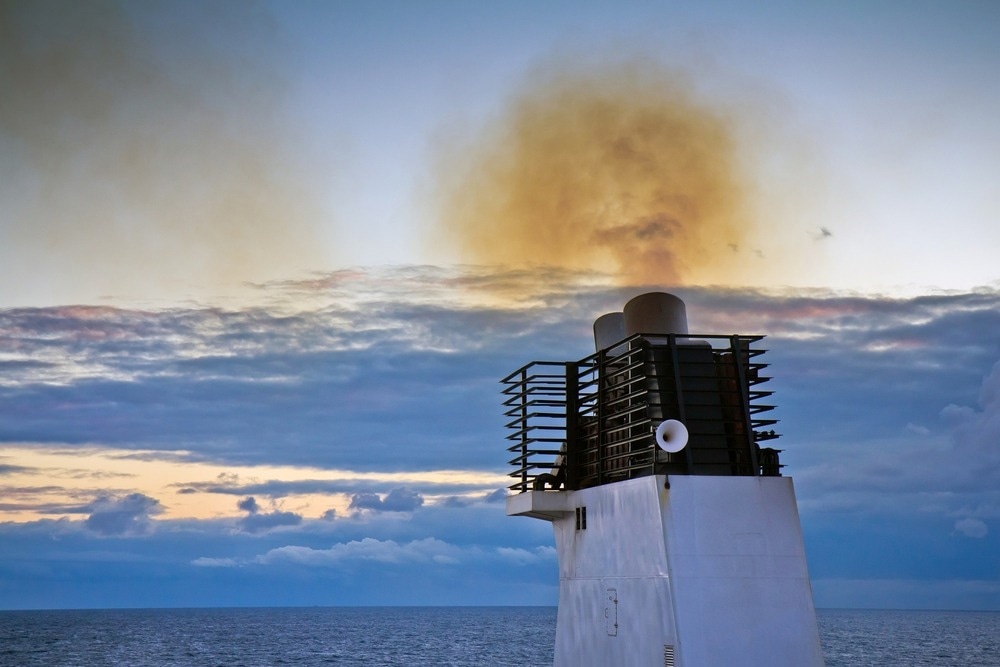
Image Credit: Alex Marakhovets/Shutterstock.com
By conserving fuel and improving a ship’s energy efficiency, the amount of greenhouse gases released into the environment is reduced. Reduced fuel consumption in ship engines is a focus in the marine sector.
Energy-saving devices, innovative equipment technologies, and improving the fuel economy of ships in operation are just a few of the options available to increase vessel energy efficiency, decrease fuel consumption, and limit emissions. Reducing fuel use and introducing new solutions are both possible approaches.
Shipboard waste-heat recovery systems are a cost-effective way to improve the sustainability of marine transportation. It creates a safe working environment, helps to meet decarbonization goals, and reduces the maritime carbon footprint. It is also simple to connect with onboard power supply systems. The high-temperature potential exists in some areas, notably aboard ships.
Thermoelectric Generators (TEG) applications can reliably and practically help with energy conversion, and TEGs are considered one of the most potential energy technologies of the twenty-first century. Furthermore, in nations such as Japan, Germany, the United States, South Korea, and Canada, thermoelectricity technology is widely used for energy generation in vehicles, space, military, and other industries.
A thermoelectric material must have a high thermopower, high electrical conductivity, low thermal conductivity, and the basic characteristics of thermoelectric materials to optimize its thermoelectric value. On ships, thermoelectric generators may operate with great efficiency on a variety of surfaces.
Specific surfaces, such as the main engine, auxiliary generators, boilers, and the sites where the ship’s waste heat is extracted, can provide the temperature differential required for Peltier to produce electrical energy.
A study looked at the prospective surfaces on which the temperature differential on the ship may occur, as well as the alternative energy potential that could be generated with the assistance of a thermoelectric generator. As a result of the calculations, thermoelectric generators were demonstrated to be an alternative energy source at the point of waste recovery aboard.
Methodology
The IMO developed emission factors based on fuel types and data from the 2020 Fourth IMO Greenhouse Gas Study. Table 1 shows the emission factors.
Table 1. The emission factors. Source: Uyanik, et al., 2022
Fuel Type |
NOX
(kg/tonne) |
SOX
(kg/tonne) |
PM10
(kg/tonne) |
PM2.5
(kg/tonne) |
CO2
(kg/tonne) |
HFO |
75.90 |
50.83 |
7.55 |
6.94 |
3.114 |
MGO |
56.71 |
1.37 |
0.90 |
0.83 |
3.206 |
An oil/chemical tanker ship was investigated as part of the study, and the ship’s main engine exhaust gas output line and jacket cooling water heat exchanger were assessed in this context. Table 2 lists the characteristics of the vessel under investigation.
Table 2. Particulars of the ship. Source: Uyanik, et al., 2022
Specifications |
Type of the ship |
Tanker |
Built year |
2017 |
Length O. A. (m) |
183.0 |
Breadth (m) |
32.20 |
Deadweight (Tonnes) |
49,900 |
Main engine type |
Slow speed |
Main engine power (kW) |
8502 |
Aux. engine power (kW) |
900 × 3 |
Exh. Gas quantity (kg/h) |
58,900 |
Exh. Gas Avg. Temp. (°C) |
324 |
The next stage was to find TEGs with characteristics that could endure these temperatures. Figure 1 depicts the methods used in the research.
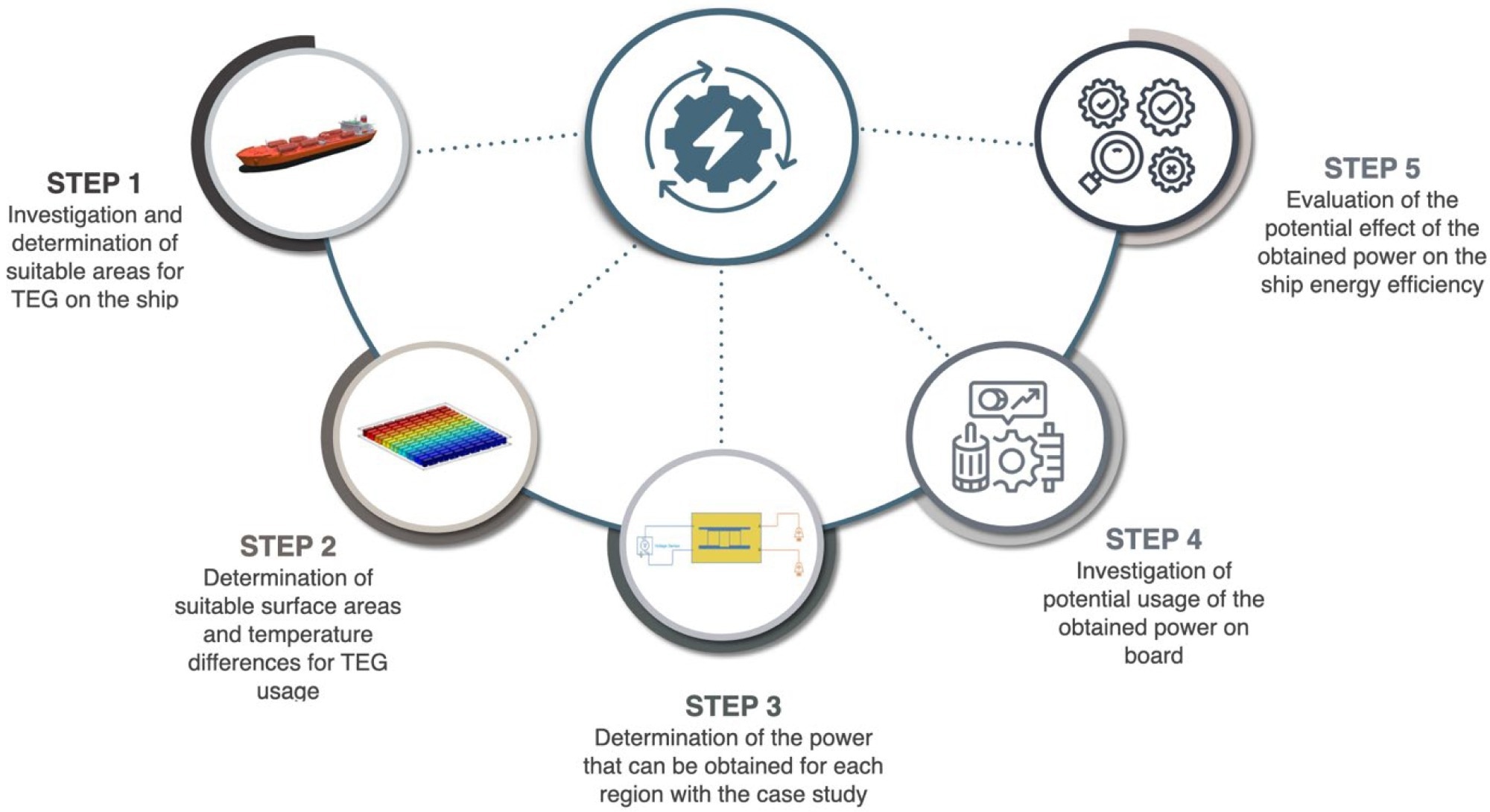
Figure 1. Methodology of the study. Image Credit: Uyanik, et al., 2022
Figure 2a shows the TEG design for the main engine exhaust outlet line surface under consideration, while Figure 2b shows the design for the jacket cooling water heat exchanger surface.
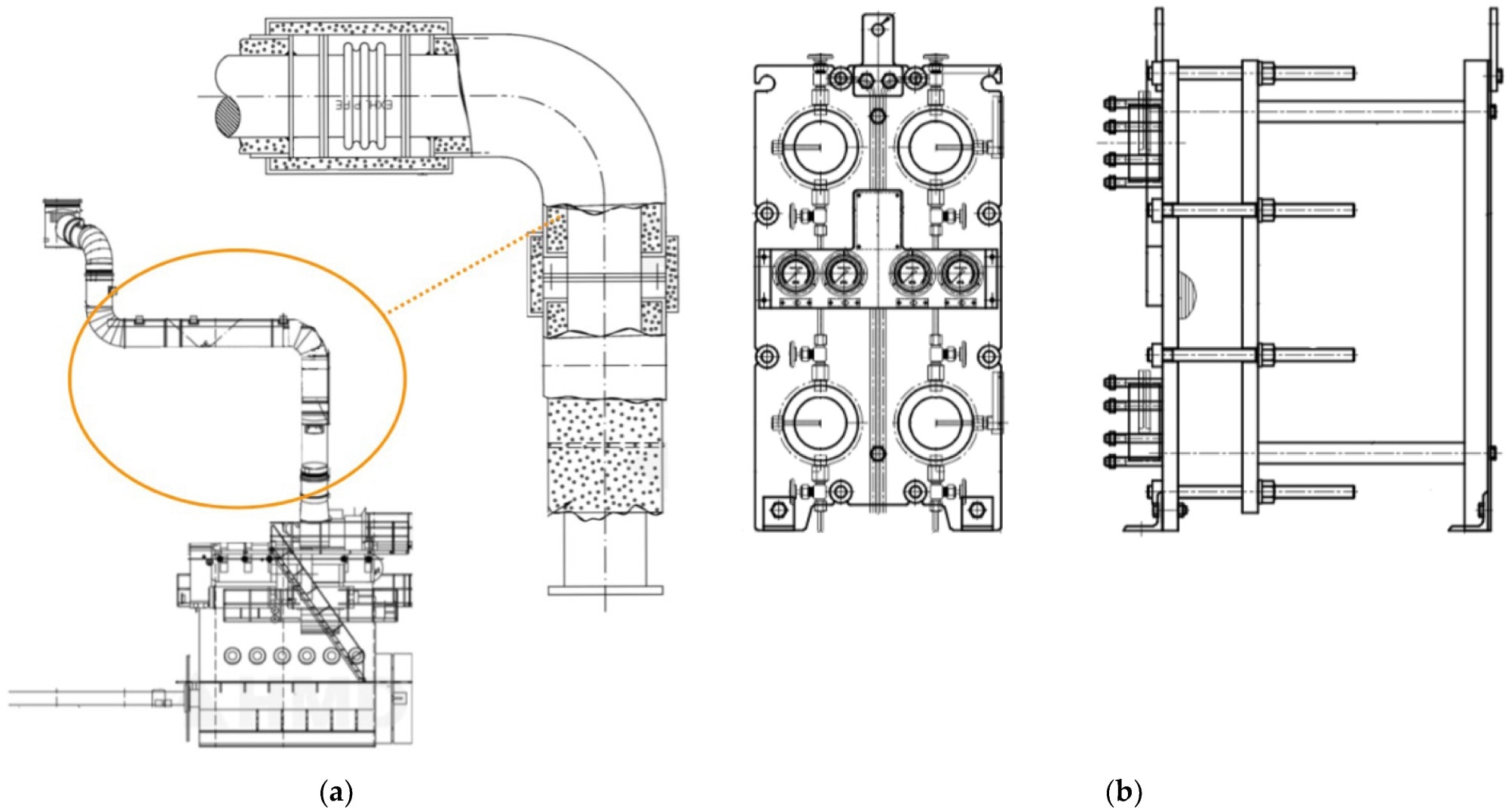
Figure 2. (a) Surface area for the TEG system designed on the ME exhaust outlet line; (b) Surface for the TEG system designed on the ME JCW heat exchanger. Image Credit: Uyanik, et al., 2022
Results
Data from the ship’s noon report, including FO consumption, generator loads, and temperature measurements, were evaluated to assess the environmental advantages of TEGs. The data from the research ship covers the voyage’s period, which was between 2020 and 2021, and assesses the effectiveness of TEGs.
Table 3 also displays the particular fuel consumptions of generators based on their different loads.
Table 3. SFOC values for aux. engines. Source: Uyanik, et al., 2022
. |
LOAD (%) |
25 |
50 |
75 |
85 |
100 |
SFOC |
207 |
193 |
189 |
189 |
192 |
Table 4 displays the total amount of fuel used by the ship’s main and auxiliary engines, as well as the costs associated with it.
Table 4. Fuel consumption and costs between 2020–2021. Source: Uyanik, et al., 2022
Fuel Type |
ME
(tonne/yr) |
AE
(tonne/yr) |
ME
($/yr) |
AE
($/yr) |
MGO |
841.59 |
171.71 |
$610,994 |
$124,660 |
VLSFO |
3120.11 |
420.37 |
$1,912,626 |
$257,685 |
The inventory of emissions discharged into the atmosphere by the ship with specifics is shown in Table 5.
Table 5. Exhaust Emission Inventory for ship. Source: Uyanik, et al., 2022
Emission |
ME
(kg/tonne) |
AE
(kg/tonne) |
Total
(kg/tonne) |
CO2 |
12,643.79 |
1890.46 |
14,534.25 |
NOX |
236.64 |
35.19 |
271.83 |
SOX |
36.29 |
4.97 |
41.26 |
PM10 |
7.72 |
1.09 |
8.81 |
PM2.5 |
7.10 |
1.01 |
8.11 |
A thermal camera was utilized to undertake a technical analysis of the ship’s temperature variations, and some examples are shown in Figure 3.

Figure 3. Thermal inspection of areas for the TEG applications. Image Credit: Uyanik, et al., 2022
Figure 4a shows the characteristics of the TEG to be utilized, as acquired from the manufacturer. Figure 4b shows the heat map of the second surface, which is regarded within the scope of the application.
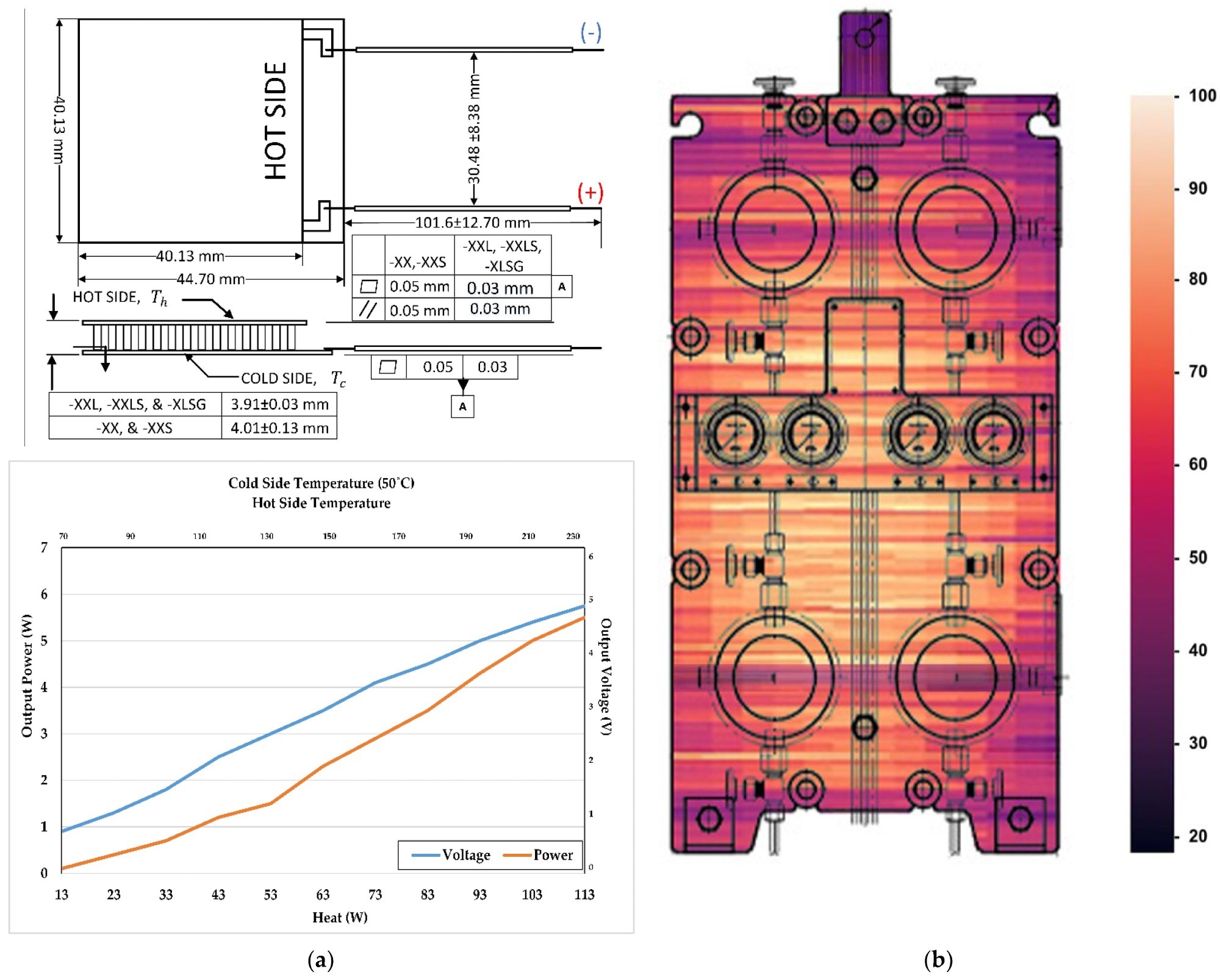
Figure 4. (a) The characteristics of the TEG; (b) Heat map of ME JCW heat exchanger (°C). Image Credit: Uyanik, et al., 2022
The power requirements of the ship’s auxiliary machinery systems (shown in Figure 5) were studied to demonstrate the influence of the intended TEG system on the ship’s energy efficiency.
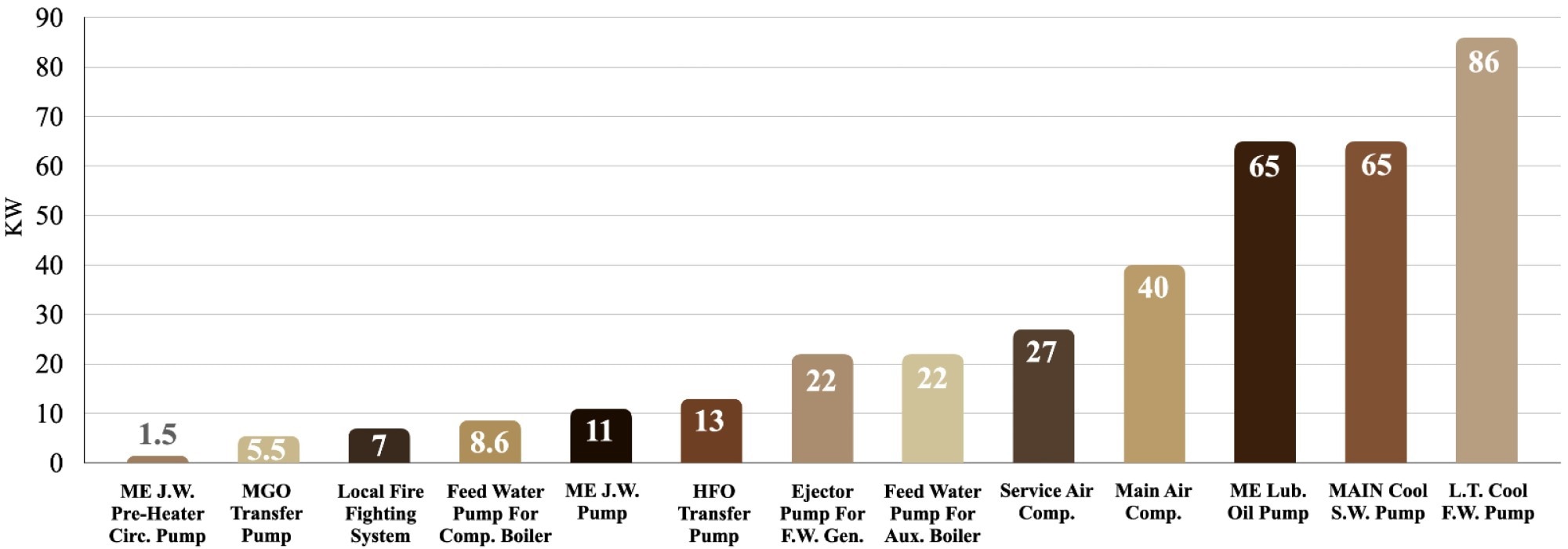
Figure 5. Power needs for the ship’s auxiliary machineries. Image Credit: Uyanik, et al., 2022
Figure 6 depicts the potential design for incorporating the TEG system into the ship’s microgrid.
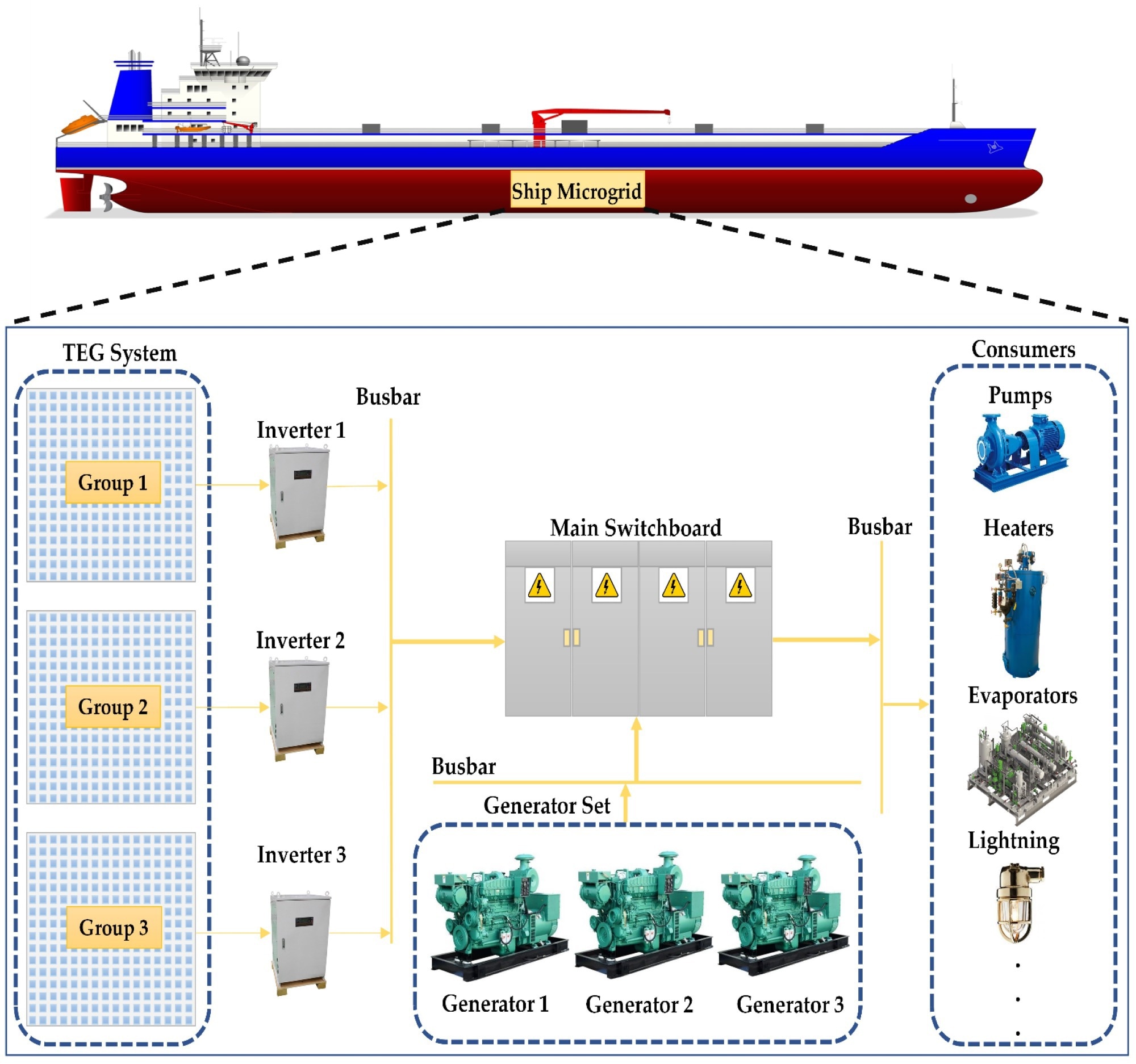
Figure 6. The conceptual design for integrating the TEG system into the ship’s microgrid. Image Credit: Uyanik, et al., 2022
Table 6 shows the cost of the TEG system, the features of the inverters that connect the system to the ship’s microgrid, and the entire design’s yearly maintenance cost.
Table 6. System installation and maintenance cost (USD). Source: Uyanik, et al., 2022
Item Name |
Quantity |
Unit Cost |
Total Cost |
Unit Specifications |
TEG [49] |
15,086 |
8.911 |
134,431 |
[50] |
Inverter [51] |
3 |
4312.47 |
12,938 |
Input Voltage = 820 VDC, Output Voltage = 440 VAC, Output Power = 30 kW |
Installation [52] |
1 |
- |
22,100 |
- |
Maintenance [53] |
Per year |
1473.8/yr |
1473.8/yr |
- |
Discussion
Solar energy, wind energy, and battery applications for marine microgrids have been the subject of several research and development projects aimed at enhancing efficiency and lowering emissions. This study offered a unique strategy for reducing fuel consumption and emissions aboard ships by employing thermoelectric generators as waste-heat recovery devices.
Furthermore, the actual data taken on board the ship were utilized to create heatmaps and an emission inventory. A mathematical model description of thermoelectric generating systems, on the other hand, was examined for the ship.
In this study, the TEG system was used to analyze existing waste-heat recovery in ships and determine its contribution to energy efficiency. Over the course of a year on the ship, TEG efficiency was measured by analyzing fuel consumption and average electrical energy produced by the generators.
Two zones on the ship were identified as having high heat efficiency, and heat maps were utilized to identify which regions were suitable for TEG installation. As a consequence of the research, critical findings for the use of TEGs on ships were acquired.
Installing TEG systems on the ship used in the case study resulted in a 2% increase in energy efficiency within a year; the increased energy efficiency would aid in the decrease of exhaust emissions as well as fuel savings, contributing to the marine industry’s long-term sustainability and green future goals.
Conclusion
The application of waste heat recovery TEG systems in the ship’s main engine exhaust gas output line and jacket cooling water heat exchanger is the subject of this study. The proposed method may be used on other parts of ships as well as different ship types, such as containers and cruise ships.
Furthermore, including additional energy-saving technologies into the suggested system, such as wind and solar, would improve energy efficiency. The development of hybrid systems, submission of a feasibility study, and cost analysis will all pique the attention of marine industry stakeholders in future research.
Journal Reference:
Uyanık, T., Ejder, E., Arslanoğlu, Y., Yalman, Y., Terriche, Y., Su, C.L. and Guerrero, J.M. (2022) Thermoelectric Generators as an Alternative Energy Source in Shipboard Microgrids. Energies, 15(12), p.4248. Available Online: https://www.mdpi.com/1996-1073/15/12/4248/htm.
References and Further Reading
- Lindstad, E., et al. (2021) Reduction of Maritime GHG Emissions and the Potential Role of E-Fuels. Transportation Research Part D: Transport and Environment, 101, p. 103075. doi.org/10.1016/j.trd.2021.103075.
- EIA Energy Information Administration (2019). Choice Reviews. Online, 44, pp. 44–3624.
- Nuchturee, C., et al. (2020) Energy Efficiency of Integrated Electric Propulsion for Ships—A Review. Renewable and Sustainable Energy Reviews, 134, p. 110145. doi.org/10.1016/j.rser.2020.110145.
- MEPC. Annex 19: Resolution; MEPC, 2011; Volume 203, pp. 1–17. Available at: https://wwwcdn.imo.org/localresources/en/OurWork/Environment/Documents/Technical%20and%20Operational%20Measures/Resolution%20MEPC.203%2862%29.pdf
- Ampah, J.D., et al. (2021) Reviewing Two Decades of Cleaner Alternative Marine Fuels: Towards IMO’s Decarbonization of the Maritime Transport Sector. Journal of Cleaner Production, 320, p. 128871. doi.org/10.1016/j.jclepro.2021.128871
- IMO. MEPC.1/Circ.684; IMO: London, UK, 2009
- IMO. Energy Efficiency Measures; IMO: London, UK, 2015; pp. 1–5
- Rehmatulla, N & Smith, T (2015) Barriers to Energy Efficiency in Shipping: A Triangulated Approach to Investigate the Principal Agent Problem. Energy Policy, 84, pp. 44–57. doi.org/10.1016/j.enpol.2015.04.019.
- ABS. Ship Energy Efficiency Measures Advisory; ABS, 2014; p. 74. Available at: https://ww2.eagle.org/content/dam/eagle/advisories-and-debriefs/ABS_Energy_Efficiency_Advisory.pdf.
- Mallouppas, G & Yfantis, E A (2021) Decarbonization in Shipping Industry: A Review of Research, Technology Development, and Innovation Proposals. Journal of Marine Science and Engineering, 9, p. 415. doi.org/10.3390/jmse9040415.
- Bouman, E.A., et al. (2017) State-of-the-Art Technologies, Measures, and Potential for Reducing GHG Emissions from Shipping—A Review. Transportation Research Part D: Transport and Environment, 52, pp. 408–421. doi.org/10.1016/j.trd.2017.03.022.
- Olaniyi, E.O., et al. (2018) Maritime Energy Contracting for Clean Shipping. Transport and Telecommunication journal, 19, pp. 31–44. doi.org/10.2478/ttj-2018-0004.
- Karatsoli, M & Nathanail, E. A (2018) Thorough Review of Big Data Sources and Sets Used in Transportation Research; Springer: Cham, Switzerland; 36, pp. 540–550. ISBN 9783319744537.
- Diesel, M.A.N. Turbo, Thermo Efficiency System. 2014. Available at: https://www.man-es.com/
- Shu, G., et al. (2013) A Review of Waste Heat Recovery on Two-Stroke IC Engine Aboard Ships. Renewable and Sustainable Energy Reviews, 19, pp. 385–401. doi.org/10.1016/j.rser.2012.11.034.
- Lion, S., et al. (2020) A Review of Emissions Reduction Technologies for Low and Medium Speed Marine Diesel Engines and Their Potential for Waste Heat Recovery. Energy Conversion and Management, 207, p. 112553. doi.org/10.1016/j.enconman.2020.112553.
- Singh, D V & Pedersen, E A (2016) Review of Waste Heat Recovery Technologies for Maritime Applications. Energy Conversion and Management, 111, pp. 315–328. doi.org/10.1016/j.enconman.2020.112553.
- Guo, X., et al. (2020) A New Hybrid System Composed of High-Temperature Proton Exchange Fuel Cell and Two-Stage Thermoelectric Generator with Thomson Effect: Energy and Exergy Analyses. Energy, 195, p. 117000. doi.org/10.1016/j.energy.2020.117000.
- Magwili, G.V., et al. (2018) Thermos Design and Assembly for Conversion of Heat to Electrical Energy Based from the Principle of Seebeck Effect Using Thermoelectric Generator and Temperature Difference of Liquids. AIP Conference Proceedings, 2045, p. 020057. doi.org/10.1063/1.5080870.
- Solanki, S.S., et al. (2018) Design and Implementation of Thermoelectric Energy Harvesting System with Thermoelectric Generator for Automobiles Battery Charging. In Proceedings of the International Conference on Inventive Communication and Computational Technologies (ICICCT), Coimbatore, India, 20–21 April; pp. 131–134.
- Wiriyasart, S & Naphon, P (2021) Thermal to Electrical Closed-Loop Thermoelectric Generator with Compact Heat Sink Modules. International Journal of Heat and Mass Transfer, 164, p. 120562. doi.org/10.1016/j.ijheatmasstransfer.2020.120562.
- Wang, J., et al. (2019) Experimental Study on the Influence of Peltier Effect on the Output Performance of Thermoelectric Generator and Deviation of Maximum Power Point. Energy Conversion and Management, 200, p. 112074. doi.org/10.1016/j.enconman.2019.112074.
- Reverter, F. A (2021) Tutorial on Thermal Sensors in the 200th Anniversary of the Seebeck Effect. IEEE Sensors Journal, 21, pp. 22122–22132. doi.org/10.1109/JSEN.2021.3105546.
- Jouhara, H., et al. (2021) Thermoelectric Generator (TEG) Technologies and Applications. International Journal of Thermofluids, 9, p. 100063. doi.org/10.1016/j.ijft.2021.100063.
- Yusuf, A., et al. (2021) Geometric Optimization of Thermoelectric Generator Using Genetic Algorithm Considering Contact Resistance and Thomson Effect. International Journal of Energy Research, 45, pp. 9382–9395. doi.org/10.1002/er.6467.
- Vostrikov, S., et al. (2021) Comprehensive Modelling Framework for a Low Temperature Gradient Thermoelectric Generator. Energy Conversion and Management, 247, p. 114721. doi.org/10.1016/j.enconman.2021.114721.
- Li, X., et al. (2021) The Influence of Peltier Effect on the Exergy of Thermoelectric Cooler-Thermoelectric Generator System and Performance Improvement of System. SSRN Electron Journal, p. 3918962. https://www.ssrn.com/index.cfm/en/.
- Zaferani, S.H., et al. (2021) Thermal Management Systems and Waste Heat Recycling by Thermoelectric Generators—An Overview. Energies, 14, p. 5646. doi.org/10.3390/en14185646.
- Zoui, M.A., et al. (2020) A Review on Thermoelectric Generators: Progress and Applications. Energies, 13, p. 3606. doi.org/10.3390/en13143606.
- Aridi, R., et al. (2021) Thermoelectric Power Generators: State-of-the-Art, Heat Recovery Method, and Challenges. Electricity, 2, pp. 359–386. doi.org/10.3390/electricity2030022.
- Araiz, M., et al. (2021)Thermoelectric Generator with Passive Biphasic Thermosyphon Heat Exchanger for Waste Heat Recovery: Design and Experimentation. Energies, 14, p. 5815. doi.org/10.3390/en14185815.
- Jia, X., et al. (2021) Performance Assessment of Thermoelectric Generators with Application on Aerodynamic Heat Recovery. Micromachines, 12, p. 1399. doi.org/10.3390/mi12111399.
- Albatati, F & Attar, A (2021) Analytical and Experimental Study of Thermoelectric Generator (Teg) System for Automotive Exhaust Waste Heat Recovery. Energies, 14, p. 204. doi.org/10.3390/en14010204.
- Von Lukowicz., et al. (2015) Characterisation of TEGs Under Extreme Environments and Integration Efforts Onto Satellites. Journal of Electronic Materials, 44, pp. 362–370. doi.org/10.1007/s11664-014-3206-2.
- Von Lukowicz., et al. (2016) Generators on Satellites—An Approach for Waste Heat Recovery in Space. Energies, 9, 541. doi.org/10.3390/en9070541.
- Moreno, R.J., et al. (2018) Harvesting Waste Thermal Energy from Military Systems. American Society of Mechanical Engineers Divison Power, 2, p. V002T12A012. https://doi.org/10.1115/POWER2018-7514.
- Dai, D., et al. (2011) Liquid Metal Based Thermoelectric Generation System for Waste Heat Recovery. Renewable Energy, 36, pp. 3530–3536. doi.org/10.1016/j.renene.2011.06.012.
- Meng, F., et al. (2017) Thermoelectric Generator with Air-Cooling Heat Recovery Device from Wastewater. Thermal Science and Engineering Progress, 4, pp. 106–112. doi.org/10.1016/j.tsep.2017.09.008.
- Chen, L.G., et al. (2016) Thermodynamic Analyses and Optimization for Thermoelectric Devices: The State of the Arts. Science China Technological Sciences, 59, pp. 442–455. doi.org/10.1007/s11431-015-5970-5.
- Qiu, K & Hayden, A C S (2008) Development of a Thermoelectric Self-Powered Residential Heating System. Journal of Power Sources, 180, pp. 884–889. doi.org/10.1016/j.jpowsour.2008.02.073.
- Fernández-Yáñez, P., et al. (2021) Thermal Management of Thermoelectric Generators for Waste Energy Recovery. Applied Thermal Engineering, 196, p. 117291. doi.org/10.1016/j.applthermaleng.2021.117291.
- Ezgi, C., et al. (2014) Thermohydraulic and Thermoeconomic Performance of a Marine Heat Exchanger on a Naval Surface Ship. Applied Thermal Engineering, 64, pp. 413–421. doi.org/10.1016/j.applthermaleng.2013.12.061.
- Sifi, I., et al. (2021) Comparison between the Thermoelectric Properties of New Materials: The Alloy of Iron, Vanadium, Tungsten, and Aluminum (Fe2V0.8W0.2Al) against an Oxide Such as NaCO2O4. Optik, 247, p. 168035. doi.org/10.1016/j.ijleo.2021.168035.
- Tan, Q., et al. (2020) Performance of Annular Thermoelectric Couples by Simultaneously Considering Interface Layers and Boundary Conditions. Applied Thermal Engineering, 174, p. 115301. doi.org/10.1016/j.applthermaleng.2020.115301.
- Aravind, B., et al. (2020) Development of an Ultra-High Capacity Hydrocarbon Fuel Based Micro Thermoelectric Power Generator. Energy, 206, p. 118099. doi.org/10.1016/j.energy.2020.118099.
- EMEP/EEA EMEP/EEA. (2019) Air Pollutant Emission Inventory Guidebook 2019. Journal of Chemical Information and Modeling, 53, 1689–1699.
- IMO. Fourth IMO GHG Study 2020; International Maritime Organization: London, UK.
- Pavlenko, N., et al. (2020) The Climate Implications of Using LNG as a Marine Fuel. ICCT Work. Pap. 2020-02. 2020. Available at: https://theicct.org/
- Marlow Industries. Technical Data Sheet for TG12-8 Single-Stage Thermoelectric Generator; Marlow Industries Europ: Weiterstadt, Germany, 2021; pp. 1–2.
- TG12-6-01L-II-VI Marlow Stock Available. The Distributor Micro-Semiconductor.Com Offer the Best Price with New Original Products. Available at: https://www.micro-semiconductor.com/products/Luminary-Micro-Texas-Instruments/SN74AHC125N
- Inverter, Solar Inverter, Home Power Inverter. Available at: https://www.inverter.com/.
- Väisänen, J., et al. (2019) Optimal Sizing Ratio of a Solar PV Inverter for Minimizing the Levelized Cost of Electricity in Finnish Irradiation Conditions. Solar Energy, 185, pp. 350–362. doi.org/10.1016/j.solener.2019.04.064.
- Väisänen, J., et al. (2019) Optimal Sizing Ratio of a Solar PV Inverter for Minimizing the Levelized Cost of Electricity in Finnish Irradiation Conditions. Solar Energy, 185, pp. 350–362. doi.org/10.1016/j.solener.2019.04.064.
- Celik, A.N.T & Muneer, P C (2015) Optimal Sizing and Life Cycle Assessment of Residential Photovoltaic Energy Systems with Battery Storage. Progress in Photovoltaics: Research and Applications, 20, pp. 6–11. doi.org/10.1002/pip.774.